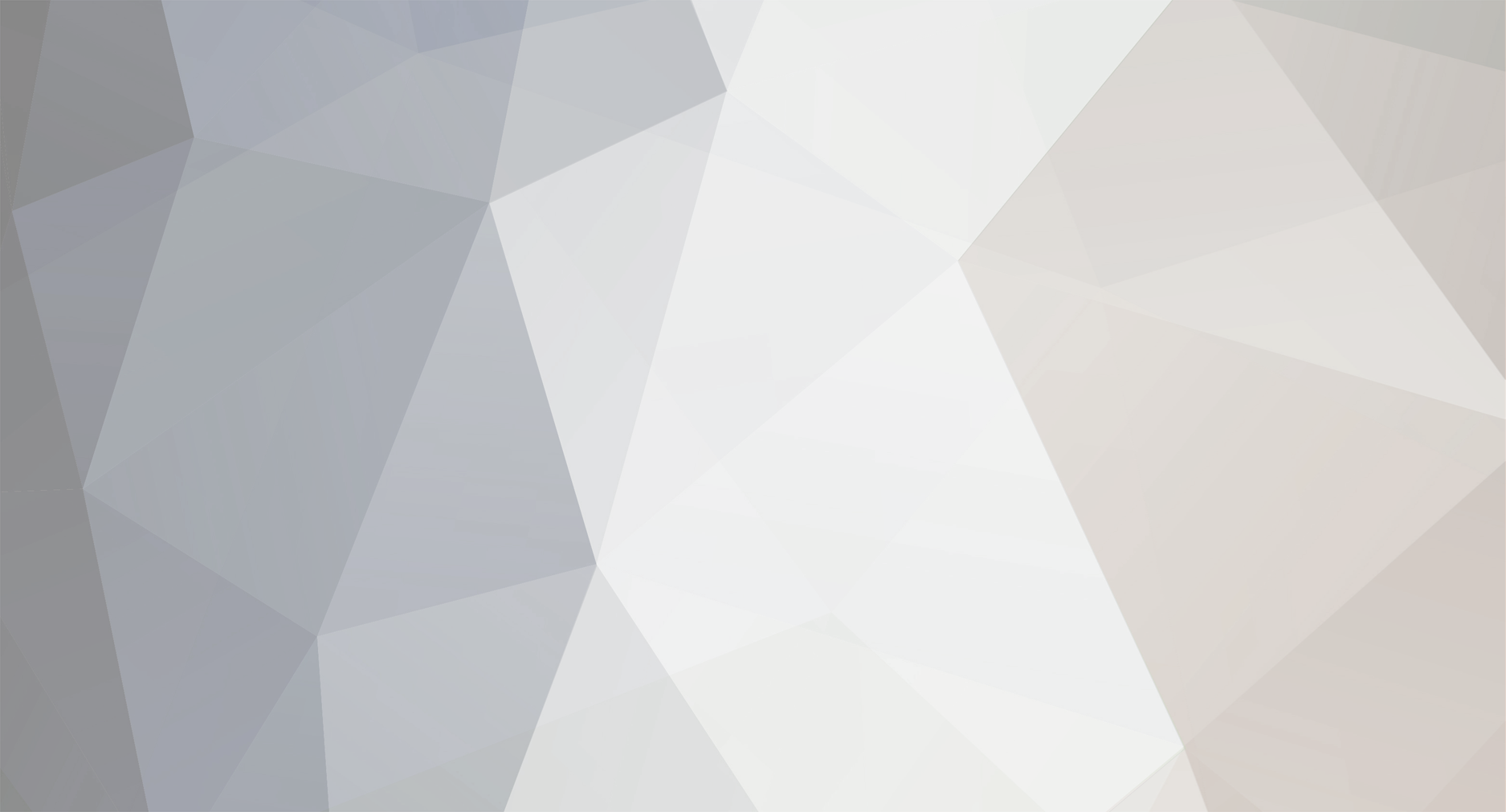
TonyIOM
Member-
Posts
119 -
Joined
-
Last visited
Content Type
Profiles
Forums
Classifieds
Tip Site Directory
Blogs
Articles
News
Arborist Reviews
Arbtalk Knot Guide
Gallery
Store
Freelancers directory
Everything posted by TonyIOM
-
Hi, I used use dry 1" (25.4mm) wide oak dowels, 3 in each leg. I hand drilled the holes using a 27mm forstner bit which gives you some tolerance but still allows a secure fixing. I made the centre one longer into the leg and tight, glued with epoxy. The outer 2 dowels have more play in their leg sockets to allow for seasonal movement, fixed with a strong flexible sealant. I figured the centre of the board won't move as much as the edges. I figured the magazine shelf adds significant rigidity to the structure so there is no other support used. I found a lot of articles mention the need to allow for woodmovement but few show how to do this in an elegant manner without resorting to figure of eight or bent metal clips.
