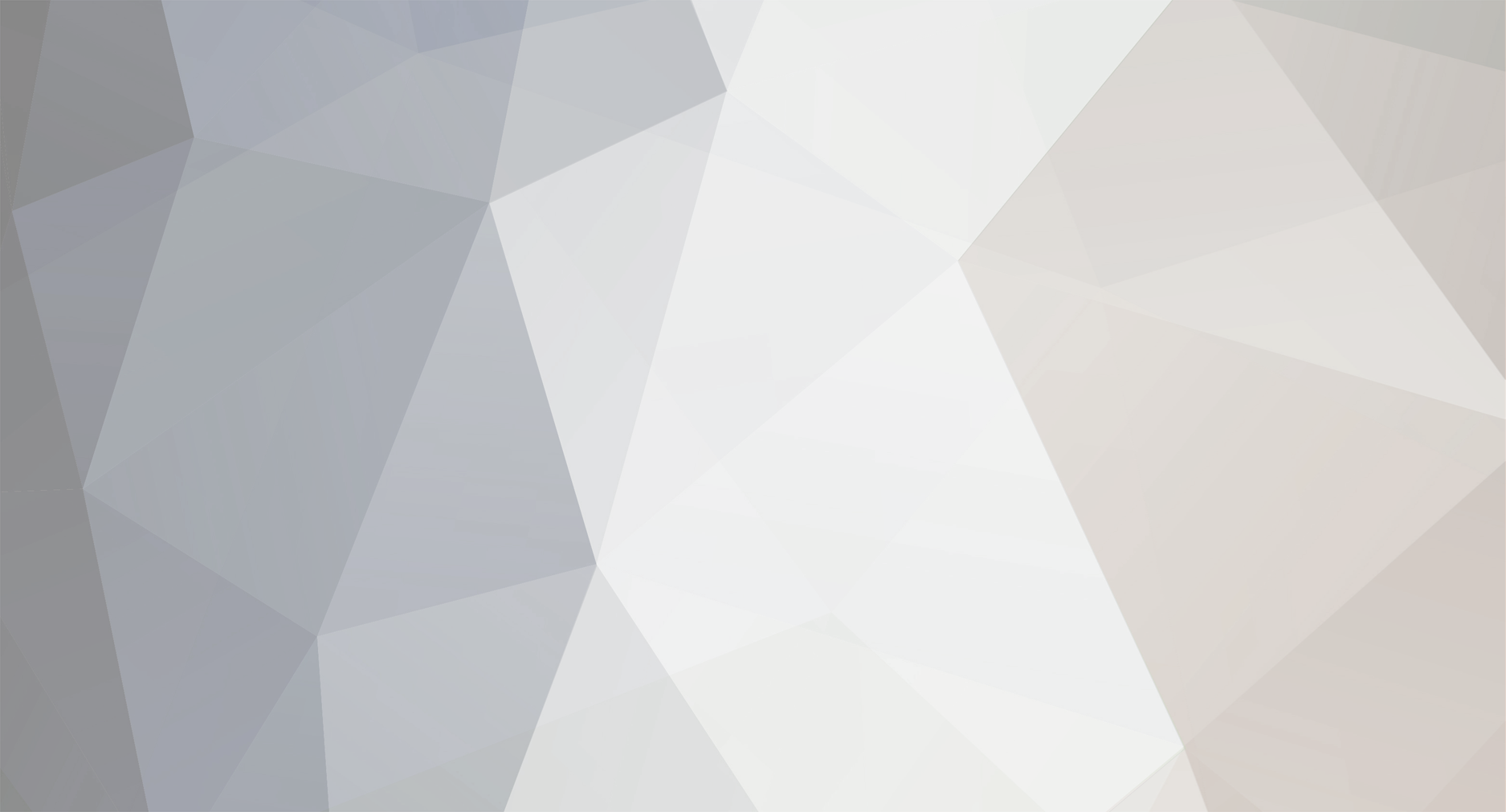
MartinN
Member-
Posts
20 -
Joined
-
Last visited
MartinN's Achievements
Apprentice (3/14)
Recent Badges
-
Anyone still advertise in yellow pages and yell.com?
