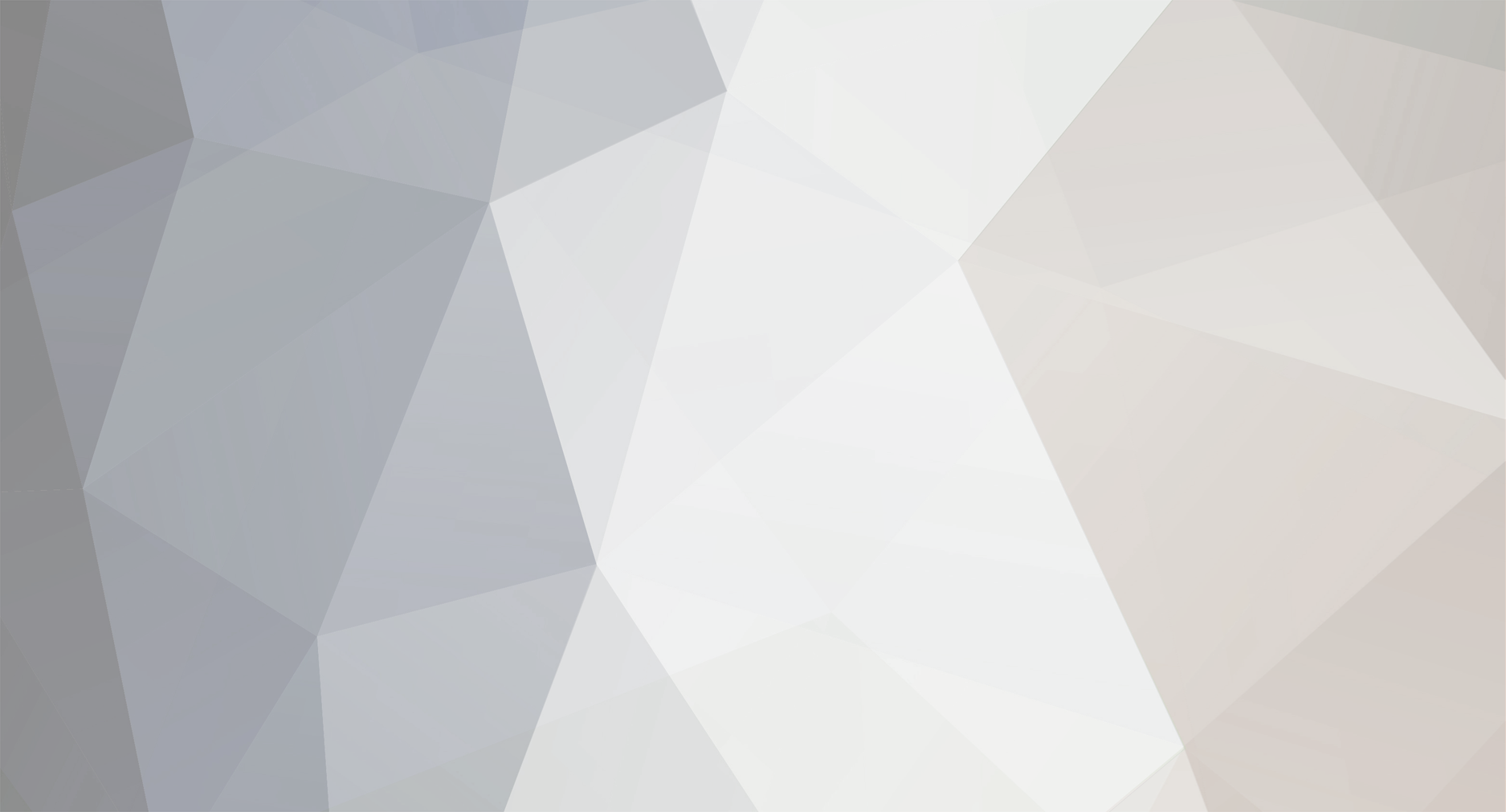
Jase hutch
-
Posts
1,282 -
Joined
-
Last visited
-
Days Won
1
Content Type
Profiles
Forums
Classifieds
Tip Site Directory
Blogs
Articles
News
Arborist Reviews
Arbtalk Knot Guide
Gallery
Store
Freelancers directory
Everything posted by Jase hutch
-
Stu, did you get the 'spare wheel mounting bracket'?
Did it fit ?
-
Hello, it arrived at parents house in U.K.
Now I'm waiting on the next friend to make a crossing.
Along with Yorkshire tea, marmite, dairy milk, ginger biscuits, my new boots, daughter's new clarkes shoes, son's hotwheels cars...
If it don't fit, I'll make it do so!
Cheers
Stuart
-
-
1
-
- Report
-