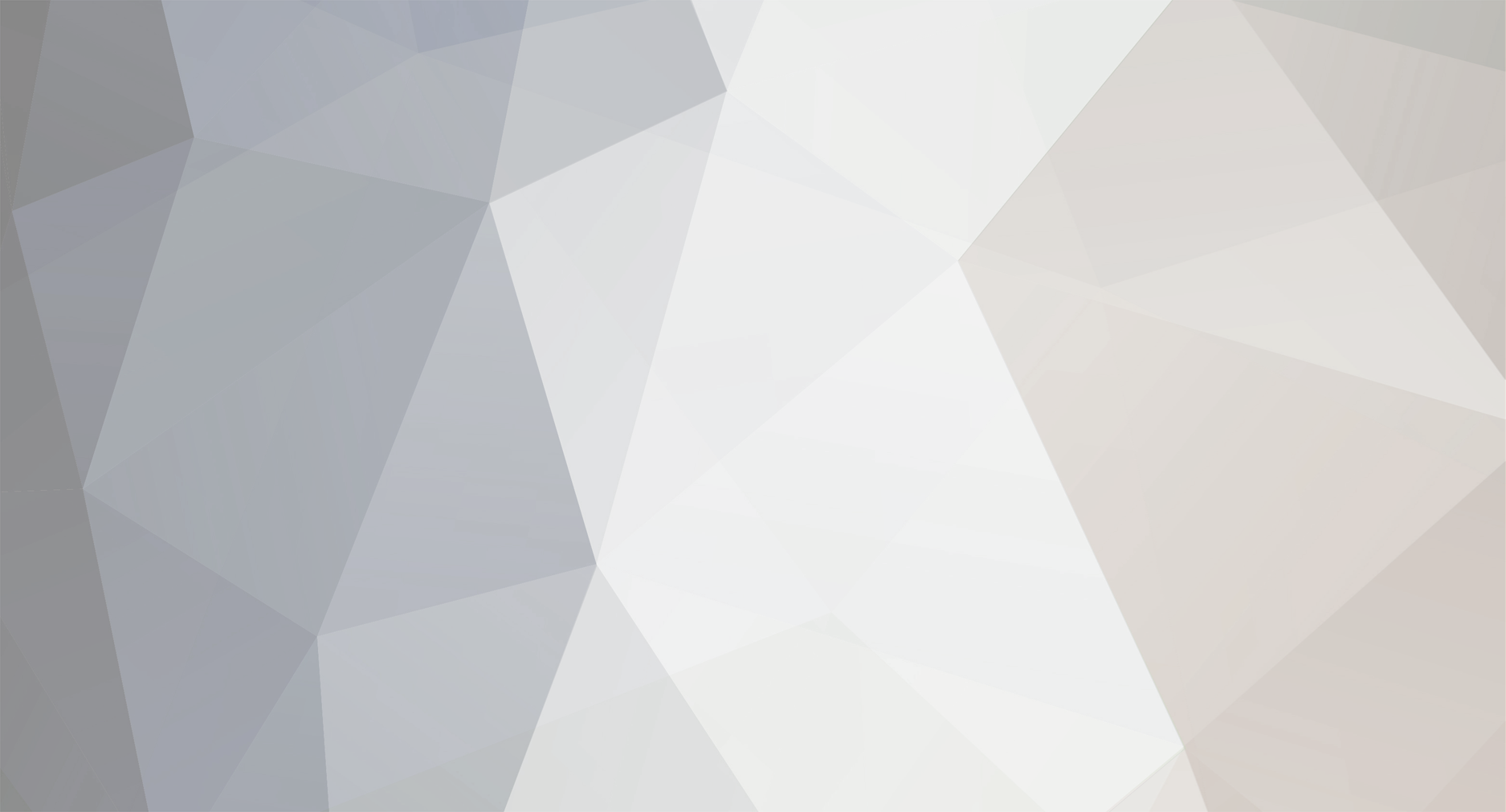
Malus
Member-
Posts
74 -
Joined
-
Last visited
Personal Information
-
Location:
SW Wales
Recent Profile Visitors
The recent visitors block is disabled and is not being shown to other users.