MartinN replied to Rye Oil Ltd's topic in General chat
Hi, just for info as I am in a different line of work. I've advertised with YPs for 23 years. I got a deal this year??? If I advertise on Yell.com £1700 worth of advertising I get that discount off the book advertising. They keep trying to get me to do Yell.com so no additional cost to me. The Yell.com went live at Beginning of March. I always monitor where jobs come from. So far not one single job! Yes not one job. With regards to the book advertising I've found an increase in the last couple of months from the book advertising. Also prices are less sensitive as most of the cheap boys and girls no longer pay YP for book ads. I spend £100 a week overall and generates £400-£500 worth of nice top profit work. Internet is so price driven. Out of areas, I pulled my book ads as they weren't worth it and website pulls in work. I spend £1000 tops on web promo, hosting adwords, etc It generates business but it is defo more competitive. Oddly I've found this slight increase in younger people using book ads as they've been had over by the internet a few times and when they've tried to get redress it's a prepay mobile with a fake address and police trading standards, of course, don't want to know. Though I have trimmed my ads to suit reduced competition. It's a bit like being a chimney sweep, less chimneys to clean and falling but the rate of fall of sweeps is greater. -
Thanks for posting pictures. Looks good. Definitely a top setup for the two drums. How long is one cycle would you say, till end of gassing?
-
Sounds like you have a neat system going already. Any chance of photos? Refractory is not really designed for moving and would crack. Weight is an issue as well. The insulation boards and blankets are a much better bet. Some have carcinogenic properties from dust due to small particle size. How long is your burn from for 2 drums to cooling?
-
Yes indeed. Using brick means a stationary retort. These exist far and wide but the economics of moving wood to the retort kills limits, dramatically, the profitability. I have just had 3 BBQs this last week using " oxford charcoal co" charcoal. One box weighing 3 kg. I always water down charcoals after I'm finished leaving a bed for the next time. Before Using English charcoal I used Argentinian not through lack of patriotism but lack of availability. One 3 kg bag would do just one BBQ so at £1 per kg that £3 per burn. English works at at £3 per burn, is much easier to light and is ready much much quicker. It's a no brainier. Unfortunately customers are generally too thick to do the maths and buy on weight. Getting the cost of production down is the key to transforming this business in the UK. I think the figures are about 94% imported. Once you've used English charcoal you'd never go back to cheap imports, though the American is quite good too and longer lasting. Oil drums in a mobile application are ideal due to low cost £8 to £10 each but as in the Adam retort, see earlier link you will only get 60 kg per burn. At £1.25 wholesale that is not a lot. In my business I charge out £400 plus per full day (nowt to do with wood) and pro rata. I don't do much per day but what I do is profitable. I'd like to do this as a side line but I'd need to produce 1 to 1.5 tons per week finished charcoal to be justifiable. About 4 to 6m3 per week processed. Moving that amount of wood a large distance to a static kiln or one in a remote location I think kills the business model.
-
There is no problem producing a durable, relatively low maintenance retort for producing charcoal. It is all down to the economics. 316H stainless is indeed a good material to use. It is more resistant to the acids produced in pyrolysis although any chlorides present can make for an agressive corrosive environment. I looked into getting a retort made last year and the cost were prohibitive let alone the problems for getting welding done. In fact I could not get a quote. It is a specialized area for thinplate welding in stainless. Most high end welders will only touch thick materials. Apparently welding 1" or 2" thick material is easier then 2mm thick. If it is not done correctly then the weld will fail relatively quickly especially at the higher temperatures of the retort. One major advantage of mild steel. With regard to warping the usual practice is to have things like dished ends on you retort tube. In stainless this is upwards £400 each for small and if you want it in heat resisting stainless £1000 + each and that's small thin section. Think of a thin relatively thin walled hollow sphere . Heating it up will cause less distortion and stress than a flat plate like the baking tray twisting in the oven. I'm in the process of a new design on a cheaper basis ignoring all the above! So far estimated costs are in excess of £3,500, though that does include some tooling to manufacture. Time permitting I'll make a 1/5 scale model to clarify everything goes together. If it does I may bite the bullet, cash in the pension and have a go, but I've got to be pretty sure it will work. Still looking for a way to test it in Solihull. Hint hint. Initial full scale design, on paper, will give half the yield of the Exeter, but will be scalable. If it works I think it could be scaled up to 4 cubic metres for about £1,500 more and still transportable on a trailer pulled by a small car. I have been reading the posts on this site regarding the Stein Arb truck and think this would be a good way to move it around a wood. Weight will not be a problem for the retort. The logic for operation would be for coppicing around centre of 2 acres and pull this wood in for processing using Stein truck. I guess this wood be about 6 tons per annum for good coppice? And then move on to the next 2 acres. By the way I' m not a wood folk person so I'm going on info on this forum regarding yield. So coppice 2 acres, move and store under temp cover, then move onto next. By the time you've done 100 acres back to the start ready for retort after some drying has been achieved. Capital investment on this would be small, trailer, saw, Stein truck, training in coppicing chainsaw ins etc but not a lot else apart from a spanking new retort. Not a huge amount for someone to nick. If I don't cut it grows a little more so could fit in with my existing non woody work. Please find holes in my logic so I can patch them up. All thoughts positive and negative welcome! Especially if it stops me wasting money.
