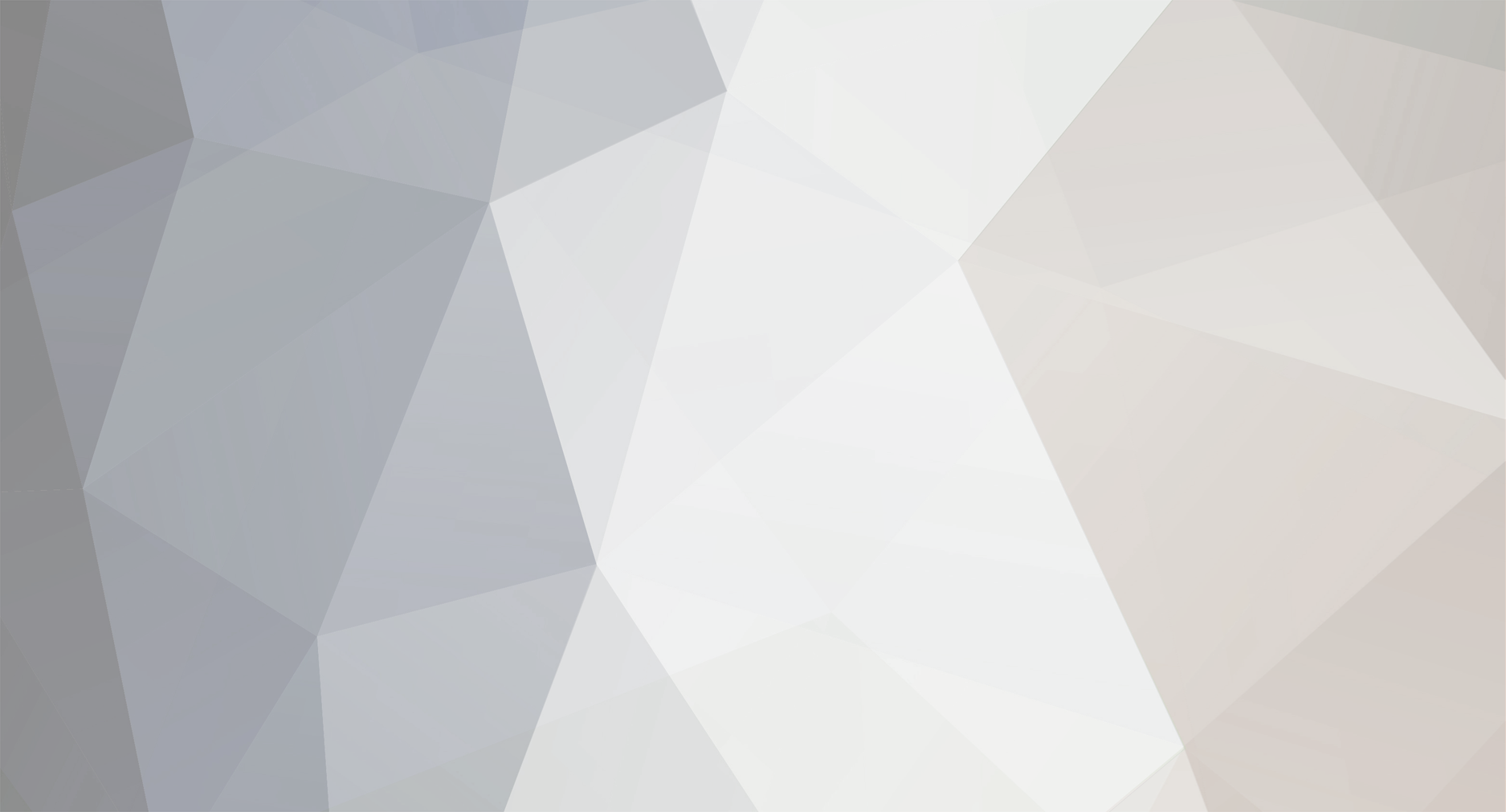
adamelder
Member-
Posts
106 -
Joined
-
Last visited
Content Type
Profiles
Forums
Classifieds
Tip Site Directory
Blogs
Articles
News
Arborist Reviews
Arbtalk Knot Guide
Gallery
Store
Freelancers directory
Everything posted by adamelder
-
I must have used pretty much every chain going over the last 5 years of milling. The lo pro Stihl PMX is by far the best I've come across. It cuts incredibly fast with not much effort and gives a very smooth finish. The ripping version seems to clear the cut better and is easier to push through but there's not a huge amount of difference between that and the crosscut version.
