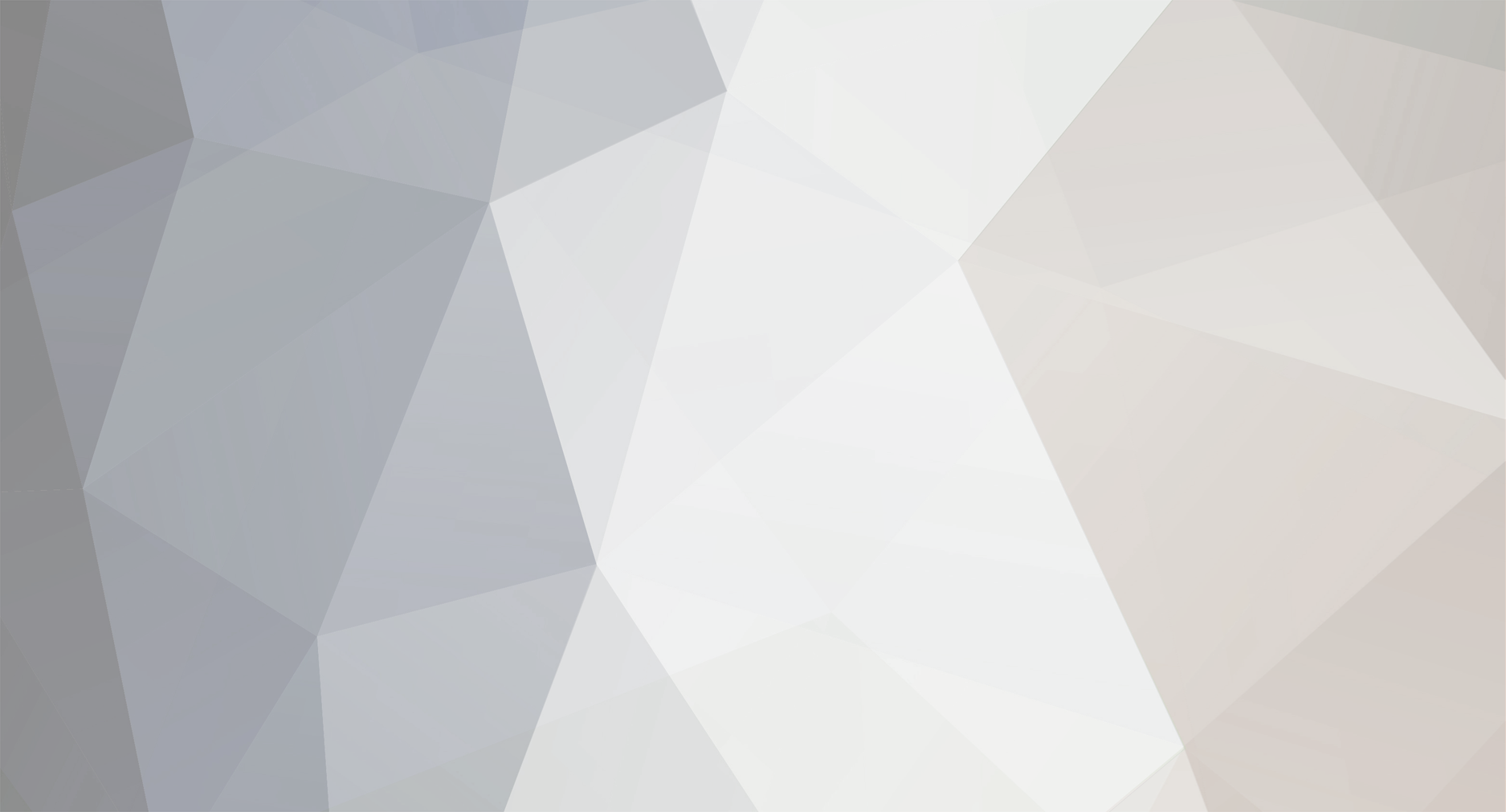
Westwood
-
Posts
27 -
Joined
-
Last visited
Westwood's Achievements
Explorer (4/14)
-
Rare
-
-
-
-
Recent Badges
-
A very interesting thread.
We do about 2000 loose cubic meters per year. about 30% Kiln Dried from eastern Europe.
We have been running retail about 5 years after a couple of years supplying rings to wholesale.
We own 100 acres of mixed woodland but most processing that we do comes from adjacent estates in 3 meter lengths processor ready and increasingly tight spec for our Fuelwood firewood factory.
Our prices per cube range from £80 to £125. We sell a range of accessories kindling, firelighters coal etc.
Our average order value is about £120 per cubic meter.
From our observation the majority of firewood retailers in the small to medium range either do it as a sideline to a day job or as a sideline to an existing business such as Tree Surgery or Farming. Sideliners have minimal overheads and capital expenditure, existing businesses have shared overheads such as barns and equipment.
As a stand alone business as we are you can either be very small with minimum investment or invest heavily to grow the business and achieve economies of scale which is the path we have chosen. We have up to 3 people full time and occasional helpers.
We know exactly the margins on bought in product. Capital and operating costs on sales marketing and distribution again are well known and profitability depends on volume. What is much more difficult to get a handle on is processing costs for bought in timber - we have two processors one for volume and one for small stuff and arb waste. It is really clear small stuff and arb waste has much higher cost. We now avoid this or sub-contract it out to others as we do felling and forwarding in our own woodland.
Most of our business is from an developed base of about 600 customers within 20 miles of our site - about 70% comes from our website. We contact the base about 4 times a year for promotional purposes.
Agree with GDH about the hidden nature of expenditure - this is very true in processing which drives the majority of capital requirements. We do not operate kilns so we do not get the benefit of RHI - we operate forced air drying to supplement natural seasoning.
just a few thoughts to add to the debate - be very interested in what others think - do you get out of processing altogether or are you supported by RHI. How do you get profitability up on distribution - smaller area, fewer drops, larger trucks?