-
Smoke cloak and remote alarm.
-
For those who would like to do fine woodwork but don't, you can get some good DVDs of the likes of David Charlesworth. One of my favorites is Rob Cosman's hand cut dovetails DVD. Amazing the speed and precision that can be achieved. I think he does a demo on youtube.
-
NRI kiln specify corton steel due to a protective coating slowing corrosion. I'm not sure ring kilns are made with it here. With regard to the true heat resisting stainless steels they are not practical as these are no longer made in the UK I've just been quoted minimum order 16 tons to get closer to decent price which is still at a premium. It is not so much warping but as the steel softens, loads distort the metal easier so thick plate with frequent supports would be required, this all adds to weight and cost. When stainless steel operates at high temperature the weld is critical and to get them done properly is expensive and not that easy to find people with those skills. All this adds to weight. To keep more mobile, size has to be reduced killing the economics. Increase in size means fixed position and the costs of bringing wood to the retort. Taking the retort to the wood is optimal especially as the V.I. suggests, going in as a clean up operation after felling. I'm toying with the idea of building a prototype and trying it in my garden, when the neighbour who does not like bonfires is away. Budget is about £1,000 and should do half of the exeter but I should be able to move it easily without lifting gear or power equipment. If it works it could be scaled up to 3 times that of the Exeter with the same spec on weight. There is some complicated metal forming which I may try to do in house unless I can find a local fabricator.
-
Probably because no one has been able to crack the cost benefit ratio in the design. I think the Exeter retort is more expensive now than at the original launch price. I think it started out at £12,000. If you get 300 burns before significant corrosion of the inner chamber, reducing wall thickness, then that would be about £40 a burn before big remedial work like replacing the inner chamber. I.e. About 30 pence per kg which is quite high. The Exeter does seem to benefit from being easy to replace this part. Maybe there is an argument for ordering in this part, easier to ship, and sending the this old bit back for remedial work. That way it does not need to be out of action for any length of time. And rig up for doing this replacement on site. Say at £165 per burn then that would be about £50,000 say £12,500 per annum if 300 completed over 4 years. Is that realistic? In other words adding about £9,000 to the bottom line, once the cost of the retort is taken into account. For a self contained unit it is attractive. I guess anyone working doing firewood etc is likely to have 40 tons of wood not suitable for firewood that is just waste, ideal for the Exeter. Having mobility and easy to service (do remedial work) is the goal for the one man business. If treble the volume at half the capital outlay could be achieved it would boost wholesale sales after capital cost to £34,000 per annum for the same number of burns. I think this is achievable, and may be more. Getting the volume of raw material then is the problem 150 tons plus per annum. I'm not sure how much is physically possible in terms of what coppicers move in a day. Somewhat back of the envelope calculations, I know. I'm not sure what it would cost to buy in 150 tons in other words what would be top price of material feedstock.
-
Is that Fuelwood in Warwick?
-
I'm on the case it's all I dream about these days. Your thoughts on my taking the following approach to said wildlife trust or failing them anyone interested. I dispose of the wood thinnings on site and in situ using my revolutionary wonder machine and give them 30% of production bagged up in those nice Selway Charcoal bags for them to do with them what they like. Or I get myself trained up to do coppicing and help them out. I try and sell the remaining 70% to see what the market is like and if the figures add up. The wood is marked on the map as a coppice though from what I can read it does not look like it is managed as one. I could be wrong. Am I right in thinking if you coppice wood less than 150mm then you don't need a felling licence? How do you get on bringing back old coppice if over150mm, if that is the case.
