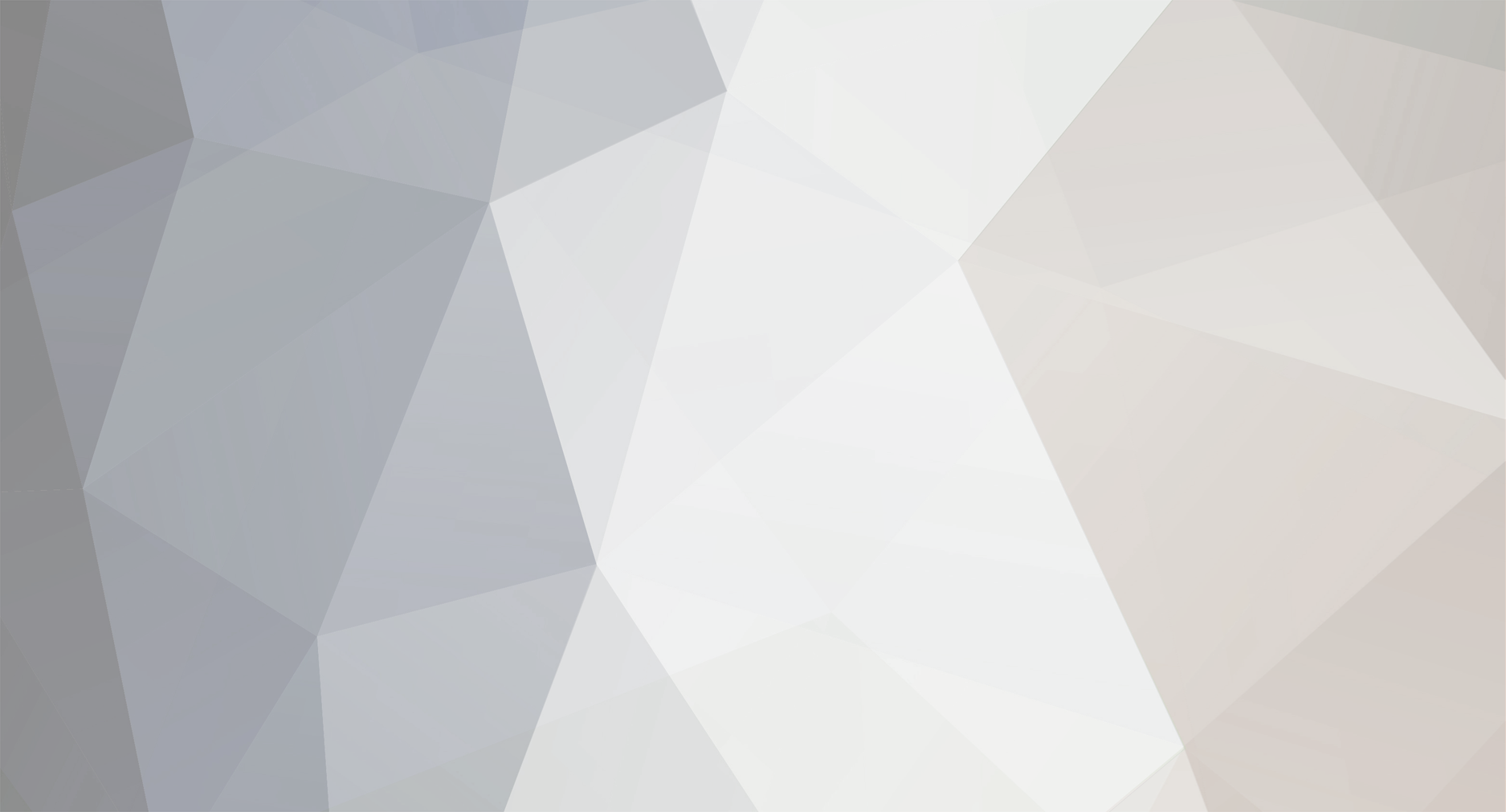
AA Teccie (Paul)
Veteran Member-
Posts
3,532 -
Joined
-
Last visited
Content Type
Profiles
Forums
Classifieds
Tip Site Directory
Blogs
Articles
News
Arborist Reviews
Arbtalk Knot Guide
Gallery
Store
Freelancers directory
Everything posted by AA Teccie (Paul)
-
The who can get most outraged at bad treework thread.