-
I live right in the middle of a small town. Occasionally I'll do a bit of milling in the back garden. I've never had a complaint but I have had neighbours drop by out of interest, to see what's being sawn up. Most of the town know me and find it amusing when they see me hauling 4m long slices across the high street or loading my milling set up into my old Merc convertible (who needs a pickup!?). I do most of my milling in a yard out in the sticks but a busy country walk runs right through the yard. Again, I've never had a complaint, only some walkers stopping to see what a tree looks like sliced. I've actually sold a few slices that way. How I approach it is to ask for a quick bit of help with lifting (if it's safe of course) if someone stops at the yard or drops by the garden. I find that inviting someone to get involved in some way goes a long way. Sure, that might have H&S implications if you're doing commercial work!
-
Cheers Spud, it's a fantastic saw. I don't really think there's anything wrong with it, more just getting to know it properly. Aye, it pulls fine without decomp, as long as you're not shy. Like you say it'll take your fingers off if you're not giving it the full blooded yank. Drop starting is my preferred method but it's tricky with the 50 inch bar on the mill! So I'll take the advice and just remember to pull hard !
-
I've got an MS661 about 9 months old from new. I'm finding that unless I give it a full blooded pull to start, it'll act like it's flooded - let sit for 20 mins or so and it's fine. Of course, it's easy to say, "Always give it a proper pull" but on the odd occasion I don't, the problem occurs. Any thoughts? Just take it back to the dealer on warranty?
-
My question is though, whats the best way to finish the cut? The final few inches i found the saw/frame would start to droop a bit. Any hints? I use a mongrel Logosol/Granberg mill but the same problem exists. In time I just got used to it and learned to support the mill by hand as it gets to the end of the cut, when the front rail becomes unsupported by the log. It's just a matter of taking your time and not being afraid of the chain a few inches from your left hand. As soon as the chain has finished the cut (but the back rail is still supported by the log) I flick the brake on, pull the bar clear and lift the mill onto the ground. I've seen a modification of the frame of the mill that some guys do. They screw a plate onto bottom of the rails of the frame that seems to be a reasonable fix.
-
That was the first tree I milled with the 42 inch GB bar and chain set up I bought from you a while back Rob. I was using the full (about 38 inches) length of the bar. The low pro chain made a huge difference to the milling speed. Thanks for that!
-
This is my latest project pretty much finished last night. The base was made by a blacksmith chum who speaks little English. I can't draw, don't measure with tapes or rules so explaining what I wanted was a laugh and a half. I ended up showing my friend my hen's feet to get the idea across. The top is a piece of spalted beech that I milled about 6-7 months ago. The tree had been lying for many years and when I milled the first slab it read about 20% moisture. I took a couple of the slabs into my spare room, stickered and weighted down. The moisture went down to about 10% very quickly. A few small cracks appeared but only surface ones. One shake opened up in the middle but it didn't travel too far up the board and got tied with butterflies I used bronze filings and West Systems resin for gap filling and the finish is Blanchon hard wax oil.
-
I very much like the "honesty" of your bench. I like that the joints are obvious and strong. Can't see that falling to bits anytime soon. It's nice to see something that's clearly made with a fair bit of love for the material. The scripting is a great addition and I'm sure is what people who know little about woodwork will appreciate along with the celebration of the wood itself.
-
Thanks Rob. The castors came from Hafelle. They're sprung ball bearing ones. I had to router out a deeper socket than normal so that they would be properly recessed. They allow the chair to be moved easily when it's not being sat on but the spring action means the chair sits properly on the legs when a weight is on the chair.
