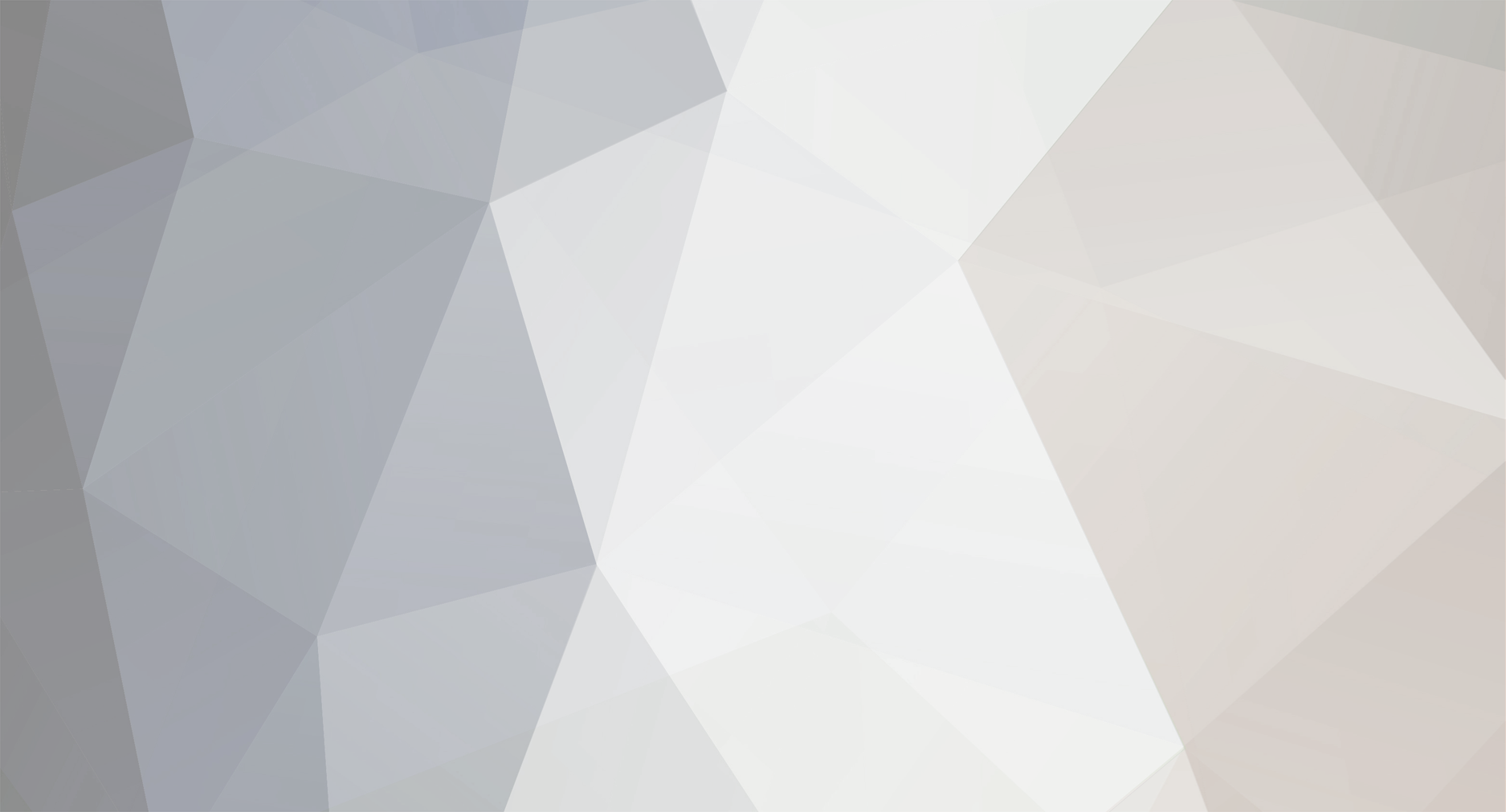
ESS
Member-
Posts
393 -
Joined
-
Last visited
Content Type
Profiles
Forums
Classifieds
Tip Site Directory
Blogs
Articles
News
Arborist Reviews
Arbtalk Knot Guide
Gallery
Store
Freelancers directory
Everything posted by ESS
-
extracting 150 cube plus hardwoods
ESS replied to steve collins's topic in Forestry and Woodland management
It helps , but with wheeled machines not as much as you would hope.I had a small one built years ago for skidding large conifer to keep them cleaner, I only had a smallish skidder at the time. The front end still lifted at times, and because I was dragging an extra set of wheels through mud it made things heavier going . Tbh I was a bit disappointed with it. Behind cats, which they were really designed for they were a great idea. Have you got your front wheels ballasted, that makes a big difference? -
extracting 150 cube plus hardwoods
ESS replied to steve collins's topic in Forestry and Woodland management
For sure. Tbh a lot of lorry cranes would struggle to lift butt end of a 150 lump, its a big ask of a crane on the back of a machine. -
extracting 150 cube plus hardwoods
ESS replied to steve collins's topic in Forestry and Woodland management
Sorry , no what I was trying to say was the machine will pull 150 comfortably as a skidder, but I couldn't comment on how efficient the crane would be with that weight.There were only trees up to 70 on this site. Lifting 150 tip first on longer trees would probably be ok, but butt first not so sure. I know exactly where you are coming from with the 2 machine operation,we used to fell a lot of Oak,and looked at all the options, in the end we just used a skidder and subbied the crown wood forwarding out, it worked for us and we weren't paying finance on a crane trailer or forwarder that was stood watching us whilst we felled/extracted butts. If I was to go down that route again I would probably use grapple/cable skidder and still subby the forwarding out. £6- 8 /t gets a lot of forwarding done. To buy a forwarder that you could afford to sit for these sites would be buying someone elses scrap and it just wouldn't stack up financially. -
extracting 150 cube plus hardwoods
ESS replied to steve collins's topic in Forestry and Woodland management
Its easy to forget how far back they went,particularly when they are still used. Always liked the shape of the 1164, and they sounded sweet. They always seem to find a home when they come up for sale, whatever condition. Some seem to find their way to the vintage sales at Cambridge. Thanks for that, brings back memories. -
extracting 150 cube plus hardwoods
ESS replied to steve collins's topic in Forestry and Woodland management
What models ? -
extracting 150 cube plus hardwoods
ESS replied to steve collins's topic in Forestry and Woodland management
Oh ok, well Counties have become collectable now . They stood us well down the years, You still have your kit? -
Low impact forestry services in Devon and the South West
ESS replied to Big J's topic in General chat
The Elm I mentioned was 81qg , 1762 hoppus of measureable timber, things like that you don't forget. I have literally cut timber from the north of Scotland to Cornwall to 5 years on windblow in the south east and Wiltshire, Hampshire, Dorset . Barrelled 9m + spruce off the hillsides in Scotland, tbh I just smile at what people call cream nowadays. -
extracting 150 cube plus hardwoods
ESS replied to steve collins's topic in Forestry and Woodland management
I had an 1124 for a number of years, pull like a train. We actually field tested the first boughton double drum, hell of a winch. Took it off that and fit it to a 1454 that got stolen. Last county I had was 1184 with 8000 mounted remote, she could pull. We got a 300 + lump of chestnut out with it. Tbh purpose built skidders are more affordable now aren't they ? -
Low impact forestry services in Devon and the South West
ESS replied to Big J's topic in General chat
I am just a thick woodcutter and wouldn't have the ability to upload pics. I have been involved in hardwoods most of my career and do have pics of stuff we have cut that a lot could only dream of. Elm to over 1700 hoppus, Spanish to over 600 hoppus, Beech to over 800 hoppus , Oak 400 plus. Conifer, Spruce over 300 hoppus, Douglas 2-300 hoppus, Larch to 200, and you ? -
