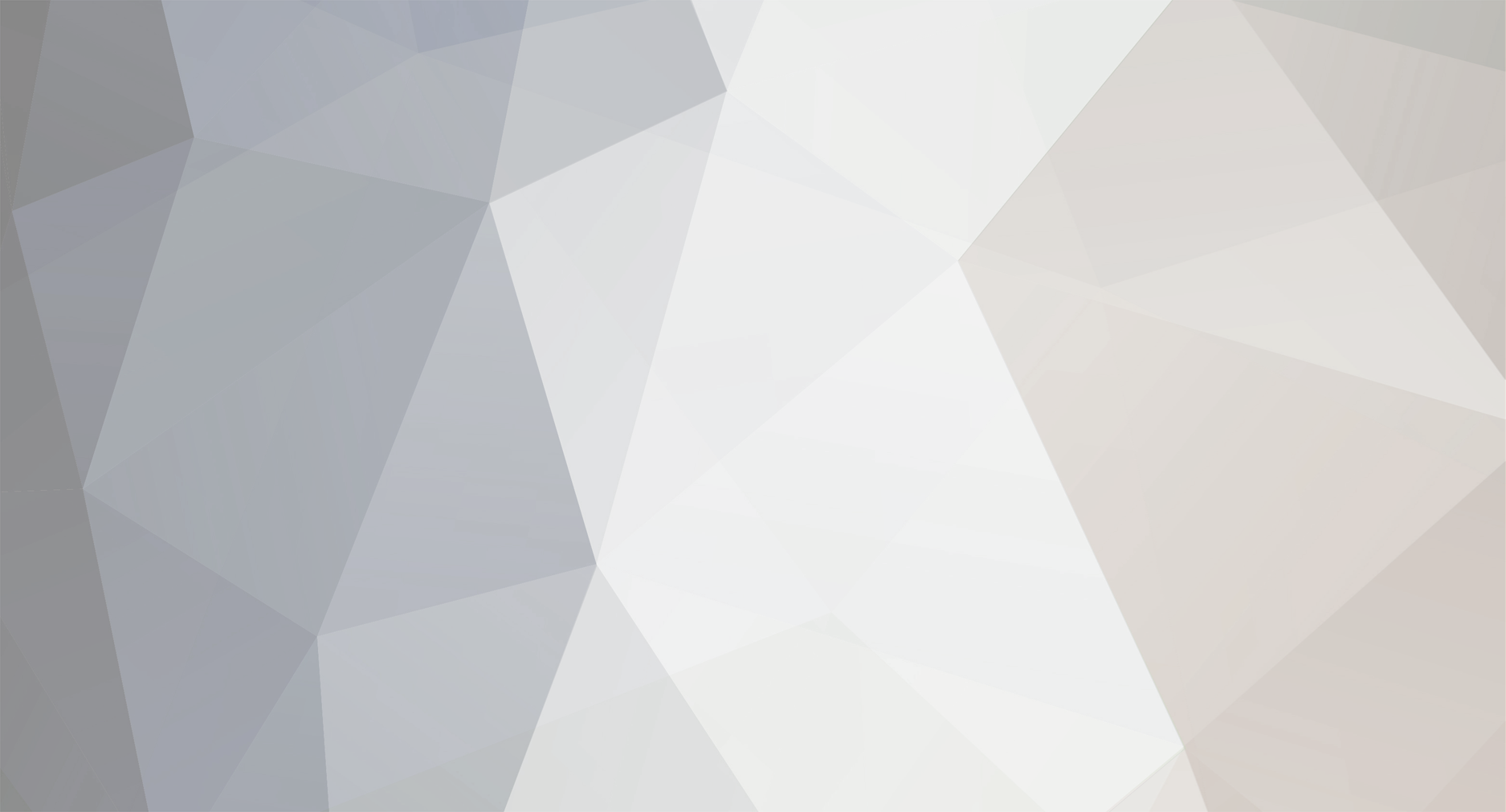
Pan
Member-
Posts
42 -
Joined
-
Last visited
Content Type
Profiles
Forums
Classifieds
Tip Site Directory
Blogs
Articles
News
Arborist Reviews
Arbtalk Knot Guide
Gallery
Store
Calendar
Freelancers directory
Everything posted by Pan
-
Hi Stefan Apologies my first response was based on your view on just making money
-
Well Stefan Based on what I thought of you - what a sad reply!