-
Hi I finished my first elm burr table yesterday. Its about 5' long and 18" high. I learnt a few important lessons along the way - very frustrating at times but I'm pleased with the end results. The shelf is made from 1" black walnut dowels and took about a day to get right, using a hand drill and aligning the holes without a pillar drill is a painful process! I wanted to use Osmo oil but the customer wanted a glossy varnish finish so he wins Table #2 will be much simpler. Cheers
-
Hi Here's a couple of pictures of elm I milled today with great colours and grain. These boards are just over 6' long, 24" wide and 2" thick. Took less than 2 minutes to mill with my 880 and newly sharpened chain Cheers
-
Hi Steve, the thin teeth score the edge of the cut and the fatter teeth cut the chip out. I have the same chain and grinder and use it on both at 10 degrees. The scoring teeth are specific to Granberg chains. Cheers Tony
-
My last Christmas order, delivered on Christmas eve. The bench seat is made from elm and overall its about 8' long. I think its looks more like a labra bear but the customer liked him so all good! Happy New Year Tony
-
Merry Christmas everyone. A giant crab made from some sort of pine I milled a few weeks ago. Not sure of the timber type but it has a very wide reddish heart with little sapwood. The turtle was carved from macrocarpa. Its my first one and the customer was very happy with iit - he bought both for £500 plus a heron for £250 and gave me a nice bottle of champagne Cheers Tony
-
It won't and I never suggested it would. However the Terram creates a harsh environment for the weed seeds to propagate as their roots cannot penetrate it into the soil where the moisture and nutrients are. The future consequences are not a concern for the OP provided he states his terms clearly on any quotes. However in this case he did not use the spun material that his supplier offers and used a ground cover fabric which is not designed to prevent weeds coming up. The OP should explain to the customer that he was supplied the wrong product, he should lift and replace with a spun product and explain that it is a weed suppressing not eliminating product. He should also state that the new fabric or any fabric for that matter cannot prevent weeds from appearing, just making it harder for them to do so.
-
Hi, you need to use a membrane with spun fibres not the woven stuff which as demonstrated is very easy for weeds to push through. I used Terram1000 which is also used a ground stabilisation/soil separation layer. You can buy it 4.5m x100m rolls - its around £150. There are other spun membranes on the market which are available in smaller quantities. I recommend you shovel it all up or if space, pull the membrane and gravel to one side, lay the Terram and then replace the stones. Make sure your future quotes refer to the material as weed suppressing not weed proofing. Good luck!
-
Hi Mark Yes they are for sale and indeed I sold most of them today via Facebook, netting £360 - they were mostly £25 with a couple at £30. They are very easy to make, about half an hour each so better margins than any carving or table I have made! I can make you a kit tomorrow that you can self assemble for the cost of postage plus £5 I have a few to take to the post office tomorrow so will get a cost for you then. Cheers
-
You ask a tree surgeon for logs and he delivers rings -whats a man to do? Only 56 days to Christmas so no time like the present to churn these out!
