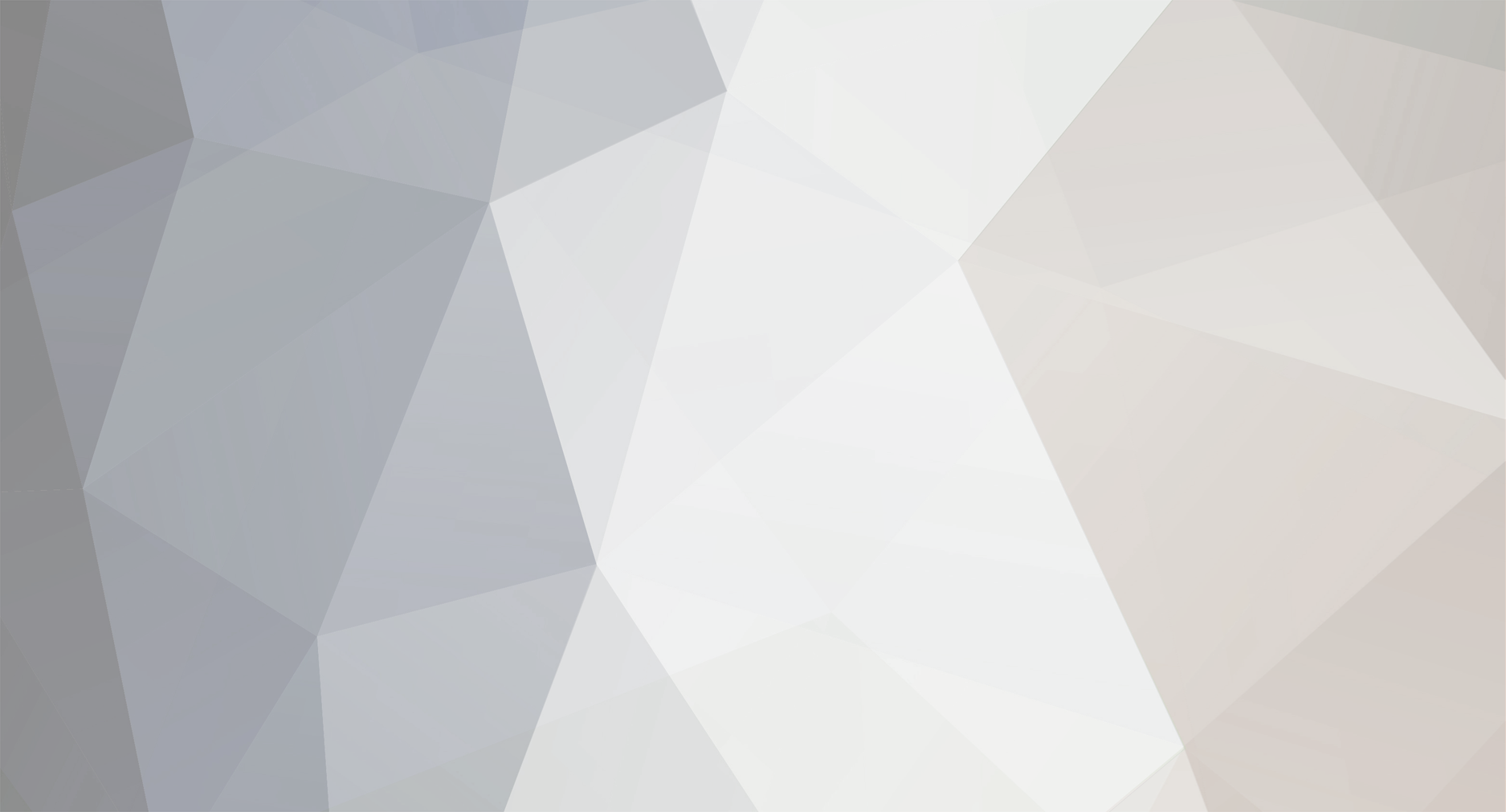
Megatron
Member-
Posts
224 -
Joined
-
Last visited
Content Type
Profiles
Forums
Classifieds
Tip Site Directory
Blogs
Articles
News
Arborist Reviews
Arbtalk Knot Guide
Gallery
Store
Freelancers directory
Everything posted by Megatron
-
Made in or after 1998 (from machine number X 39 176 186). Looks to have done a fair bit of work judging by the ribbing on the front handle hose being worn smooth. I wouldn't say it's that cheap vs a new MS660.
