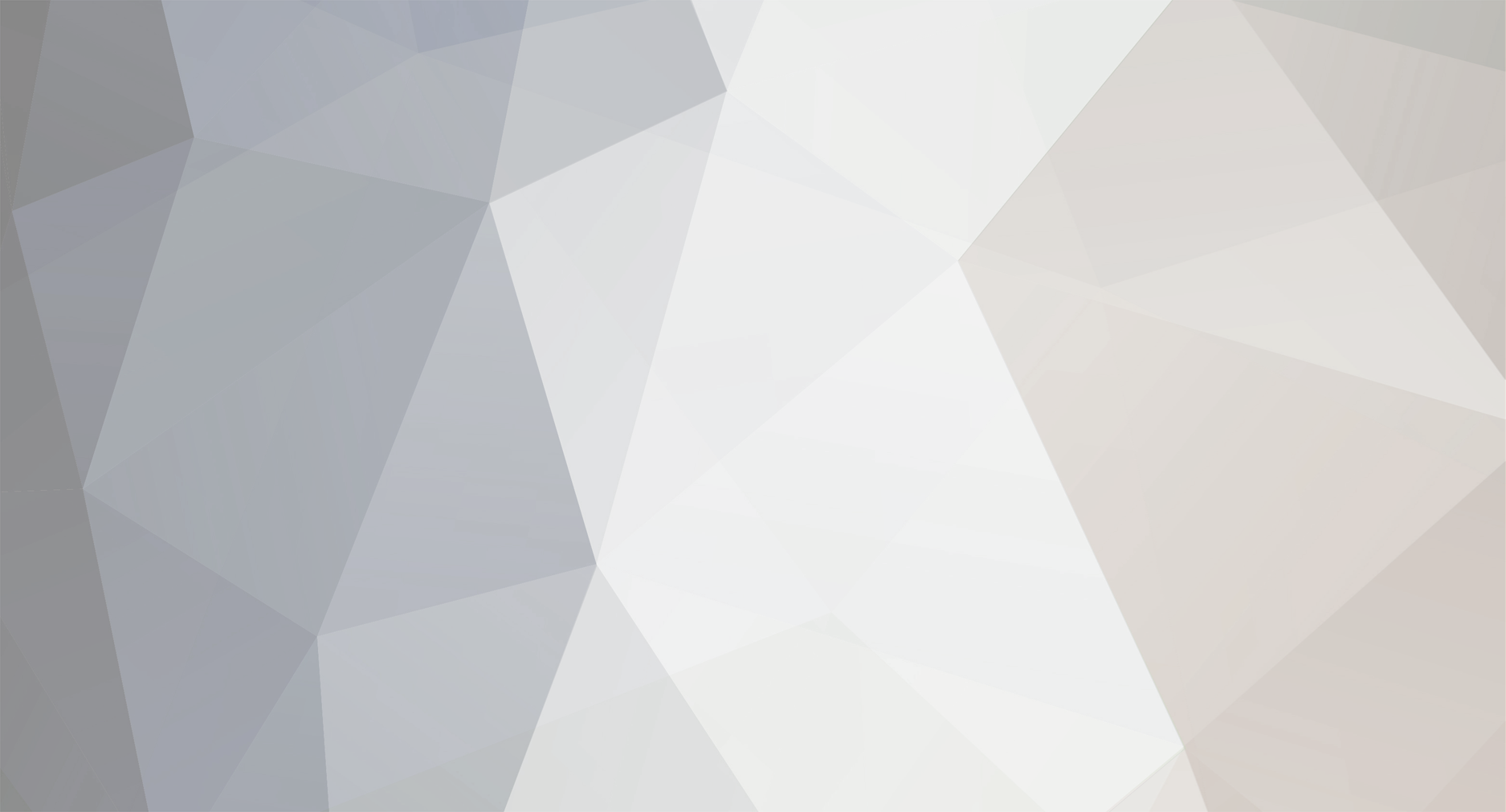
Muddy42
Member-
Posts
617 -
Joined
-
Last visited
Content Type
Profiles
Forums
Classifieds
Tip Site Directory
Blogs
Articles
News
Arborist Reviews
Arbtalk Knot Guide
Gallery
Store
Calendar
Freelancers directory
Everything posted by Muddy42
-
No need necessarily for a mityvac if its a big leak. Leaks in the crank seals and not always visible. Try a bicycle pump or blowing air from your mouth through a tube into the impulse line with everything else sealed off. Dunk the saw under water to identify the leak.