AA Teccie (Paul) replied to Mick Dempsey's topic in Picture Forum
Good evening 'Mr Dempsey'...that hurt! We advocate pruning to BS3998 as the norm but wholly accept that often 'the spec' comes first, as would appear to be the case here. I know you've often been cynical when I've been advocating 'THE' British Standard but surely it's healthy to have a balanced debate then people can make their own decisions what to do. Paul PS Believe or not I was "with you" here as, whilst not BS3998 pruning, it could be the start of a pollard regime. -
Hmmm, thought this was, in the least, frowned upon as a practice. The LPAs 'best bet' would have been to encourage removal on the grounds of 'being dangerous' and then a replacement would have been an automatic requirement.
-
Possibly agrilus beetle often associated with Acute Oak Decline (see https://www.forestresearch.gov.uk/tools-and-resources/pest-and-disease-resources/acute-oak-decline/typical-symptoms-of-acute-oak-decline/ )
-
PS - If it's of interest, we/I deliver a 1-day seminar / workshop on BS3998 which, if you're considering, offers a significant discount to members (see https://www.trees.org.uk/Training-And-Events/Course-Detail?id=E3E82C2E-094B-486A-B741-6EFFC2688CC8 for a northern even but we're also delivering in the midlands later in the year https://www.trees.org.uk/Training-And-Events/Course-Detail?id=CD29BF71-1C8D-4526-B9D6-7619D0ACBCED ) Apologies for the 'sales pitch' Paul
-
Hmmm, there are many difference with the actual finished version / document tbh so I wouldn't recommend. The 'TreeLife' option (BS3998-Concise Guide) is the best one tbh but it doesn't include the appendices...in relation to 'pruning' Table B1 (attached) is the most relevant. In relation to MoPs 'buying a copy ' to check works...never gonna happen tbh, and why more businesses don't use the document for marketing purposes when meeting with customers I really don't know...but then maybe £230 is reason enuff . Cheers, Paul
-
Tree/Shrub in LIncolnshire April 2019
AA Teccie (Paul) replied to Zico's topic in Tree Identification pictures
Probably Blackthorn as flower's, and very floriferously, before leafing...I hope -
LOLER trained arborist, looking for advice
AA Teccie (Paul) replied to Chris86's topic in Employment
Think Steve means forming a company isn't necessary, you could offer the service as a sole trader. You will indeed need 'Professional Indemnity' insurance. -
As with all / any risk assessment documentation, or indeed any H&S documentation, don't just blinded purchase / download and adopt as it is because, in reality, at that stage it's unlikely to meet the "suitable and sufficient" test. I've just downloaded their stuff and, in general, it appears to cover the main points of the RA process but does need to be read in conjunction with the 'instruction manual' (also available to download) to use it to best effect. Not sure about some of the risk ranking / rating outcomes tbh but that's always a subjective element and open to debate ("not tonight please" ) and appears to assume climbing for all tree surgery works....mmmmm. Similarly the method statement is okay but does miss out welfare arrangements, often an 'eye-brow' raiser but very relevant to construction (of which the document has a strong flavor.) Not surprisingly, if you're keen to adopt industry specific / industry produced stuff then I know an organization who can help TTFN.. Paul
-
mystery tree near me
AA Teccie (Paul) replied to se7enthdevil's topic in Tree Identification pictures
Yep, Bird Cherry -
Cryptomeria...yup
-
Think you need to educate your accountant. CIS is an abbreviation for 'Construction Industry Scheme' so if you only (currently) work for residential customers = not relevant / not applicable. Cheers,Paul PS Lots of previous threads on this subject, but where it is applicable, generally, poss take a look at https://www.gov.uk/what-is-the-construction-industry-scheme
-
National companies putting us a step back.