-
I wouldn't imagine it would work too well. Completely different geometries/designs. Probably vibrate like crazy...
-
Looks rich. Did you load the saw up for a while and then hit the kill switch towards the end of the cut before letting it return to idle? However, I never rely much on reading spark plugs by colour. The area you actually want to be reading is way down at the base of the porcelain, not what most people think. The colour can also vary depending what fuel and oil you use. Definately worth changing the green filter though. If the green one is in good condition keep it for use in wintry conditions i.e. falling snow. You want the black and silver HD2 filter, part number 0000 140 4402.
-
-
Check to see if the big end bearing cage is damaged. Personally I wouldn't reinstall that piston or small end bearing due to the trauma they have gone through. Is that a fracture on your picture, circled in red? Whatever you decide, to get the engine pan out having removed the clutch, flywheel, oil pump etc you have to remove the rear bar stud. Screw two bar nuts against each other and then unscrew the bottom one to unwind the bar stud. IMO it is only possible to reinstall the piston, crank etc into the cylinder with the engine pan removed. This is because you need to clean and de-grease the mating surfaces of the cylinder and engine pan in order to reseal with Dirko HT red sealant. Also trying to reinstall the way it looks/sounded like you were going to risks the oil seals not properly seating. When reinstalling coat the top of the piston and rings with 2-stroke oil and postion the rings such that the rings ends are either side of the locating pins. Invert the cylinder and guide the piston in(with crank attached), the cylinder is tapered to help installation, you can use a cocktail stick etc to ease the rings in past the transfer ports etc. If reusing the same oil seals, ensure they are in the same orientation as before. Next run a small bead of sealant around the groove of the engine pan and lightly smear a thin layer in the crank seal seat in the engine pan. Mate the engine pan and cylinder together ensuring the oil seals to do get clamped diagonally i.e. twisted. Without separating put the engine block back in the housing and tighten down the bolts in a diagonal pattern. When back together like Spud said a Vac and Pressure test should be carried out. Some pictures, I haven't used sealant as I don't want to reassembe. The bearings have spun.
-
This thread worries me... Have you removed the entire cylinder and pan from the housing? to end up with what is shown in the attached picture.
-
The pop-off and re-seat pressures will vary from carb to carb and are not that important. It only matters that that the inlet needle does open and reseat at a pressure of more than about 10PSI. This will ensure the fuel pump pressure does not force the needle to open under operating conditions where the pressure from the fuel pump is usually 5-7PSI. You must remove the metering diaphragm when performing this test otherwise the pressure required to un-seat the inlet needle can damage it. Also the carb should be flushed with fuel before any testing. Usually I just perform a leakage test on the carb, intact. Again flush the carb with fuel to wet the fuel passages and moisten the diaphragms. Apply a pressure of about 11PSI via fuel hose. If this pressure remains constant for a few minutes you can assume the carb is airtight. If the pressure drops; The inlet needle is usually not sealing which is usually caused by foreign matter in the valve seat or sealing cone of the inlet needle is damaged or inlet control lever is sticking. Also check the metering diaphragm for distortion and replace if necessary.
-
I have never tried with magnets on an 088/MS880 piston or cut a piston in half but the info came from a good source. Perhaps ask on Arboristsite? What model Tillotson carb does the saw have?
