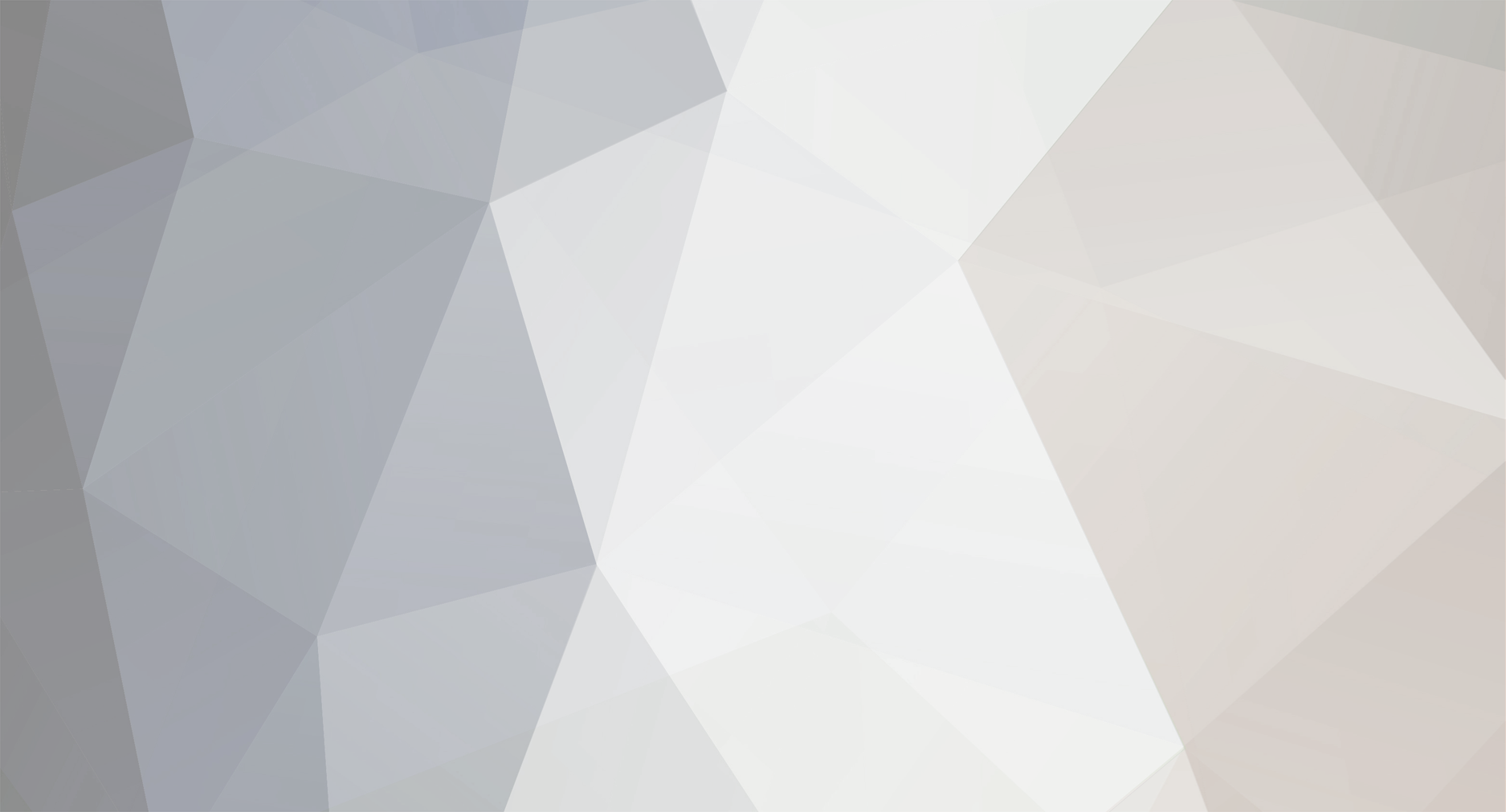
farmerjohn
Member-
Posts
273 -
Joined
-
Last visited
-
Days Won
1
Content Type
Profiles
Forums
Classifieds
Tip Site Directory
Blogs
Articles
News
Arborist Reviews
Arbtalk Knot Guide
Gallery
Store
Freelancers directory
Everything posted by farmerjohn
-
what will cut a lot will cut a little!!!
farmerjohn replied to farmerjohn's topic in Panther Mill UK
Man do I see what you mean about bar sag, I never experienced it with my 50 inch Cannon bar. There seemed almost 1/4 inch deflection without the power heads on and set at maximum cut. To reduce the sag we pushed the 2 sides in 5.5" each side and it reduced it drastically. Is there any issues with running the mill like this. Apart from if we get a bigger log we need to move the brackets back out. -
I have just received my new Granburg Mill and it has arrived with a Hypre skip chain. I am going to make up 2 other chains up from my older chains Oregon 27R's, leave one standard and the other i was thinking of cutting some of the teeth and leader off (maybe cut 3 or 4 off between) has anyone else done this? i have been advised if i am carful and use a thin blade and dont let the metal of the chain get hot it should be ok. spoke to Rob D at APF when i was running 2x 075's on a 4ft mill and he didnt think i need to mess about with the amount of power i had. new set up is a ms880 and a ms650 on a 5ft cut. any comment welcome. ]
-
He must have worked with 2 legends i served my time with on building sites. they used to say to me. "just remember, p@ss while you walks and sh@t in your own time!!!" I now tell all my employees the same (half in jest!!!!! )
-
said like a true Yorkshire Man!!!!!