-
Have you tried a pressure test with the saw under water in a large sink? Best to apply pressure through the impulse line. When the pressure is there, rotate the crank, wiggle the impulse line and poke the intake book. In my experience, water is the best way to find stubborn crank case leaks. Then dry the saw off and try the same for vacuum (best to not do this under water). As described if both pass, the carburetor isn't providing enough fuel so clean the carb fuel gauze, clean below and check the adjustment of the needle, spray cleaner down the H and L pipes. Soaking is better for the carb than compressed air, which can damage the carb.
-
True, you could also use a kiln and be there in two weeks. I prefer a slower process that involves the wood getting rained on outside for a year then brought indoors for a year. But then I do have lots of space and a telehandler. I would love to see some proper scientific analysis of emissions from various logs that had had different treatments.
-
That would make sense if you had a serious air leak somewhere in the crankcase as as spud says. This leak makes the engine over rev at idle, putting the choke on will cut off the air, compensating somewhat. Block off the saw as described above and pressure test the saw under water. You'll find the leak easily.
-
Meths and then hot water and detergent for the parts you can remove.
-
Its all about fuel quality and burning dry wood. If you burn wood that has been split and seasoned for a few years outside then brought inside in the summer, it barely produces any smoke at all.
-
I have the mityvac pressure and vacuum kit and would recommend it. It also has a good range of bungs and tubes to help get the test set up. The key is you want to block all but one port into the crankcase which you use to introduce pressure and vacuum. I generally introduce pressure through the impulse line. I put the spark plug in. I use rubber inner tube to block the intake and exhaust port. The screws/bolts that attach the muffler or carb can be really helpful. Also dunking the pressurized saw can help reveal the source of an issue. https://www.amazon.co.uk/Mityvac-MV8500-Silverline-Pres-Metal/dp/B0002SQYUA
-
Is the carb H and L at factory settings, idle screw not engaged at all? Is the fuel line split, that could leak air too? Pull it out and try and blow through it and bend it around a bit to look for cracks. It would also be worth doing a pressure test of the crankcase. I find the best way to do this is remove the muffler, block up the intake and exhaust ports with blocks of wood and inner tube. I then send air through the impulse line.
-
You say the machines are hard to start when warm. Are you sure its pure vapour lock (fuel boiling in the lines/carb) rather than fuel delivery issues? Does loosening the fuel cap help? Is the fuel tank vent clear?
-
I've cut an old pair of chaps into strips. These hang down from my felt hat to my chest and will catch and instantly stop the chain in a kickback situation. Then you can remove the chain brake entirely, taking the weight ratio to the next level.
-
or you could use one in each hand.
-
Too late, I've ordered a puller, for £5! This gorilla whacking approach has yet to work for me. I had to borrow a puller last time. I probably have weak office fingers. Yes I have a few ideas to approach the lip (good idea about lube) I'll see what the lip looks like when the seal is off. No rush here. I am militant about pressure/vac testing which should help confirm if the seal is good.
-
What will an ash woodland look like in 10 years time?
