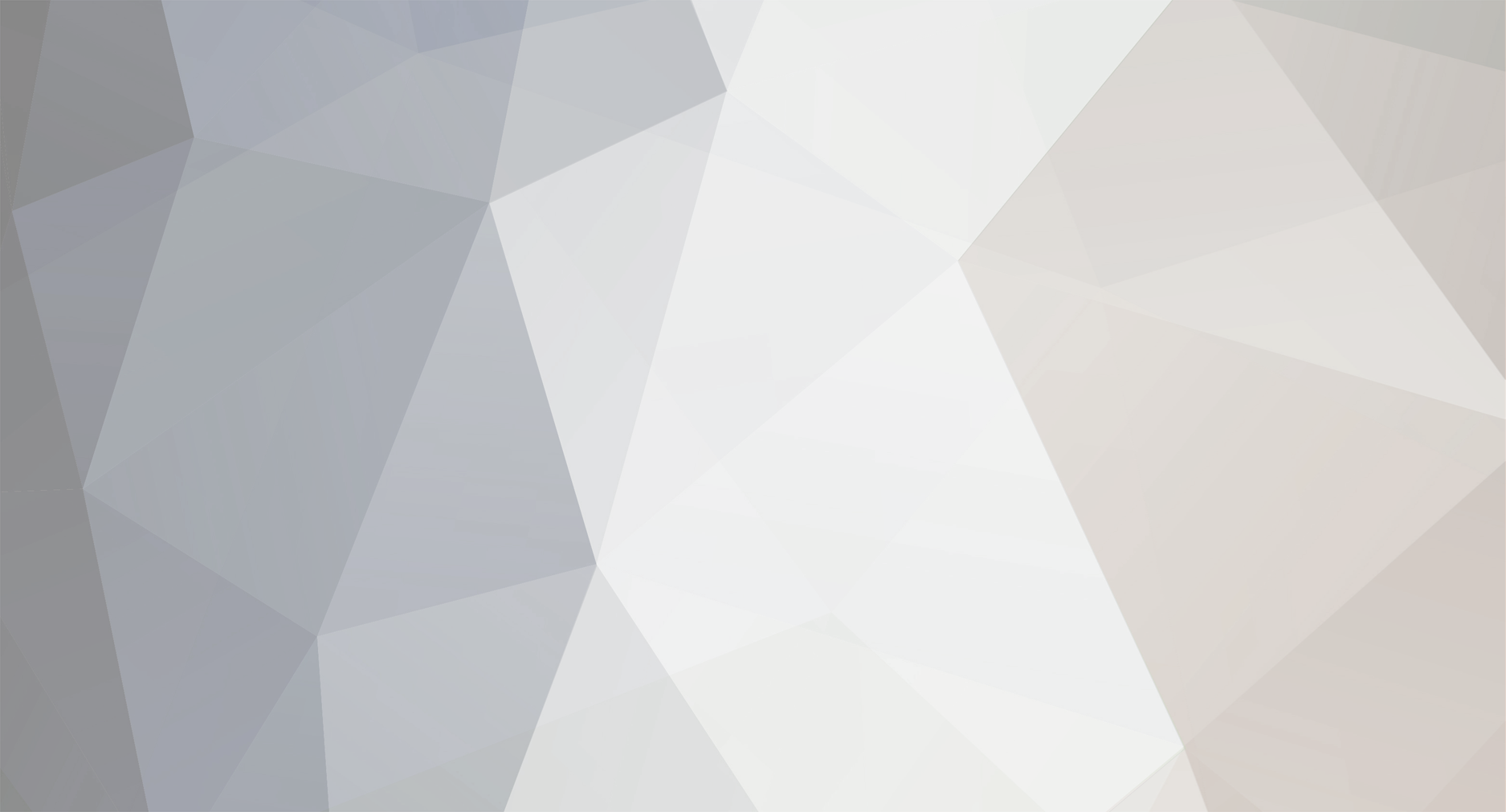
cornish wood burner
-
Posts
1,500 -
Joined
cornish wood burner replied to Woodworks's topic in Maintenance help
cornish wood burner replied to Northernarbsupplies's topic in Chainsaws
Tagged with:
cornish wood burner replied to Northernarbsupplies's topic in Chainsaws
Tagged with:
cornish wood burner replied to Northernarbsupplies's topic in Chainsaws
Tagged with:
cornish wood burner replied to sandspider's topic in General chat
cornish wood burner replied to gensetsteve's topic in Firewood forum
cornish wood burner replied to gensetsteve's topic in Firewood forum
cornish wood burner replied to gensetsteve's topic in Firewood forum
cornish wood burner replied to thecaptain's topic in Maintenance help
cornish wood burner replied to Stefan Palokangas's topic in General chat
Arbtalk.co.uk is a hub for the arboriculture industry in the UK.
If you're just starting out and you need business, equipment, tech or training support you're in the right place. If you've done it, made it, got a van load of oily t-shirts and have decided to give something back by sharing your knowledge or wisdom, then you're welcome too.
If you would like to contribute to making this industry more effective and safe then welcome.
Just like a living tree, it'll always be a work in progress.
Please have a look around, sign up, share and contribute the best you have.
See you inside.
The Arbtalk Team
We have placed cookies on your device to help make this website better. You can adjust your cookie settings, otherwise we'll assume you're okay to continue.