Malus's Achievements
Enthusiast (6/14)
-
Rare
-
Rare
-
-
Rare
-
Recent Badges
-
Nice one, thanks for the advice. Looks like you get a fair load on that trailer! It's holding up ok over the years then? Doubt I'll be loading the trailer up that high, I don't think the ergonomics of a grab on a digger is quite as good as a dedicated timber crane and I think loading high might be a little bit awkward. I think I'll have to play around with headboard height to get the balance right. I had a look at some of the ones Hywel Evans makes and his have a low headboard, probably for that reason.
-
Brilliant, thanks. I was planning on using a set of wheels from parnells, look decent enough and come with axles and a swivel hitch. Rated for 900kg, but will probably handle a bit more? What do you think? 22x11.00-8 Utility ATV Quad Trailer Kit P334 Wheels Axles & Swivel Hitch 900kgs WWW.EBAY.CO.UK 2 x Wheels, 22x11.00-8 4ply Wanda P334 Utility tyres on steel rim 4x100mm PCD. • 22x11.00-8 4ply Wanda P334 Utility tyres. For sale is 1 new 22x11.00-8 Utility ATV trailer kit with... They're cheaper on their ebay shop than their website. Ok good to know about the ladder frame. I've got some 70mm 5mm wall box section that I had contemplated using as a spine but thought it would probably be a bit on the skinny side, think I've got enough other box sections to make up a ladder frame. Not sure on how much weight I'll have on it but realistically it won't be much more than a ton, maybe one and a half. The digger can lift and move about half a ton when its got the grab and rotator on. The limit in larch is a 16' log up to 24" butt diameter I think I would consider buying one if I didn't have a load of steel left over from various projects that I'd like to clear up out of the way and put to use. Also if I can save a bit of money from buying kit it's easier to justify buying new tools for the workshop To start with I'll probably just bolt a 50mm ball hitch to the blade. In the longer term I think it would be better to weld on a drawbar receiver to the rear of the sub frame, with a pin on draw bar. My thinking is that then when on a slope you can keep the trailer uphill and the blade downhill as an anchor.
-
Planning on welding up a little forwarding trailer for my 3 tonner. Looking to use it for extracting logs for personal use on my mill, sometimes I buy windblows etc cheap where the forest owner wants them cleared without damage to other trees. Also hoping it will be handy for moving brash, but I'm not sure how it will compare to just dragging brash out with the grab. Does anyone here use one? Any tips on what works/doesn't work? I was thinking single axle with atv style floatation tyres, trying to keep it lightweight and also think it will turn better than two axles. Is it worth having a headboard or will it just get in the way? I think it would be handy for it to be extendable in length perhaps?
-
Could you just barrow in a lorry load of top soil to add to the lower spots? Then reseed or turf?
-
@tentman looking good but like you say looks a bit slow on the way down. Have you put it to use yet? I'd say a hydraulic ram arrangement will be better than the winch, the winch could be repurposed. Would make a really handy timber winch if it's strong enough. I guess you're planning on controlling it from inside the cab? It's a lot quicker than way and a lot quicker than a tractor knocker. I tend to run out a string line between strainers and then stab a good 10 stakes in, jump in the digger and drive them inm saves getting and out for each stake. The downside is it's difficult to get posts in absolutely vertically if you're working on your own. Just like a tractor knocker the posts often go in nice and plumb but as soon as you lift the post cap up the post springs off to one side, I guess that depends on what your ground is like.
-
Can you send me a couple of pics of the beech logs? Are they nice and clean?
-
In danger of repeating bollocks here but I was once to by an old boy at a farm auction that there were a load of excess ball pein hammers after ww2. They must have been made for a specific manufacturing purpose for the war effort. After the war they were repurposed and a lot were turned into hatchets. Might be complete crap but it's a nice story
-
I've used vinegar to remove rust in the past, just the cheap stuff. Soak the steel for as long as it needs. Important to thoroughly wash it after with water and then a coat of oil or something. Gotta be quick with this or you'll get flash rusting. Could possibly use bicarb or something in water to counter the acidic vinegar? I've not tried it.