-
what will cut a lot will cut a little!!!
farmerjohn replied to farmerjohn's topic in Panther Mill UK
Hi Jonathan, thanks for the reply. how are things now you are back down south ? the other problem with the swerber is that my ms650 would not go on it without removing the chain break handle (not enough clearance between saw and upright on the mill) ill speak to Rob as i think some of the mills are adjustable to put a smaller bar on. I can not really justify having 2 seprate mills and 4 saws to run them -
Hi All, I have had a old swerber double headed mill with 2x 075's, few reliability issues maxed out in oak, but it has been an awesome start to milling. i had the opportunity to get my hands on a few logs that are 5ft across at the bottom end with bad access for machines to move the logs as a whole. sooo, i have decided to buy a double headed mill and a ms880 (i will run my ms650 on the other end) and the other will be sold. I have bought a 87" bar to give a 72" cut. MOST of the stuff i will mill with the chainsaw mill will be around 40 to 50" (though who knows whats around the corner, 2 months ago 50" cut was ample) what are the pros and cons of cutting logs considerably smaller that the mill size. (anything up to 35" ish i cut on a woodmizer) has anybody ever bothered buying a smaller bar and chain for a larger mill or is it not really worth it for the 20" ish differance? thank all
-
Awesome, Cheers mate
-
Hi All, i have some unreliable older saws on a double head mill, 075 and 051, i am wanting to get an ms880 to replace the 051, and in the future replace the 075 as funds allow, with the 075 and the ms880 having different high end RPM i thought id best ask if anyone has run 2 saws with similar deference between them. Thanks, John
-
Hi Dumper, i have searched for spud, but it says he last visited in 2012, does anybody have any contact details for him? Regards, John
-
thats his nickname on here?
-
vibration problems ??? i need a pouch to catch the bolts that drop out each cut we make, thats with new AV mounts and EVERY bolt lock tighted in. the mill is a sperber that on the advice of another arbtalker i removed the rollers off the top and had some aluminum box welded to it. am deffo going to look into getting a ms880 in a few months. has anybody ever run a newer saw with an older saw on a double head mill? thinking of slowley upgrading to 2 ms880's and a mill with a bigger cut over time. but i am concerned about the top end RPM differance
-
out of interest does anybody know of a company / 1 man band REALLY good with older 2 stroke engines? i have this and 2 sthil saws that are beyond us. Regards, John
-
funny you should ask, it came with 2x 075's, one ran great, the other struggled to start, ran like crap etc, anyway, we put new barrel and piston on, carb kit, filter, crank seal bearings, etc etc. it ran fine for a few days and started playing up again. an 051 in good condition came up and i bought that, so at the moment we have 1 051 and 1 075 on it. and a 075 that we cant fix.
-
we, i ended up getting them and milling them for the craic!!!!! and to get some practice on the chainsaw mill. as everyone suggested the timber is a bit on the soft side, but thinking a fat bit of resin on it will harden them up for a table for my misses and parent at least even if it does not seem good enough to sell to customers!!!!
-
Advice from Trak Met bandsaw users please...
