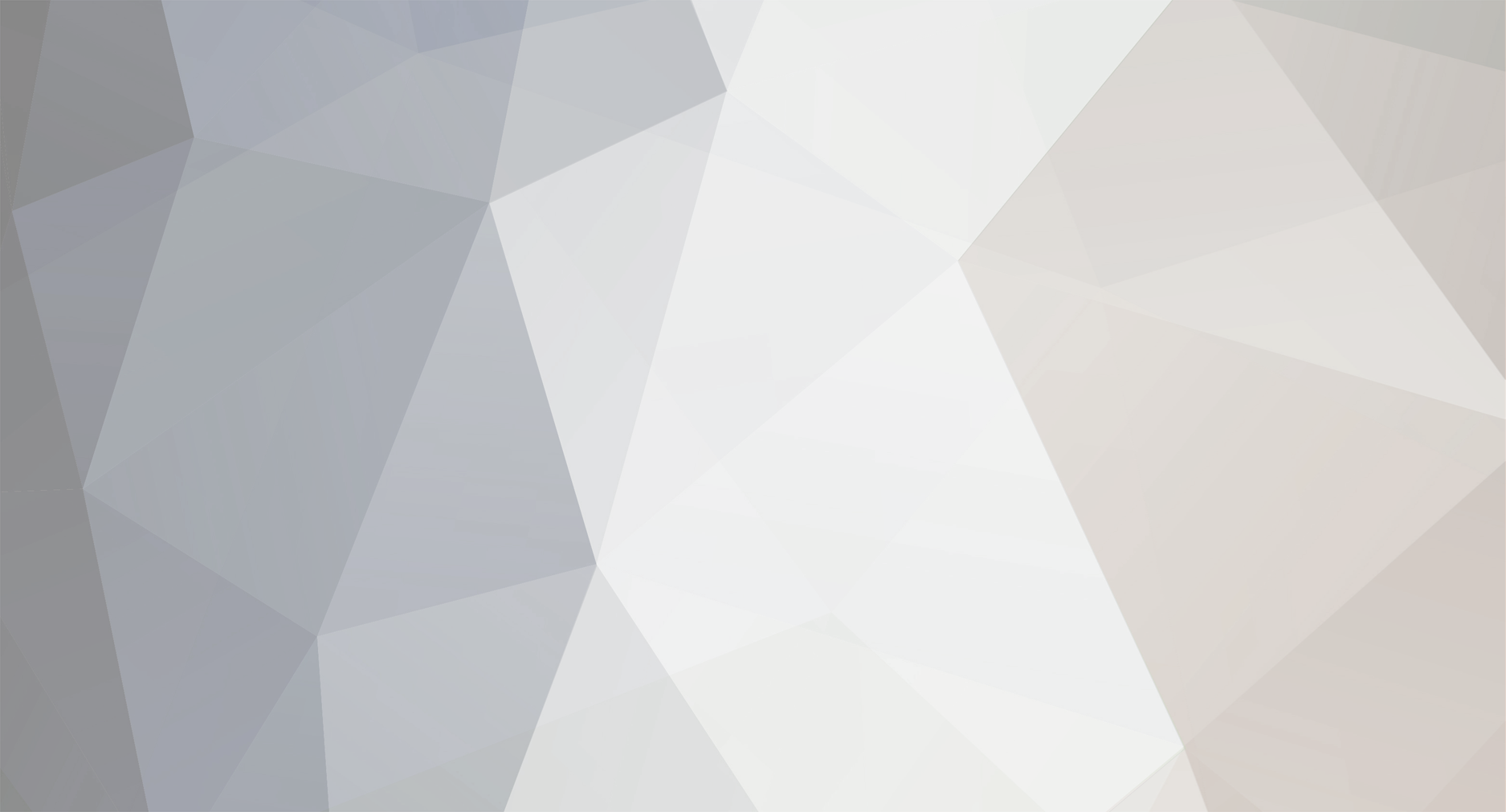
weldersunited
Member-
Posts
77 -
Joined
-
Last visited
Content Type
Profiles
Forums
Classifieds
Tip Site Directory
Blogs
Articles
News
Arborist Reviews
Arbtalk Knot Guide
Gallery
Store
Freelancers directory
Everything posted by weldersunited
-
Heavy showers and windy down here in Axbridge
-
Yes, done a fair few now- only advice I would offer is to keep everything spotlessly clean, both your working area and the ram you're repairing. Dirt and grit will only lead to the seals failing much sooner. Also if you're not sure about the assembly sequence, lay it out on the order you take it apart, that way it should help with re assembly. Good luck with it
-
I couldn't agree more with this- it is the biggest load on bollocx and is there just to make money, along with all the other accreditation schemes Chas, Exor, IPAF, etc. I may stand corrected but I think the window they allow for "time served" entrants is now gone and you need to complete an NVQ (level dependant on the card you are going for) for anything more than a visitors card- this was cetainly the case for me. It's worth noting that almost all of the imported workers eg Polish etc are only on site with a visitors card and they are freely using pertol disc cutters, operating MEWPS, driving diggers etc
-
Bullet proof tractors- good choice. A local livery yard/ small farm has a couple and believe me they willl break anything and the worst they've managed in the last 5 years are a coouple of doors! (which is good for them!)
