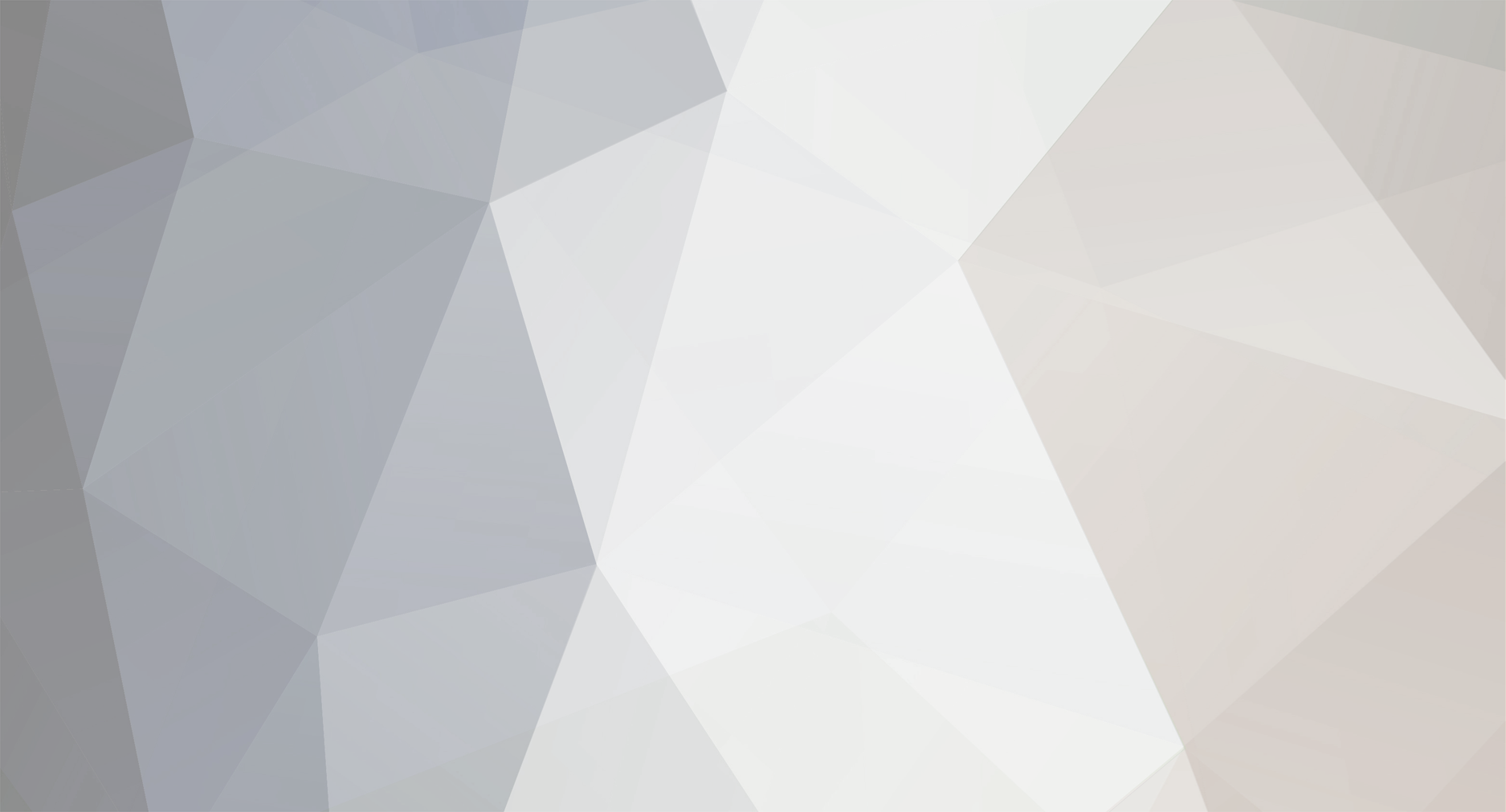
Exec Trustee
Member-
Posts
10 -
Joined
-
Last visited
Recent Profile Visitors
The recent visitors block is disabled and is not being shown to other users.
Exec Trustee's Achievements
Rookie (2/14)
Recent Badges
-
Hi NCSL, Sorry, What is 0021-05 ? Where are you based and do you have access to trees to be cut down ? Are you qualified to teach enabling award of a Lantra or NPTC certificate ?
-
Hi Stere & Handcutter, Nearly all of the 380mm courses only allow a class size of 4 and so these fill up pdq. I have been in touch recently with WBO only to discover that they cancelled their recently advertised 380mm+ course. I have tried Berkshire Agricultural College, Merrist Wood, Sparsholt and Hampshire Training Providers and am getting no place fast in securing a place and so if you can help then please contact me by PM or via The Oxfordshire Woodland Group website ([email protected]).
-
I was told by Hampshire Training Providers that Dave Grafton was working for them 2 days last week (Apr 2024) and is thus still very much engaged in the field of Chainsaw and Tree Felling training. I did my cross cut and maintainance (2012) & felling trees up to 200 mm (2016) under Dave via West Berkshire and Oxfordshire Training and was much impressed by his approach, knowledge and skills. Does anyone have a direct email or tel number to contact Dave to arrange a one to one on felling trees up to 380mm and over 380mm thereafter ?