-
No private jet, no tour bus, no caravan but a bright orange Vango Force 10 tent, the height of luxury. Only wish the missus would see it that way. If I can get something tried out up here that works, I would appreciate the wisdom of the V.I. for you know more than me! I looked into getting something produced in heat resisting stainless steel. As we no longer produce said steel in the UK the price is 4 times what it would otherwise be. Problems finding fabricators and getting prices for said work was impossible. So change in design. Round 2. If you could get a retort to the wood rather than bring the wood to the retort would that make it much more economically viable? I see all the heavy equipment and time used for the processing of the wood and guess that's what kills the economics. Too much time on my hands, I've just found a wildlife trust 1/4 mile from me. Lived here for 10 years didn't know it was there. I wonder if they can help? My goal is to create a process requiring very little in the way of capital investment but which could offer a very good rate of return. If this can be achieved then more woodland can support more jobs at better rates. I believe that the UK's second biggest sector in our trade deficit is in wood and products of. Somewhere in the region on £6 billion. Imagine if a small percentage could go back into the UK countryside instead of going abroad. As you say we are not far off the figure that the public will bear, for the charcoal at least.
-
I suspect it could be one of the mark it up at a high price to give 50% off later. Yesterday I picked up one of the Oxford Charcoal company 3kg boxes from Waitrose for £7.99 a quite acceptable price and much better than last year when they did small 1.25kg bags for £6 if my memory serves me correctly. The supermarkets always run out way to quickly round here, just as the BBQ season starts, so there must be more market opportunities for uk charcoal. I did some serious research into getting into producing charcoal last year. I was quoted £1,000 per ton collected but bagged by me, last year. My logic was around here it would be not so difficult to get into the shops on the grounds that uk charcoal sold out at the beginning of the season. I even tried to order in a dozen bags locally and they could not get any. Sold out. I quite liked the look of the Exeter retort but couldn't square the cost vs the yield. I have spent some time developing (on paper) a retort system that would be man portable, i.e. Could be taken into woodland by one person, without machinery, to where wood is felled and which is also expandable. I approached an estate owner locally to prototype the system but to no avail. I think he was interested in doing it himself as he already has a large firewood business. Here in the Midlands there is a lack of woodland. Or at least that I can't find. I'm quite happy to buy wood in to try to commission a working system but I don't think my neighbour, who does't like wee small bonfires, would appreciate me burning 4 m3 of wood in my back garden. Any suggestions would be appreciated. I have read a report that a single person could, with hard work produce 1.5 tons charcoal a week. I was hoping I could improve the figure. Do you producers think this is viable? Ideally a traveling system which could be used on thinnings etc which could be taken to where they are. Presumably moving charcoal out is a lot easier to move than the wood to the retort.
-
Revisiting this thread. How are the Exeter retort users getting on with them. I noticed that Sainsburys are selling the Bio-Regional charcoal at £16 a bag (3kg I think) Do you think this is a realistic price? Or is it inflated to give discounted price later. I keep thinking of getting into production, apart from lack of wood and where to do it and keep checking out viability. I think £16 is over the top especially when put against a £4 bag supposedly for the same stuff. Can all you charcoal burners out there get £10 a bag.
-
Last 3 vans I bought from new. Vauxhall with a 28% disc off list with7% disc on optional accessories like upgrade on sound, heated mirrors, air con, sat nav, up-rated suspension, up-rated power etc. The only things I couldn't get were cruise and leather! Buying new you get exactly what you want over s/h. Cost £15k plus VAT. The only thing I did't get was alloys and metallic. Coming up to 9 years old. First 3 years no MOT required, that can cost money if the van is off the road. After 3 years a gamble. I get it serviced at a top place who look after me. That's just £1700 quid a year. If the money was in the bank that would be another £100. When I come to change it I might get £1,500 with all those extras. I've had a couple of bigger bills recently but even with this servicing, all tyres etc I calculate an average of £600 a year average so that all comes to less than £50 a week for the last 9 years. It gets me from a to b in comfort. I spend more on my phones. So for less than £50 a week I get a top spec vehicle fully serviced and maintained and don't have to worry about dents scratches and mileage. As said before I'll get something back when it is sold. If there was an expensive fault then I'd just order a new van with the money I've saved over the years. You still need tax insurance fuel etc but then that applies to whichever method you do.