-
Hi Stefan Please don't take offence to what I am about to say Surely the art and craft of wood carving cannot be replicated by machine and computer. Where is the artistic ability and skill in becoming a computer programmer? Carving is a learned skill that requires practice and time to master. There are many great carvers on here that weald chainsaws to great results, or to the likes of me who get fed up using chainsaws all day so use traditional chisels instead. Computers and 3d CNC machines cannot and will not ever recreate the skill and artistic ability of the human hand and mind. When you see a mass produced computer orientated carving it de-values the true meaning of time honoured skill and craftsmanship - is this what progress and skill really means? I think these true values, should, and do reflect on the sort of person I thought you were (based on your postings). Are you more interested in mass produced/mass profit/ little skill, or the true meaning of human craftsmanship? Kind regards David
-
Listening to the news today it sounds like Nicola Sturgeon took the rugby defeat pretty badly!
-
Cheers for all the replies guys - nice to hear all your views. To answer some of your questions: They are all carved from seasoned wood. They took quite a while to carve, each one done over a weekend. Currently carving a Ginkgo design (but not finished yet)! Many thanks again Pan
-
Hello again Long time no contact! my apologies for always looking in but not contributing much - definitely time to change An Arb with a hobby of woodturning now changing to woodcarving (as the turning didn't seem to be selling or getting me anywhere). I didn't feel I could put these in the 'chainsaw carving forum' as they were made with chisels rather than chains. They are made from cherry wood mounted on a walnut plaque (7" x 7"). Any opinions or comments for improvement gratefully received. Kind regards Pan
-
Dan - Looks like you've had a busy weekend and off to a great start with the new lathe, addictive isn't it! Hope you have managed to sort out problem with the woodworm screw - as Steve has said taking lighter cuts with very sharp tools will help. What sharpening system are you using? TWiG - Another great selection of your work. The spalted ash hollow form being my favourite. I would imagine its quite hard to get such a good finish on spalted ash without the wood picking out. I have not got into colouring any of my work yet - how do you find the coloured pieces sell compared to the natural wood items?
-
Thanks for posting that article Peat its given me lots to think about in pricing my own work - seems like lots of sound advice I love the cruck framed bird table in your other thread. Can we see another photo with the shingles?
-
Hi Dan Thanks for the positive comment. I look forward to seeing your work on here shortly. Have you got your new DVR-XP set up yet?
-
Hi all - here is the second Maple burr that I turned. I have left this one a little thicker than the last as it was a bigger burr. I quite like a bit of weight to the form rather than it being too wafer thin. This one measures approx. 14" x 8". I have sanded the inside again, as it had such a large void in the side and everybody I show it to keeps wanting to put their hand inside! Does anybody have any news of any burrs available yet? Regards Pan
-
How Much? Now there is a good question and one that I've been pondering on myself, perhaps you guys on here can help me out. I've recently been to a few local art/craft galleries with a view to selling my work. It seems the going rate for commission around here is 50/50 or if your lucky 60/40 (This is in the South East). So you have the price of your wood - in this case nothing (my own arb waste) but sometimes I do buy in wood, so a burr this size perhaps £15 -£20. Time - Now I'm not a very fast turner as I only get time at weekends so I guess this piece took me a day to shape and hollow out. I then had to season it for 3/4 weeks as it was green wood. Then when dry sand it, including the inside which took forever (you wouldn't need to do this on a piece that didn't have such open voids). Then multiple coats of oil and wax over a few days - So the total time spent would be a minimum of 1.5 days. The gallery want their cut - I know it seems high but I don't have a shop front to sell stuff from. I could go to a local farmers market or sell online on a cheaper bases, but I don't think you get the same sort of people wanting to spend the same sort of money compared to a gallery. So what sort of price do you put on all of that? The older I get the less I want to be swinging around in the trees, and the more I think of diversifying into selling this sort of work. Probably just a pipe dream - I know!.........but I guess dreams have to start somewhere. What do you folks think?
-
:lol: I have a feeling our wives would get on like a house on fire! By the way I love the two little pots Terry. The bottom one is my favourite with a very suitable lid for your namesake!
-
Hi Stompy This one measures approx 7.5" tall x 9" wide. I was really pleased when I finished it but rather crestfallen when I showed it to the wife "Yes very nice dear but what on earth can you put in it"? Practical as ever! - love her to bits
-
Hi all - Well I finally finished the two Field Maple burr hollow forms that I mentioned a few weeks back, so I thought I would post the results of the first one. The two photos are the same form just front and back. Having turned these burrs, I would love to turn some more. So if anyone on this site is taking down any Field Maples with reasonable sized burrs on it please send me a message. In fact if anyone has any burrs from any trees I would still be interested in purchasing them! Many thanks for your interest Pan
-
Hi bobh The base of the bowl is the branch, with the head of the pollard at the top of the bowl. All the small branchlets come out the side of the bowl. I think I've got a photo of it before I started turning somewhere.
-
A few weeks ago I mentioned that I had made some natural edge bowls from some old willow pollards. I finished one today so hopefully some photos attached as promised. Amazing what results you can get out of a crappy bit of Willow! Size is 14" x 7" (I'm afraid the inside photo seems to have turned orange!)