-
Oh, you mean the accelerator pump. Yes there are numerous accounts of the carbs getting air leaks as a result of having said pump. The pump is supposed to give the saw better throttle response by offering a solution to the different "reaction times" of the fuel vs air when the throttle plate is opened. The general concensus seems to be it wouldn't need the pump if the L screw was allowed to be richened up. AFAIK, all MS200T carbs now have them, not just the US. A lot of other Stihl saws have them also e.g. MS361, MS362, MS441,...
-
I agree that the decomp system is over engineered but I'm pretty sure it doesn't send exhaust fumes back in to the crankcase Rather than an EPA scheme I thought it was a Husky idea gone bad. Pretty sure they stopped installing the auto decompression on later models because of all the problems and there is a tech note outlining the required parts to either turn it into manual decompression or plug the decomp. I suppose California and a few others might be different but I thought the majority of the US states were the same as us i.e. some model saws are available with catalytic converters but you can also get the same model saw without one. There are a lot of Stihl saws for example where catalytic mufflers are not even an option. Yes, I agree it is a good idea to run slightly richer than EU/EPA regulations permit/suggest. However, don't do it on a saw still under warranty.
-
OEM piston? Did you remove the limiter caps and screws to clean the carb? According to my literature the standard setting (limiter caps in place) is 3/4 turn out on the H. The basic setting (having removed the limiter cap) is one full turn out on the H. (For the HT-12D and HT-12E carbs). The newer Walbro carb is different.
-
I don't think you would notice any difference in power. It is just that you may need the higher octane in a race saw due to the higher compression of the engine, to prevent detonation. You can advance timing by either removing or shaving off some of the woodruff key. The key is only used to ensure the flywheel is in the "right" place, it is the crankshaft taper that prevents the flywheel from spinning on the crank. ...or just buy a saw with points and condenser. Agree with your conclusion
-
Adding more oil to the fuel will in fact make the fuel to air ratio leaner but I doubt 5% would have resulted in this. IMO it sounds like the saw was set up to lean from the factory. Due to the nature of design of a chainsaw carb the air/fuel ratio will be leaner at part throttle than at either idle or full throttle. However, most carbs nowadays have a part-load jet which lessens this effect, don't know if the MS261 has. I don't believe there are any aftermarket piston and cylinders available for the MS261. Surley the German made saws we receive are governed directly by EU regulations as well as indirectly by EPA ones? By "two choke carbs" I presume you are referring to the twin barreled carbs found on the MS441 etc. This is due to them having engines with stratified scavenging, which in itself will not make a saw run leaner. At the start of the exhausting and scavenging cycle, fuel free air first streams from the transfer ports into the combustion chamber and scavenges the exhaust gas into the exhaust port. The head air prevents the subsequent fuel-air mixture from entering the exhaust port, thus reducing the environmental impact by reducing the fuel-laden scavenging losses and the fuel consumption. What is a "power valve"? Are you sure you don't mean all US saws have spark arresting screens instead of all US saws have catalytic converters?
-
Actually it is the opposite. The carbs with idle systems dependent on the main jet system are more common nowadays. Generally the independent ones are on older models or belong to older saws. I meant to say before the full-load semi-fixed jet is not an exclusive feature of the dependent carb, you can find it on independent ones also. I am not aware of an independent carb having the part-load jet though, maybe due to design or again due to age?
-
Out of interest did you take a peak at the intake side of the piston? Those wire mesh filters aren't the best! Especially if it is old, the mesh can warp and the spacing between the wires is greater in certain places than it should be. It usually doesn't hurt compression unless it is really bad but it will eat the piston skirt. A felt filter is available instead. Unlike when the saw would have been released, Stihl now only recommends wire mesh filters to be used in extreme winter conditions i.e. falling snow. Good diagnosis work though
-
Idle system dependent on main jet system In these carburetors the idle system branches off the full-load system after the high speed screw. It is not directly connected to the metering diaphragm chamber. Full-load fuel flow is determined by the high speed screw (H). Adjusting the low speed screw (L) to change the idle fuel volume does not result in a change to the overall fuel volume.