Muddy42 replied to 5lab's topic in Forestry and Woodland management
My only experience of this is areas of Scotland that have suffered from phytophthora ramorum outbreaks to larch plantations. Here if you had forestry within a targeted exclusion zone, the FC would identify the disease (often with helicopters) and would then issue a felling order to fell all larch trees within 200m of an outbreak within two months. In practice, huge flexibility was given to the timing and forestry plans (so you could fell a practical amount) and various grants (felling restocking etc.) were available. I don't think the landowners complained, but it is sad that we now don't have larch as a diversifier against sitka spruce and other conifers that look pretty similar. Obviously this is different from dead ash because the timber has a commercial value. -
Right so it is leaking out of the clutch side crank seal. This is a Stihl Wood Boss 028 AVS. Other than this, the saw runs well, has compression and piston looks good, so I would like to try and save it. I have not replaced seals before so any advice gladly received. Is it possible to replace these seals without cracking the case? I don't like the look of the ridge (in the photo below) that you need to get the seal over. Ideally I'd like to replace both seals and buy a flywheel puller for the other side. Thanks
-
This saw wasn’t running quite right hence the pressure test. Annoyingly I suspect a crank seal is leaking. I’ll take the clutch off tomorrow to see a bit more clearly. IMG_5897.mov
-
Right so, with a new oil pump and new worm gear, the saw oils the bar just fine. So all is well that ends well, but I am still not really sure what was causing the problem. Maybe the plastic part of worm gear was worn, but replacing it on its own didn't cause oil to flow. Maybe internal surfaces of the pump were worn. Thanks for the helpful suggestions.
-
Sorry maybe a basic question, but do you use the decompression valve and the choke? Does it start any easier with aspen?
-
@pleasant Yes I can see that. It wouldn't take long for a proper hourly charge +VAT to increase beyond the cost of the new part or even a new saw. My time working on a saw is basically leisure time and I enjoy tinkering after work so my time is free. I hate to see an old saw scrapped. Then there are the retired cash-in-hand guys who aren't VAT registered who are still pricing their time like its 1970.....
-
The pinion looks fine and the arm is held tight, but i guess as the gear is plastic, it could wear. I will try the new gear with the old pump first. Yes it does throw/reciprocate a little, but maybe not enough. I’ll examine the new one before using it. thanks for all the help everyone, it’ll be Friday before I can work on this and report back.
-
What will an ash woodland look like in 10 years time?
Muddy42 replied to 5lab's topic in Forestry and Woodland management
On the plus side, ash is fantastic firewood. Blambles are a natural tree guard against deer and allow pioneer trees to reestablish themselves. Watch out for deer, hares and other browsers, these had really delay recovery of the understory. Nature will heal itself, but very slowly. You don't need to kill yourself replant all the ground in one go, but you could do small areas or plant either side of a footpath. Planting by hand on a 20 degree slope is still possible. -
Right, so I got the spindle out using @spudulike's panel pin technique, cleaned everything up (cotton buds, solvent, syringe) and blown through and reassembled. But its still not pumping oil. It shows a fair bit of resistance when reassembled and blown through with my mouth (whilst rotating the gear). I'll wait for the new pump mechanism to arrive and compare to that. Some part or the gear teeth must be worn.
-
This is making me feel guilty now! I'll try the panel-pin-punch out of curiosity, given I know I have a new pump on the way. I can compare the functionality of old and new by blowing through them. It might be worth the new pump for the oil adjustment alone.
-
Yes I have tried forcing air/wd40/solvent through every which way whilst rotating the pump gear (or wiggling it with needle nose pliers). Yes I can get a little bit of fluid to move through it, but its not great. I don't have the right punch to dismantle the spindle so I've called it quits and ordered the replacements. As described, the adjustment function is broken and the pump gear feels crunchy, something is just not right with the existing pump.
-
I have not owned this saw from new, so I cant tell if its original, but it could be. I think a new pump (and worm gear for good measure and they are cheap) has to be the next step. The lines either side of the pump are functioning fine. I have pushed a lot of air/white spirit either way through the pump so don't think there is a blockage, it must have failed or worn somehow. The loss of the oil adjustment functionality is reason enough for replacement anyway. Thanks
-
Chimney sweeping rods and brushes?
Muddy42 replied to cessna's topic in Log burning stoves and fireplaces
That's my approach. Once a year by the sweep and then I give the open fire a second clean in January. Just done it and brought out about a bucket full (including a jackdaw feather and a stick - the B@stards must have been poking stuff through the protective grill I have). I find if I don't give the open fire a second clean, the draw gets reduced and it can smoke back into the room slightly. Also the sweep won't go on the roof, so I try to get on the roof before he turns up.