Low impact forestry services in Devon and the South West
ESS replied to Big J's topic in General chat
That was the only way I could imagine. Painfully slow though. -
extracting 150 cube plus hardwoods
ESS replied to steve collins's topic in Forestry and Woodland management
That particular machine would be skidding 150 + but not in one lump. A county with mounted igland 8000s would, then crane trailer to go on butt plate.I have run several, and they will handle 150 comfortably. Finding one would be a different matter. We ran cat 955 with fork on , had a big crane trailer built for that that would carry 300 cube., with 4 sets of bolsters on. Hyster winch on cat. The HSM was sold to Essex and replaced with new. They would let you have a look at it. That one had a head to go with it too. Grapple skidder with trailer was a shit suggestion, grapple would snag headboard etc. -
extracting 150 cube plus hardwoods
ESS replied to steve collins's topic in Forestry and Woodland management
I have worked alongside HSM , crane with d/d winches rated @around 17t from memory. Very capable machine on the winches and crane, 150 might be a bit savage to skid with crane alone, although they do have a grip on the butt plate, pricey though. When you say tops do you mean in shortwood ? I would have thought it simple enough to plumb a trailer to a grapple skidder. -
Low impact forestry services in Devon and the South West
ESS replied to Big J's topic in General chat
Perhaps its me that's not understanding it, however, ….the machine travelling up the rack is driving at the felled trees end on in a line thin,..but processes 90 degrees to that line .the head works across the bed ? In a stand that has already been line thinned before the matrix wouldn't be a problem as you say because the trees can be winched to the side of the machine, but to process trees that are felled in the line the machine it would seem would have to be sideways on to the butts, in which case you would be processing down the line. -
Low impact forestry services in Devon and the South West
ESS replied to Big J's topic in General chat
Sorry, but you are not understanding me,you would still have to have the butt end of the tree at 90 degrees ish to the machine to process them. How can you achieve that ?In a single rack thinnings the felled tree is going to land with the butt roughly in the centre. I don't see how you can then process that tree off the side of the rack with that machine, to do that the tree needs to be turned within the rack. If you imagine a harvester in a thinnings rack the trees are felled into the matrix, then processed across the bed, so no turning of trees, whereas in handcut line thinnings the trees are cut down the rack so the need to turn them ? -
Low impact forestry services in Devon and the South West
ESS replied to Big J's topic in General chat
Hmmm, not sure you understand where I am coming from,...if you look at the video the trees are presented to the processing head at 90 degrees, ish . In a felled rack the trees will be facing the machine head on either tip first or butt first, it doesn't appear to have the reach to pick trees up in front of itself , and even if it did you would be processing straight back at the operator short of turning the trees before processing. -
Low impact forestry services in Devon and the South West
ESS replied to Big J's topic in General chat
Yes, but surely you have to process across the bed, in which case the trees will be to turn.How do you turn say a 25 foot tree in a single rack to align it with the head ? -
Low impact forestry services in Devon and the South West
ESS replied to Big J's topic in General chat
Would it not be difficult to turn trees in racks to process them, particularly where they need to be felled head on ? -
Low impact forestry services in Devon and the South West
ESS replied to Big J's topic in General chat