-
As I said in the MS201T thread, on some carbs the low speed screw will influence the full-load fuel volume. Idle system independent of main jet system In these carburetors the main jet and idle systems are arranged in parallel (separate fuel passages for H and L screws). Changes in the idle fuel volume mean a change in the full-load fuel volume. If the idle fuel volume is altered with the low speed screw (L), it is necessary to readjust the high speed screw (H). When the idle setting is made leaner, the overall fuel-air mixture becomes leaner too. This increases engine speed as well as the risk of engine damage as a result of overheating. Note: different model carbs for the same model saw can vary with respect to having dependent or independent idle systems. E.g. the Zama C3M carbs for the Stihl 044 have independent idle systems, however, the Walbro HD carbs for the 044 have dependent idle systems.
-
You can lean a saw out at full throttle as well as at idle by only turning the L screw "in" on some carbs. It depends if the idle system is dependent or independent of the main jet system...
-
Any of the old Mccullochs, Stihl 070/090,075/076, Sachs Dolmar 166, Solo Twin 611
-
Bad unfortunately. It seems to be pretty random whether anyone has the right crankcase to install the side chain tensioner or not. The MS240 and 024 parts lists aren't much help and there doesn't seem to be any tech notes from Stihl regarding this. Some pictures. The first three show a 024 which could be turned into side adjustable. The final picture is of an MS240 crankcase where this is not possible.
-
I use caustic soda (sold as drain/heavy duty cleaner), available in most supermarkets/hardware stores etc. As I understand it is virtually pure Sodium Hydroxide (NaOH) and comes in solid flakes/pellets. Mix with water yourself when needed. I haven't got an exact ratio but usually try to dissolve as much as possible in a couple teaspoons of water. I apply with a small synthetic brush (The end of Q-tips seem to dissolve). Heat definitely helps. I can't compare how good the Caustic Soda is compared to acid as I have never used it. Disclaimer: I am in no way recommending that anyone try this. Just outlining what I use fully understanding the risks involved.
-
It depends. I believe the crankcase may have been changed at some point to allow the accomodation of the side chain tensioner whilst still having the front chain tensioner installed at the factory. Does your saw have the stainless steel inner guide plate, like the MS440 etc? (what the bar gets clamped against)
-
Splitting the case on a Husky 61. Remove all screws and dowel pins. Clutch side using homemade puller/pusher. Secure using bar nuts and any neccessary spacers on the bar studs. Flywheel side. Push out crank using homemade jig and big clamp. Use block of wood with countersunk hole to protect crank from "mushrooming". If a bearing is left in the case I use a vice and a socket of size such that it contacts the outer race of the bearing. If a bearing is left on the crank I use one of those el cheapo bearing pullers. Job takes less than the time it takes to post this.
-
Vac and pressure testing a Stihl 024. Clamp a piece of rubber between the cylinder and muffler. I used one of the various aluminium flanges I have on the intake to clamp another piece of rubber, with 3/8" drive sockets as spacers. You can use the carb as a spacer but for this model you would have to take off the pump side of the carb to enable you to gain access to the impulse tube through which I apply the pressure/vacuum. Vaccum test first. This test is important because oil seals tend to fail when subjected to a vacuum. Which means the oil seal lips lift away from the crankshaft during the pistons induction stroke when there is no internal counterpressure. It is possible a pressure test alone could not detect this. Apply approx 15 inHG vacuum. I leave for a couple of minutes then return and rotate the crank slowly several times. Shouldn't loose any vacuum. However, the Stihl literature is a lot more relaxed with limits calling for only 20 seconds to be required for the test and then conclude the crankcase is airtight. Pressure test. Apply approx 7 psi again leave for a couple minutes etc The saw past both tests.
-
Using my patented cocktail of chemicals and wet and dry paper to clean the bore and combustion chamber. No visible/feelable scores above the exhaust port so it should yield good compression.