AA Teccie (Paul) replied to TreetopAO's topic in General chat
Hi Swinny, thanks for your question, very relevant. Many/most of the assessors are also Lantra trainers / NPTC assessors, or have been so, or are NPTC qualified themselves so understand what "good practice" looks like. They also have 'industry experience,' albeit not as extensive as many operators, and they are formally H&S qualified, i.e. NEBOSH, and SSIP registered auditors and hence understand H&S management, and operational safety, very well. Whilst a very important, and key, aspect of the assessment process, the onsite operational stuff is 1 of 4 modules to be considered and hence the assessor needs all round knowledge and experience. Cheers, Paul -
National companies putting us a step back.
AA Teccie (Paul) replied to TreetopAO's topic in General chat
Morning Andrew, hopefully a little more awake now to better respond (apologies.) The principle of sampling is great, and applied effectively is very useful to see a representative sample of, for instance, documents or process outcomes etc. Applying that principle in an office, or factory etc., environment is a fairly straight forward process. Applying it to arb teams working across a region on differing operations is logistically fair more challenging, not to say we can't / shouldn't, and as I mentioned at the 'interim' reassessment (Yr.3 of 4 Yr. cycle) where the operations we require to see is much less specific, i.e. 'aerial tree work,' we do to some extent. The initial assessment, or full reassessment (Yr.1 or the 4 Yr. cycle), is much more prescriptive in terms of the operations, i.e. "..involving rigging", and as an actual job, and hence the likelihood of multiple teams being suitably deployed is much reduced. However, certainly a very useful comment and one I will mull, as is my 'MO', over the coming miles on the road...thank you. Paul -
National companies putting us a step back.
AA Teccie (Paul) replied to TreetopAO's topic in General chat
Hi Ben, thanks for your post. Apologies for the 'mauling' but as scheme manager I'm pleased to learn the standards have been applied and assessed rigorously...but hopefully reasonably / fairly. Particularly as a participant business in the scheme ("thank you") please don't hesitate to volunteer any suggestion you may have as to how we can improve the scheme and/or the assessment process. Thank you for your last comment, quite 'insightful'...and hopefully avoiding the need to be 'hindsightful' (a strapline crabbed from Achilles but very apt relating to your comment.) ATB, Paul -
National companies putting us a step back.
AA Teccie (Paul) replied to TreetopAO's topic in General chat
Nope, 50/50 in reality, with site safety inspection(s), completed tree planting & pruning works + arb tech knowledge, plus workshop, store, yard, chip / timber storage too. With the smaller businesses this is probably 40/60 office / site as the focus is very much on outcomes and performance. Cheers, Paul -
National companies putting us a step back.
AA Teccie (Paul) replied to TreetopAO's topic in General chat
By depot / offices, i.e. at the point of service delivery. But once one depot is approved, which usually includes a Head Office audit, its difficult to control giving the impression the whole business is approved. Paul -
National companies putting us a step back.
AA Teccie (Paul) replied to TreetopAO's topic in General chat
In reality, with a reassessment visit once every two years, and a desktop review on the 'in between' years, we can only see so much and it is incumbent upon the approved contractor to self audit regularly and improve areas requiring such (this process is part of the evidence we require to see.) Long drive, just arrived home, so gonna leave it there for tonight. Regards, Paul -
National companies putting us a step back.
AA Teccie (Paul) replied to TreetopAO's topic in General chat
Hi Andrew, I'm sure had we been on that site, on that day, at that time, we would have spotted any short-comings. The incident, whilst serious, n thankfully no-one was hurt, is exceptional IME, and I'm really not sure how the assessment process would / could have taken account of what happen and the circumstances surrounding it...and therefore what we need to review accordingly. Your proposed improvement is fine in theory, and would probably work if the contractor had multiple teams operational, and if they were all undertaking the operations required by the standards, e.g. rigging, but this is often not the case. We do, at least to some extent and where possible, adopt the approach you outline, particularly at the interim reassessments where we have more flexibility, but, regardless, even the perceived "golden gang" that we allegedly see at every visit frequently present with 'opportunities for improvement.' Always open to improvements and ideas so please "keep'um'rolling" but I'm now on the road for a few hours so it might be tomorrow before I can get back to view. Thanks again for your interest in 'ARB Approval' Paul -
National companies putting us a step back.