farmerjohn replied to Tom at Heartwood's topic in Milling Forum
That makes 3 of us!!!! I have been cutting with my chainsaw mill with old 075's and we practically do a day milling and a day re-building / fixing saws. i am very seriously looking at a 1200mm wide hydraulic mill thinking around march april 2019 if all goes to plan. the main of what i will cut will be wither the odd oversized 3-4ft oak logs around 3" thick or 2 to 3 ft hardwood planked around 1.25 to 2" thick. I am thinking due to budget of a 600 model rather than a 800, does anyone run a 600 with wide head? also BigJ, out of interest, your 800, did it have 1 log roller or a number? u mention in a post you were milling pretty huge loge 4T+ im just wondering if 1 log roller, did it manage to roll the log? also, hoe did you go on with import tax etc? did trekmet sort all that out so you just had a bottom line figure you knew it would cost? if anyone else seriously thinking along the trekmet route early to mid spring next year PM me. -
my god how true that is!!!! i have spent more time tinkering with the old 075's that came with my old mill than milling, the amount of times iv said ''could do with an engineer to make a mill that will use chainsaw bar and chain and wither electric motor or hydraulic drive but give a 50"cut'' this is that my double head mill will do and i am getting logs that nearly max it out, anyone know of an fabricator up for a challenge like that, or do i just battle on and save up and get a manual trekmet with a 42" cut for about £9k plus delivery and import tax, or just get a paid of 880's with little use to hopefully be more reliable!!! PS, awesome looking mill BigJ
-
Hi all, just a question pretty much as per title. when making skirting and architraves i buy quite a bit of re-processed tulip wood (poplar) for planing and molding. I am fairly certain it is completely different to uk poplar but can not remember why i know this (prob read it on here) can anyone confirm this? Its just my friend has quite a few really straight trees about 24" diameter so handy size for manual mizer. Regards, John
-
Hi, does anyone know of anywhere in the UK does carb kits for sensible money its for a Tillotson Hs-60d Carb. i can only find them for around £50 each in uk, i need 3, and they are about £18 quid each and £18 postage for all 3 from america. Thanks, John
-
hi Bill i was happy with how they went in and we did grease them, though i did not use stihl baring seals, bough good quality ones from a baring supplier. the bearing themselves seemed absolutely fine, and we did grease them. coming to think of it, the wrong seals were sent by sthil which is why used non sthil and i have feeling we only did that side seal in the 1 saw that is now stiff. Think next step is to remove that seal and see if it removes the knotch when turning by hand
-
keep the fluids going and dont take up accountancy, wisest words of the year, will take them to my grave ?
-
BIT OF AN UPDATE / ADVICE Hi, I have put this post in the 'chainsaws' forum but as its directly related to this thread, and some people might have had simlar issues from old milling saws i thought id double up the post. ill try and make this brief as i can. I bought a mill with 2x 075's (one on each end) one was running fine, one a bit rough. after changing a lot of parts on both the one running rough was running perfect, the one that was running rough is now spot on. the one that was running really well now seems to have a tight spot, after changing crank baring seals it seemed tight to pull (as if there was a hand break on !!!!) this is what we did on the saw: before i bought a clutch spanner i tried the old method to lock the crank of putting rope down the plug hole and turned to top dead center and got a bar on, there seemed to be a 10th of turn then went tight again so i stopped as it felt bad and got a clutch spanner ordered, changed the seal, put all back together and it was tight. after deliberation decided to remove the barrel and there seemed to be fibers between the barrel wall and piston, so presumed the rope had gone into the exhaust port and i had cut it with the piston, on inspection the chrome was flaking on the top of the barrel. so decided to change the barrel and piston (as we had changed this with great success on the saw that was running badly as barrel badly scored) so, new barrel and piston in, oiled everything up, new gaskets, stretch bolts etc, went to fire and its still tight, took the spark plug out as even with de-compressor there is some compression and compared the other saw it seems to have a tight spot at top dead center as it changes direction, like a notch!!!! my thoughts are, but i cant believe i could have done it so easily is that i have bent the crank or con rod. am going to split the saw (again) at the weekend i think, does anyone have and other thoughts? or even if i get the crank off, how to check it or the conrod as the been could be undetectable to the human eye. Any advice would be much appreciated as i just want to get milling and spent so much time and money and still am not up and running its frustrating
-
i have access to a woodmizer for smaller stuff, only milling 750 -1200mm diameter with the mill. am having rollers changed and a mill fitted as i type. just need my saws working!!!!
-
Hi, ill try and make this brief as i can. I bought a mill with 2x 075's (one on each end) one was running fine, one a bit rough. after changing a lot of parts on both the one running rough was running perfect, the one that was running rough is now spot on. the one that was running really well now seems to have a tight spot, after changing crank baring seals it seemed tight to pull (as if there was a hand break on !!!!) this is what we did on the saw: before i bought a clutch spanner i tried the old method to lock the crank of putting rope down the plug hole and turned to top dead center and got a bar on, there seemed to be a 10th of turn then went tight again so i stopped as it felt bad and got a clutch spanner ordered, changed the seal, put all back together and it was tight. after deliberation decided to remove the barrel and there seemed to be fibers between the barrel wall and piston, so presumed the rope had gone into the exhaust port and i had cut it with the piston, on inspection the chrome was flaking on the top of the barrel. so decided to change the barrel and piston (as we had changed this with great success on the saw that was running badly as barrel badly scored) so, new barrel and piston in, oiled everything up, new gaskets, stretch bolts etc, went to fire and its still tight, took the spark plug out as even with de-compressor there is some compression and compared the other saw it seems to have a tight spot at top dead center as it changes direction, like a notch!!!! my thoughts are, but i cant believe i could have done it so easily is that i have bent the crank or con rod. am going to split the saw (again) at the weekend i think, does anyone have and other thoughts? or even if i get the crank off, how to check it or the conrod as the been could be undetectable to the human eye. Any advice would be much appreciated as i just want to get milling and spent so much time and money and still am not up and running its frustrating
-
bit off topic but i love talking about urine, i was so dehydrated today mine was orange!!!!!