-
It will all depend on joint preparation if it is a butt weld. If it's a fillet you need plenty of heat and filler wire to achieve penetration and fusion. A standard mig running on a 13a plug will simply not deliver this. The only single phase units I've seen that came somewhere near were run off a single phase 30amp supply and even then they were working right at their top end.
-
Good advice there and to add joint preparation is key as well as cleanliness, dont't waste your time welding on rusty/ dirty/wet/ painted/ galvanised steel without cleaning it first, it will ALWAYS come back to haunt you and you'll probably get disillusioned with the whole thing as well! I learnt most of my welding while working at a company called Dowdeswell that manufcture ploughs, the guy who oversaw me's favourite expression was "you wouldn't put a clean suit on over a pair of overalls" 15 years on i still haven't heard a better peice of advice!
-
I think we generally receive copious amounts of grief, all FOC
-
Some intersting replies here- out of interest, how mnay people on average do you guys employ? We used to have about 5 but over the years our business has grown (steelwork) to around 50 odd employees. We always took staff out for a Christmas party/ meal and free booze and a decent bonus as a thank you. As the company increased in size we found people bitching about the bonuses (they weren't small either)- he's had the same as me and i did x amount more than him etc. Also, the amount of last minte drop outs for the christmas party/ meal was unreal and the excuses were pretty piss poor considering all concerned were up for it earlier in the year. So we stopped the lot. Now we finish on a dinner time. open the bar up at the loacl pub and those that want to come and have a few drinks do so, those that don't go their own ways- no pressure either way. It's interesting to see that it's usually the same faces that come each year as well.
-
Dried food only for my dogs- mole valley farmers complete working dog food. Dogs do well on it too. Give them the occasional bone from the butcher.
-
BF- if it helps I have built myself a power rack which was basically a copy of my local gyms one- I drew it up properly so you are welcome to the drawings if it helps? I've personally squatted and benched some (what i consider!) pretty decent poundages in there so it aint gonna fail any time soon. PM me if you would like them Cheers
-
Last night had a mix of old old ash, blackthorn and willow, all split and stored in the barn since summer 2010- very toasty!
-
Good luck with it mate, you'll be better than before and smashing the weights about in no time!
-
Just replaced the thermostat in my defender 90- toasty as now and for the first time in over a year I can actually turn the heater down/ off when it gets too hot!
-
Hi Mate, I did mine when I dislocated a shoulder playing rugby. It got so bad in the end that when in certain positions the shoulder would literally fall out of the joint. I had open surgery done and was in a sling for a month, and physio for another 5 months after so in total 6 months before I could resume contact sports. The physio did however give me the all clear to be lifting weights as heavy as i liked after about 5 months. The operaation site and joint itself ached for a good year afterwards though. I'm 6 years on from the op now and it's great, stable shoulder, no ongoing problems. I believe that they also do this procedure with Keyhole procedure now and the recovery time is much quicker- something like 12 weeks, but not 100% sure- speak to your surgeon as to which procedure you'll be having. Good luck with it!
-
We have Migatronic and Thermal Arc pulse/ synergic and standard Mig sets for our day to day workshop fabrication. All are three phase units and all synergic units are inverter based so have the ability to be used for ALU, Stick welding and scratch/ lift tig setups. For site work we run Mosa welder generator sets and for smaller site jobs we have Thermal Arc inverter welders. It really does depend on what you want to do- If all your work is shed based then a decent MIG set will fit the bill perfectly, if it's repair work you have a job to beat good old fashioned stick welders (or inverter), simply due to the array of electrodes they will rub with the different materials you may encounter. As others have said though, cleanliness and joint preparation are critical to a weld's success- as with most things time spent in preparation is rarely wasted- after all, you wouldn't put on a clean suit over a pair of dirty overalls would you!
-
Another Cider drinker here- thatchers cloudy for me! Have tried some of their single variety ciders as well, Katy us a nice drop and really sneaky, just too easy drinking and before you know it you've had one too many...