-
-
Here's a bed (head) I made from a huge plank of Scots Pine that came from a tree I milled in exchange for two slices of the timber. It's 40ish inches wide x 1 3/4 thick. The shelves are elm. The plank was stickered and air dried for a year and a half under very heavy weights to keep it flat and then stored in my spare room for 6 months under more heavy weights. After a year or so of using it I did alterations in my house (smaller bedroom) so the bed head was too big and was repurposed as a long table for my cafe.
-
The short distance between the in and out are too small for any U bend I could find. So I just made my own. Quite proud to say that it's never leaked a drop!
-
Thank you! The plumbing was a bit of a challenge but def not a nightmare. It's just the same as doing a standard sink. I fitted the waste pipe into the sink (basically just a snug fit through the hole with some epoxy) leaving about 30mm wood at the top which I coated with epoxy too. The waste exit was left about 150mm long, roughly inline with the waste coming out through the wall and then just connected up as normal but without a traditional trap. You'll see in the picture. Drilling a 40mm hole through about 18 inches of hard elm took a bit of time though. I actually bought a cheap mains drill expecting it to burn out which it did very quickly. So I just used my normal Dewalt mains drill and took it easy. Used an auger. All the plumbing is hidden within a stud wall at the back. I just hope I never get a burst pipe in there.
-
I used Rustins Plastic Coating. Three good coats with a 0000 wire wool rub down between each. It's been about a year of pretty standard use and I've recoated once which only took a couple of hours. Not had any problems at all.
-
West Systems resin is bomb proof. Their tech support are very helpful.
-
West Systems two part resin is fantastic stuff for filling. Dead easy to use. It takes any sort of filler (metal, glass, dyes etc). Doesn't need a vacuum chamber to get rid of bubbles. The pics show a sink I carved about a year ago and have been using daily since. You can see the fissures here that are filled with the resin. I've been using the resin mixed with bronze powder a bit recently. It sands and polishes down to a pretty genuine solid metal finish. Can't recommend it enough.
-
Makita 7104L Chain Morticer - Chain Morticers - Drills & Morticers - Machinery | Axminster Tools & Machinery
-
I've just milled up an elm that had been lying for I don't know how long. A lot of it is spalted. Some of the timber isn't quite rotten but not completely sound either, just a wee bit soft in places. It's very nice so I'd like to keep it as intact as possible. Does anyone have any suggestions on if and how it can be stabilised? I know there are wet rot wood hardeners around but I think they're really for timber that's completely gone. I was thinking maybe West Systems might do something?
-
I milled a load of spalted beech recently and it didn't just grow the white mould, it had white mushrooms! They cleared up once the wind and warmer air got through the stack. I figure it must be still, damp air.
-
Thanks for the video. Great stuff, especially the steer on the importance of sawing exactly along the growth of the grain. As Rob D says, more videos would be really useful. It's quite tricky working in isolation and learning through your own mistakes!
-
Remote controlled (almost!) double ended chainsaw milling!
adamelder replied to Rob D's topic in Panther Mill UK
I like that! -
He could well have been talking about your fine wine rack! But if there's any hint of me getting a compliment I'll seize it!
-
Thanks Mike!
-
I'm not so great at joints. But I was chatting with a chum about woodwork and he asked why I didn't make a chair. I told him that the thought of it terrified me due to the number of joints needed. So he bet me I couldn't make one. The plan was to make a chair with as few joints as possible but then I had other thoughts... This was the result. Sycamore mostly with oak for the cross pieces on the back. It's surprisingly comfortable - I curved the shape of the back to sort of match my shape when I sit. It's also shockingly heavy so it's got 12 recessed spring ball type castors hidden in the feet. It skates across my floor fine and sits happily in place when sat on.
-
Yes, I wasn't sure how the saw would cope with the long bar either. It wasn't particularly slow. A bit slower than the 42" but not bad at all. Certainly, the saw didn't bog down at all. I suppose that because most of the work today was on the mill I'm losing about 5 inches of bar length. The last short bits were about 55 inch so these were done freehand. Again, the saw didn't seem to struggle at all. Highly impressed with how it performed. I'm afraid I've got a queue of guys up my neck of the woods waiting for elm so gotta keep this stuff!