-
Here are my two go to axes for splitting my wood. The elwell especially also gets used for hedge laying, it's a nice weight and handle length for it. Neither axe is much of a wedge shape so probably not the ideal splitting axes but hey ho. When splitting I usually use the elwell and I prefer to be on my knees with a low splitting block. Far less bending over and I make sure I've got a nice soft pile of sawdust to kneel on. With the nice light axe I find I can be pretty productive. The felling axe is one I found at the local scrap yard when I was dropping off a load of scrap. Couldn't believe my luck! Looks to me to be pretty old, blacksmith made with chiselled decoration on the pole. It was really pitted so I had to put it back in the forge to work the bit and then reharden and temper. I think it's wrought iron with a steel bit. Both handles are suffering from damage on the neck. It isn't from bad aim, honest! It's mostly from when the axe head gets buried into a log and as a result the handle hits the edge on the log before it splits. I guess it's a result of the narrow profile of the heads. I bought my dad a gransfors bruks splitting axe for his 60th and it's got a steel collar on the handle neck for this reason. I've not had a chance to try the axe out yet.
-
Bit late to the party but might be of use if you haven't sorted anything yet. I made up a lightweight set of pallet forks for my compact tractor. Like you I wanted to keep weight to a minimum to maximise the load of would lift. I used 80x40x3mm box which has done ok. The forks comfortably lift half a ton. I bent one tine when it wedged under a big root when I was picking up a log, couldn't the fork/root from the cab. With a bit of care something light like these should last a while. I can pick up both forks and frame on my own so can't be that heavy. One thing is I made the tines long for picking up bulky but light things, I'll have to make a short set when I get time - the long can be a pain at times. As mentioned above, get a big weight on the 3pl and maybe set your wheels as wide as they'll go. Could also balast the wheels by filling tyres with water. I ended up making a mount for the digger that uses the forks off the tractor. Pretty handy.
-
Thinking about it if the tines etc are made from hardox or some heat treated steel they are probably treated in sheets. Then you've got all the cutting and welding processes putting a lot of heat into the whole lot. Can't imagine they fabricate then heat treat? Then there's air hardening steels, I think chainsaw bars are air hardening.
-
I wouldn't want to heat something like a tine unless I knew it had never been and didn't need to be heat treated. It's amazing how steels properties can be changed by heat - chuck a file in the log burner and see how it performs the next morning. It won't cut anything but you'll be able to bend it back on itself. But more to the point I didn't have a heat source on me and had a job to finish. To be fair I wasn't blaming the tools and nor was I abusing the grab. Just interested to see who else has bent tines and how. If I had seen the tine was stuck in the log I would have put it down with a bit more care and not slewed away until it was free. Accidents happen and farming and forestry isn't exactly kind on tools!
-
That's a bit disappointing to hear after buying one recently based on everyone saying how good they are 🙄 to be fair though it's a brilliant bit of kit, very handy and speed up a job massively compared to moving stuff by hand or pushing brash with the bucket. Just would expect it to last. Yeah exactly, I couldn't believe you lot use them for digging stumps out etc 😂 are they joined as in a log grab then as opposed to tines? The tines are pretty handy for brash and the few rocks I've moved have been easy to grab and position.
-
I managed to bend one of the tines on my grab this week. Bent it back with a sledge ok but it took a bit of beating. Was a bit surprised it bent tbh, has that happened to anyone else? It's an intermercato tg16. Basically I was moving a lump of willow and I was rotating/dropping it off and when I slewed away one tine was lodged in a hole in the log. The log rotated and landed as expected but it just levered the tine and bent it.
-
Lopping the top off a hedge with a tree shear should be a criminal offence. If possible it's far better to lay it, if that's not possible then coppice it to get some decent, healthy regrowth. I've seen some horrendous jobs done over the last few years since tree shears got popular. I was looking at getting a tree shear for my mini at the start of the summer but decided against it for the time being. Mostly for coppicing hedgerows before tidying up the stumps with a saw. Just a heads up to give Evans and Reid a call, down in Neath. They make a small shear up to 150mm from memory and was quoted a bit over 2k plus vat earlier in the year. Was the cheapest by far out of all the ones I had prices for. Would be interested to know what it's like.