-
Hi Rob, I'm afraid I'm largely ignorant when it come to softwoods, needles or scales and this had needles! I have another section to mill and there is a another tree of thesame type still standing so maybe a picture will help ID it. Cheers
-
Hi Rob and thanks for your comments. I filed both lugs down a couple of mil or so with my flat file and it slides over the bar without snagging - it is now no longer called 'bastard grinder' I milled a pine of some sort today, not sure what variety and it made a pleasant change from milling hard oak and elm - superfast and no effort whatsoever. Didn't half gum up the chain though! Cheers Tony
-
Good evening There are internal casting lugs about an inch long and 3-4mm wide and deep on the grinder where it fits over the bar and they are fouling the 880 56" GB bar (404 chain) I recently bought. Its fine on my other narrower width bars but the gap is not big enough - I don't fancy hand sharpening all these teeth and was wondering if its OK to file down these protruding lugs to get clearance? Has anyone else had this issue and managed to resolve it? Cheers Tony
-
Yes I can certainly agree with that sentiment - here's yesterday's milling efforts done in the rain only for the sun to come out when I finished! I used my new 880 with a 56" bar which certainly tested the structure of the 48" chinese mill: On inspection of the worst cut I had made on arguably the best wood I have (3rd picture), the nuts holding the depth gauges eased off and the the mill gradually increased the depth of the cut through the length of the board, from 2" thick to almost 3" at the end. The nuts were not finger loose but must have loosened enough to allow the mill to drift. To make matters worse, one end of the mill moved more than the other creating a compound wedge board Needles to say when i tried re-milling the board I moved the problem elsewhere and its still wedge shaped! To add insult to injury the chinese mill cost about half what I could have sold this board for. I've never had this problem on the 36" Granberg mill I have which uses more substantial brackets, rails, U-bolts and nuts. Today I tightened my nuts until they squeaked and the slabs came out fine Cheers
-
Good evening Here's a memorial carving I produced last week for the family of a young girl who passed away at 13 due to a very rare condition, juvenile sandhoff disease. Her last wish was to get a message from Katy Perry and the combined might of the internet made her wish come true with Katy sending a personal video message! #youreafireworksophie trended worldwide. The carving is an elm slab mounted on a pitch pine base using a french cleat for easy removal in winter. Cheers PS tried rotating pictures every which way but still come out sideways
-
Good evening and thanks for all your replies. I have tons of elm here but no kiln unfortunately. I know her stove will dry it out but to go from 50%+ moisture to less than 10% in 24 hrs might just cause a few cracks Can you send me a picture of the huntigdon elm you have Mr Muttley? I can look into the haulage costs to see if its remotely viable - the customer does live in a £750k house! Cheers
-
Good evening, A customer is looking for an elm mantle beam, preferably with burring to use as a floating mantle. The dimensions are approximatley 1800mm L x 200 W x 100 thick and kiln dried with one waney face. I can be flexible up to a point on dimensions. Thanks Tony
-
Yes these are some of the reasons I gave to a customer who had 3 beech twin- stem trees in her garden. I got the tree guy to leave them at 6/7' then put 6 carvings in their place. I charged £150 per carving and it was done in 3 days so a good result for all concerned. All chainsaw and blowtorch as there was no power on site. I have given my cards to several tree surgeons and pay them a comission % on the value of any work done but its hard work - the majority ring the trunk up and I never know if they offered the option to the customer. Cheers
-
Don't delay, has to be gone today!
-
Not my tree but spotted on Arbtalk on FB. Contact Nathan Dean Barnett on Facebook 07725691275 , Barnett Tree Services, Burton upun Trent Hope someone can use it!
-
I'd just like to publicly thank Rob at alaskanmill.co.uk for his helpful advice and putting together a great deal on a 56" GB bar, 2 milling chains plus one free (at 144 links thats a lot of free chain) and a 48" mill. Having just spent £1200 on a new MS880, Rob's prices sweetened the deal, thank you. #donttellthewife! Cheers, Tony
-
Hi everyone Here's my first attempt at adding a back to the benches I have been making - a complete pain in the ass! Lots of head scratching and cursing then I squared off the back of the log and fixed a tapered 6x2 to hold the back rest. The back is bolted from behind to the uprights after I rebated it to give me more depth to the seat. I found lots of room for error and I was wondering if any one has found a simple and quick solution? Cheers Tony PS I know my cats need more work than bench backs
-
Hi I have milled some Turkey Oak and whislt the boards look good and promising when milled, they have cupped and cracked quite badly (2" and 5" thicknesses). The sapwood is not durable at all. I have used the timber to make HD chopping boards and house signs as the wood is very hard when dry. I still have 4 butts around 2.6 metres long x 36" diameter which I will mill into large chunky benches but I'm in no hurry to do so! Best wishes Tony
-
Please accept my apologies for not furthering the development of chainsaw carving beyond yet more owls - I promise to try harder next time
-
A clanger? A clanger?? OK I concede there are some distinct similarities