How much are they out of interest ? Value could be added to produce with the ability of cutting stakes which are in constant short supply, but are an absolute ballache to handcut .Winched timber off a bank is a nightmare for conversion, unless mechanised. You tube Jarc crac dual. -
Low impact forestry services in Devon and the South West
ESS replied to Big J's topic in General chat
Yes, well it may be there a while then, unless they can tag it in with something else close by. I could see a tractor mounted processor fitting into your operation to cut cost down for winch work ? Knocking trees over is relatively cheap, its the conversion that costs money, particularly alongside winching. -
Low impact forestry services in Devon and the South West
ESS replied to Big J's topic in General chat
Will do, thanks. It should happen in the course of this summer. -
Low impact forestry services in Devon and the South West
ESS replied to Big J's topic in General chat
I couldn't comment about that site without seeing it,but I could understand with handcut it would be a problem, unless conversion was through a processor after winching if that's what it needed, obviously winching is double extraction costs. In general terms in mainstream harvesting it sounds an attractive rate , and certainly if it was a site we could work with the T winch I would have a stab at it, or if we could harvest it with an 8 legger , 60 t a day average would be making money. £28/t is skyline rate. You are right in general that they don't offer enough money, but its easy to see why. Harvesting managers don't work for contractors, they have directors and landowners to answer to. As far as a landowner is concerned you can only sell it once , so sell it right. If you are able to keep busy with sites away from mainstream then that's all good, obviously one of the problems you have is terrain in your area, and the limitations of not having purpose built machines for working these sites adds cost. In most areas timber has been grown on land that is worth bugger all for anything else, particularly conifer, and by its very nature is difficult to access. -
Low impact forestry services in Devon and the South West
ESS replied to Big J's topic in General chat
Hmm, day rates mixed in with piece has never been ideal. I worked Sussex and Kent for many years and tbh apart from hardwood pulp, rates in the South East were generally higher than what we were used to.In more recent years I have only felled /extracted large hardwood in that area and found the rates good enough for us to do well, travel from the north and lodge. As I said in an earlier post , there is a massive fight between marketing companies to buy timber and feed supply chain quotas, sadly that has had a knock on affect on harvesting rates, particularly in main stream work. I have sites to look at in Kent in the not too distant future and will be needing cutters for some of the work. -
Low impact forestry services in Devon and the South West
ESS replied to Big J's topic in General chat
I actually derailed the thread as its called because I read something at some point that the o p had written about paying excellent cutting rates. Personally I feel that if someone puts that out there it has the right to be challenged.? -
Low impact forestry services in Devon and the South West
ESS replied to Big J's topic in General chat
To a degree that's forestry today isn't it ? Its a slightly different situation in the south with terrain. I am from the north and can honestly say that a lot of the big hardwood skidding caused more than just surface damage. The company I first started with used D4s because nothing other than tracked machines could travel the ground and a lot of trees were 200 hoppus plus. Forestry and mess have always gone together. I will say though that I have worked on Sussex sites after the blow in 87 and there are still ruts in the heavy clay from 87 filled with water, but there again contractors were only doing what they were asked to do. -
Low impact forestry services in Devon and the South West
ESS replied to Big J's topic in General chat
I think I could say the same in over 40 years, but by the same token I would be shit at climbing. It is a different skill step, and I take nothing away from climbers by saying that.