-
We made our own European larch and Western red cedar shingles (more correctly called shakes) from 60 year old trees growing and felled in our woodland in South Oxfordshire to cover the roof of our cruck barn. We needed to make about 2500 shingles with a nominal 8" width x 24" long x 0.75" tapering to 0.375" thick. These were produced on a Woodland Mills mobile sawmill on a simple home made jig. All sapwood was removed and in practice a variety of shingle widths will be produced thereby ensuring economy of conversion. The shingles need to be "pick and mix" matched to ensure the correct positioning of the lap gaps between shingles. For further details please contact :- [email protected].
- 30 replies
-
- 11
-
-
Michelle Goss uses a Woodland Mills 126 and has experienced difficulties in re aligning the drive motor pulley to re tension her drive belt and align same to the drive wheel. Her videos are worth a look. Occasionally she has to deal with grizzly bears dropping by on their property in Western Canada which is not something that troubles us much here in Oxfordshire but we do have to deal with the dreaded glis
-
We felled our own trees and converted the main structural components (Larch & Douglas Fir) by hand hewing. After raising the timber-frame we used a temporary tarpaulin roof applied over the timber frame to make a relatively dry working space where we installed a Woodland Mills band saw to make roof shingles (WRC & EL), sarking boards (DF), floor planks (DF & WH), cladding (EL & DF), doors & shutters (WH). The building Inspector was not involved nor did we employ a timber grader. Each structural timber was assessed during conversion and where we weren't happy then a timber would be consigned to the bone yard or be subject to a localised repair.
-
It's been getting harder to push the saw through logs on the bed and I thought that maybe it was time for a blade change. Wrong ! Closer examination revealed that the front carriage wheel (on the blade exit side) had seized and so this wheel could only skid over the track. I jacked up the saw head carriage and unbolted the wheel. This confirmed my suspicion that the bearing was unable to rotate. I decided that I would need to buy a new bearing (part no 5204-2RS) and therefore the old bearing would need to be removed from the wheel rim. This is a interference fit bearing and so without a workshop in the woodland I inserted a 1" tapered hexagonal timber-frame peg into the inside diameter and then hit the end of the peg with a small hammer which did the trick in driving the the bearing out. Once out, I then used a carpenters scratch awl to prise up both bearing end covers seals and set about unfreezing the bearing with the aid of WD40. This is a double row ball bearing with 8 balls in each row held in position by a 2 part nitrile cage. The cages are easy to prise out without causing damage also using the scratch awl. The ball bearings all then need to be moved to one side of the bearing and then these can be dropped out one by one into a tray. The bearing components showed no signs of damage and so after a judicious clean it was possible to reassemble the bearing and then refit this to the carriage. Voila the carriage now moves very easily and the mill cuts a dream again. This bearing operates in fairly arduous environment getting sprayed with cooling water and sawdust from sawing and so maintaining this component on an annual basis would seem prudent. A new bearing can be purchased for about £12 from the "bearingboys" website.
-
Michelle Goss has just posted a video of her receiving, setting up and using the Woodland Mills setting and sharpening kit :- https://youtu.be/JkOFaaxAoVA
-
We own and operate at Woodland Mills HM130 and bought 20 blades with this machine direct from Woodland Mills. We are now out of WM blades and so tried 3 off Ripper 37 blades supplied by Stephen Cull. I talked with Stephen last week and he confirmed that he no longer sharpens blades instead sending these out to a saw doctor in Wales as recommended by Chris Pearce of Woodland Mills UK. I got in touch with Chris and he advises that his blades are sharpened at a cost of £7.50 each plus VAT & shipping at USK Saws located in USK, Wales ( email contact [email protected] ). Stephen Cull does not stock Daikin Flathers Ripper37 blades and instead he simply forwards orders received to Daikin Flathers who ship blades direct to Stephen's customers. It seems therefore that Stephen Cull is now little more than a post box for Daikin Flathers with his own immense competence and capability in the field of saw blades now of lesser importance. Daikin Flathers use UK / German steel to make their blades contrary to WM who obtain their blades from China and so since self sufficiency has become more important to the UK since the pandemic then maybe we need to support home grown suppliers On a more positive note if you can attend The Royal Welsh Show at the end of July or the APF in mid September then Stephen advises that you will be able to obtain 11 blades for the normal price of 10 however other of these 2 promotional events there appears to be little appetite for providing new customers with introductory or bulk buy promotional offers and so the purchase of a blade sharpening machine might now appear to become a more attractive option. However :- Josh at Woodland Mills advises that each blade can be sharpened 5 times and so with the blade sharpening machine costing £570 + VAT this would equate to a cost of £6.84 per blade sharpening for 20 blades. In our experience the reality is that approx 25% of blades get wrecked or become unsuitable for resharpening due to :- broken blade (root fissure cracking) teeth damaged due to sawing through the log support metal upstands (oops!) blade coming off drive and idler wheels, caught by blade catch which ruined a number of the teeth (mainly caused by pulling the saw backwards whilst the blade is still turning) the earliest blades are now rusty blade damaged by inclusions in the log blade buckled and therefore the stock of blades is bound to decline over Josh's 5 resharpening blade cycle effectively increasing unit resharpening cost. Now what to for the best and especially what to do with those junked blades ?
-
It is amazingly simple to make your own charred planks. Check out :- http://oxfordshirewoodlandgroup.co.uk/forum/?mingleforumaction=viewtopic&t=380 Professor Fugimori is the expert in this field of traditional Japanese wood treatment practice.