-
Landrover all the way. I'v had navaras and rangers as well. now on my second defender, nearly 20 years old and just shy of 180K miles- engine and gearbox haven't yet been touched. It's brilliant and wouldn't swap it out now- just chuck the dogs in it, or fill it with wood, great for shooting/ lamping from and goes just about anywhere i point it providing the driver's ability is up to it
-
We use cranes on a regular basis for our steel erecting. All of our ercting work is sub let so contract lift and crane hire don't affect us. The main difference between the two is who the responsibilty lies with should there be an accident- contract lift should absolve you of anything going wrong ie crane toppling over etc. Crane hire gets you just that and you become respobsible for it, including sizing the thing, checkiong ground conditions are sufficient etc, providing lifting plans etc. Beware crane hire companies that offer insurance- it's only covering damage to the crane, not much else. Personally I think it's all a bit of a scam to make more money- on face value the crane supplier should have liability insurance as would the hirer and between them all bases should be covered. However some bright spark decided that they'd offer the package of "contract lift" that basically included everything that they should be doing and charge a premium for it! Unfortunately I'm not aware of any court case where this has actually been tried, so it looks like you're stuck with contract lift or take the chance with a basic hire. As regards price shop around. Pre recession crane hire companies could pretty much name their prices. Now there are an awful lot of places with cranes sitting idle that need finacing- look to be paying £6-800 tops for a contract lift with a 25 tonne truck mounted unit, certainly not into 4 figures unless the crane is particularly large. ATB Andy
-
Exactly my thinking- he only wanted to know how long we were going to be so he could plan when to get his roofers in
-
Have had a few over the years- as I have said in other posts, Arb work isn't my main source of income- that's steelwork, anyway... We quoted a local guy to install some steelwork at £x which he readily accepted. He asked us how long we anticipated the job to take- to which we replied a couple of days. We managed to install all in one very long day and the guys I had working for me really pulled it out of the bag. It ended up being one of thiose jobs that just fell together. Customer came to pay the bill and demanded a reduction because we'd done it quicker. I replied that if we had taken 3 days would he have paid the additional day? To which the answer was a resounding NO! He paid but only under threat of court action. Another one was with a very large national building contractor.... The painting specification changed to a much higher spec after the QS had placed his order with us. We advised him of the price increase and had an email back telling us to proceed with the paint as specified. Point blank refused to pay for it and claimed that the email acceptance of our price was in fact nothing of the sort and he was merely instructing us to apply the correct specification, not that he was agreeing to pay for it. Guess that these people are about everywhere in every trade!
-
Galvafroid is your best bet for this. We use all the time on new installations where the galvanising has been fettled or welding is required. If you're worried about it looking dull in contrast with the hot dip galv finish you can always get some cold galvanising spray and top coat it. Don't be fooled into thinking the spray will do the job in one though- it might look good but you will see rust coming back through in a matter of weeks.
-
Always try to quote the job- that way your customer knows how much it wil cost and can accept or decline. If they insist on and hourly rate it may be worth having a scedule of rates that you could give them ie your time per hour, cost of plant per day eg saw, chipper, haulage, disposal costs etc, travel time and rates you charge at etc- the more it's broken down the more difficult it is to argue against, just make sure that your profit margin is built into these costs, eg any hired in plant would be cost + 20%. Have yourself a daywork sheet itemising all this and have customer sign at end of day. Unfortunately try as you will to safeguard your interests there will always be one clown that will challenge everything you do. Trick is to spot them before you do the job and walk away!
-
Have you tried your local metalworking shop to see if they would fabricate some for you? We make these all the time for new build supermarkets and offices etc and depending on the spec they won't break the bank... Alternatively try googling street furniture as an on line supplier. ATB Andy
-
Hi Mate, the welding option is a great idea.... if the surrounding metals are steel as well. Think you have an aluminium casting there. If you weld the nut to the broken stud, the alu can tend to melt in the threads making the broken stud impossible to unscrew- I'v had this happen so speak from experience! As other have said, try stud extractors, centre dot the broken stud before you drill and go slowly a bit at a time, checking. That way you can alter where the hole ends up before you get too far! Good luck with it!
-
I had a Mitox about this time last year- largest one available at the time witha 20" bar. Saw was gutless and slow- I kept it one week before getting shot and replacing with a husky. Guy I sold it to does occasional fire wood (once a year!) and a few small maintenance jobs on his farm- absolutely loves it. I'm not a pro like a lot of you guys and this is not my source of income, but... I HATE not being able to get on with the job whatever I'm doing and the Mitox just didn't cut it for me. Maybe having grown up with Stihl and Husky my expectations were too high!