AA Teccie (Paul) replied to TreetopAO's topic in General chat
Hi Andrew, thanks for your post...on behalf of the "arbtalk masses." Consequential to the incident Bartlett's were prosecuted by the regulator / HSE (see http://www.hse.gov.uk/ProsecutionsHistory/case/case_details.asp?SF=CN&SV=4517829 ). Thereafter we conducted a full reassessment to satisfy ourselves they had implemented the necessary improvements / preventative measures, which they actually did / completed before the HSE began their investigation into the incident. Hence they have maintained their ARB Approved Contractor status and are doubtless using this to their commercial advantage. Regards, Paul PS Scary to think the incident was over 2.5 ago.. -
National companies putting us a step back.
AA Teccie (Paul) replied to TreetopAO's topic in General chat
Thanks Ed. The primary benefit of approval, potentially, for the small business doing mainly domestic work is as a "quality mark"...but one you would need to educate the customer in the value of, and, perhaps, a way of standing out from the 'tree surgery crowd' and particularly where the crowd is of the less than reputable fraternity. Always happy to "come n take a look" . Best regards.. Paul -
National companies putting us a step back.
AA Teccie (Paul) replied to TreetopAO's topic in General chat
Hi Ed, I hope you're well. Thanks for your comment about the scheme. These contractors are often working to LA specs that are outside of BS3998 but the TO is happy and the objective is met ...hence it never formally comes to my attention, i.e. a complaint. The reality is that the value of ARB Approval in the commercial sector these days is as much about H&S etc. compliance as it is tree care standards...if not more so. In terms of being at the "top of this industry", actually, at least initially, ARB Approval sets a minimum standard for arboricultural contracting...albeit across a wide-range of requirements. The phrase 'continual improvement' is then the plan going forward...some businesses do better than others with this but I'm generally satisfied that the scheme minimum standards are maintained. As always, I happy to receive evidence of unsafe practices or poor tree care standards and I will always investigate these but in circa 75% of cases there is a valid explanation. Please don't lose faith, the majority of businesses do good work, safely, the majority of the time and the more businesses that were included in this would mean the less significant then minority becomes...or summat like that (not ignoring the problem but recognizing the scheme isn't perfect, resources are limited, and there is a reliance on the business self-auditing for the majority of time we we're not present...AND 'competent complaints' are acted upon and all are initially investigated.) Thanks for now and "happy to chat further" Paul -
Fungi at the base of a sycamore id please
AA Teccie (Paul) replied to swinny's topic in Tree health care
A wild guess really as no-one else has...a partly desiccated clump / cluster of Honey Fungus (but then more often they 'mush' rather than desiccate .) I really don't know, sorry. ...who's next with a better guess! Paul -
Sub contractor but also team leader
AA Teccie (Paul) replied to David Dobedoe's topic in Insurance Forum
As a matter of interest, well to me anyway , within 'Approved Contractor Scheme' we make EL insurance a mandatory / conditional requirement regardless of 'how' an employer engages their staff. That way it safeguards both parties...and yes, the AA. -
Sub contractor but also team leader
AA Teccie (Paul) replied to David Dobedoe's topic in Insurance Forum
"The employer" is the duty-holder and, as far as I am aware / understand, it is they who should hold the 'EMPLOYERS Liability' insurance (which is a legal requirement under the EL (Compulsary Insurance) Act 1969. I really don't see how this could be transferred to a LOSC, i.e. free-lance climber acting as a Team Leader. Cheers, Paul -
Isa Certification vs level 4 Arboriculture
AA Teccie (Paul) replied to tree man john's topic in Training & education
Edward, thank you for your reply here and you are quite right I have deviated from the OP point about ISA CA 'v' L4, which are essentially 2 quite different learning opportunities and in the OP's case clearly L4 would be the better / more suitable one. However, if I may, regarding the cost of the ISA CA 'facilitated training' between the AA and Treelife it is as follows: 1. AA Member £840.00* +VAT (for x6 sessions = £140.00 (+VAT) per session) 2. Non-AA Member £1,080.00\\8 +VAT (for x6 sessions = £180 (+VAT) per session) *includes the ISA CA study guide which is £75.00 To conclude, at the craftsman level, the ISA CA would be relevant to employers I would suggest. Regards, Paul