-
Hi Terry, I've been turning for just over a year now doing all the usual bowls etc But having been inspired by the likes of you and Flames I have started doing more natural edge stuff and hollow forms. Choosing odd pieces of wood out of my own arb waste rather than the straight grained stuff I used to turn with. Had some old willow pollards that I did a few n/e bowls with but some of the wood, although highly figured, was very puckey so I left the foot on thinking I would get a better finish when it was drier. Problem is now they are so out of round I'm not sure I've left enough wood to recut them! Had a couple of field maple burrs that I've turned in your style with big gaping holes in the side. I did turn these in one go, as I got a better finish off the tools and they even sanded quite well being green without the paper clogging up. I have got them drying indoors at the moment and will leave them a few weeks before I pick off the odd bit of loose bark and then give them an oil finish. I noticed on some of your pieces you blacken the insides which I think enhances the outside well when you have a hole. On these bits of Maple the holes/gaps are so big that I'm not sure whether to blacken them or not. I'll try and put some pictures up when they are finished.
-
Hi Terry the HC burr form is absolutely stunning - I can see why you would want to keep that one! You often see that shape around but with a hidden join at the neck rather than one piece of wood. Can you tell me have you made that piece in one go or did you rough it out and then finish it at a later date when seasoned? Do you use the same process for all your hollow forms or would certain woods suit being turned to completion in one go as opposed to a second mounting. (I am imagining some of you hollow forms with lots of holes would be very difficult to remount after they had moved during seasoning)
-
Hi Steve Seeing all your cored out bowls I'm interested in how you are drying them. Are they just left in your workshop or are you bringing them inside for warmer conditions? How long are you leaving them to dry before you re-turn and finish them? Have you or anybody else got any ideas of speeding the drying process up with regards to turning green wood to finished article? You have got some lovely looking bowls there Steve I especially like the brown oak one.
-
Hi Andrew Great to see your wood store and how you currently season your timber - patience is certainly a virtue! Although fairly new to milling I am looking to try and speed up the seasoning process. At the moment I am looking into the Sauno woodkilns. Space is a consideration and the amount that I mill - so in that aspect it looks a good option but it does come with a hefty price tag! One of my current concerns with my timber is insect infestation (sycamore being worst affected). The kilning process with the Sauno does seem to sort this problem out with the initial high temperatures and use of steam. (Perhaps more so than the use of insecticides such as Boron?) I've got to ask - your curved sections of apple in your wood store look intriguing! What have you got planned for them?
-
Andrew Thanks for posting those photos, you must be so pleased with the result - stunning figure in those planks. I'm interested in your seasoning process now. Are you going to air dry for a couple of years and then slowly bring them into centrally heated house conditions? or are you planning on kiln drying them to get the moisture content down to suitable conditions? Also have you treated the planks with anything to stop any woodworm getting to the sapwood? Well worth all your effort so far - look forward to seeing what your going make of them!
-
Just to expand this idea further Rob - have you thought of sawing the initial butt into three pieces instead of in half? If you take the oak butt in your photo and you saw two vertical cuts say 6 -8" each side of the pith - this middle section could then be planked into 12 boards, turned again and ripped through the pith to give you 24 true quarter planks. You have then still got the remaining two halves to plank as you wish to give you your crown cuts or more quarter boards. Just an idea - what do you think?
-
I have recently purchased an Alaskan 48" to use in conjunction with a 2nd hand Logosol wood workers mill that I picked up a few years ago. I am fairly new to milling but hope this combination will work well together. I have been saving up various decent butts of trees that I have taken down this year and am looking forward to processing them this winter. I realise I will loose a lot in sawdust but I don't do enough yet to justify a bandsaw mill. I have sorted out a load of large Oak trees to take down this winter so I'm hoping the Alaskan will cut it nicely into quarters before mounting them on the wood workers mill.
-
Hi Alec Thanks for reply. Like you I think plain sawing and obtaining the wider boards will be better. I was just not that sure how stable walnut is. I am based near Maidstone Kent. I am thinking of planking it up in 1. 1/4" & 2. 1/4" thicknesses and hope to use it for making furniture and possibly turning some platters with the thicker sizes. I guess when I sticker and stack it all I should try and get one of those cordstrap machines to keep it all tight together. I believe you can also retighten these straps over time as the wood seasons and shrinks.
-
Hi guys I have just got hold of a fairly decent walnut butt 3m length x 50cm diameter showing a good 80% heartwood. Just wondering the best way to mill it. Quarter sawing - I guess would give me a radial linear figure (rather boring in this species) but with the advantage of greater stability. Plain sawing - would give me the tangential more showy figure. Having never milled walnut before I don't want to muck it up - what are your views? Are the stability advantages sought when quarter sawing as significant in walnut as opposed to less stable species?