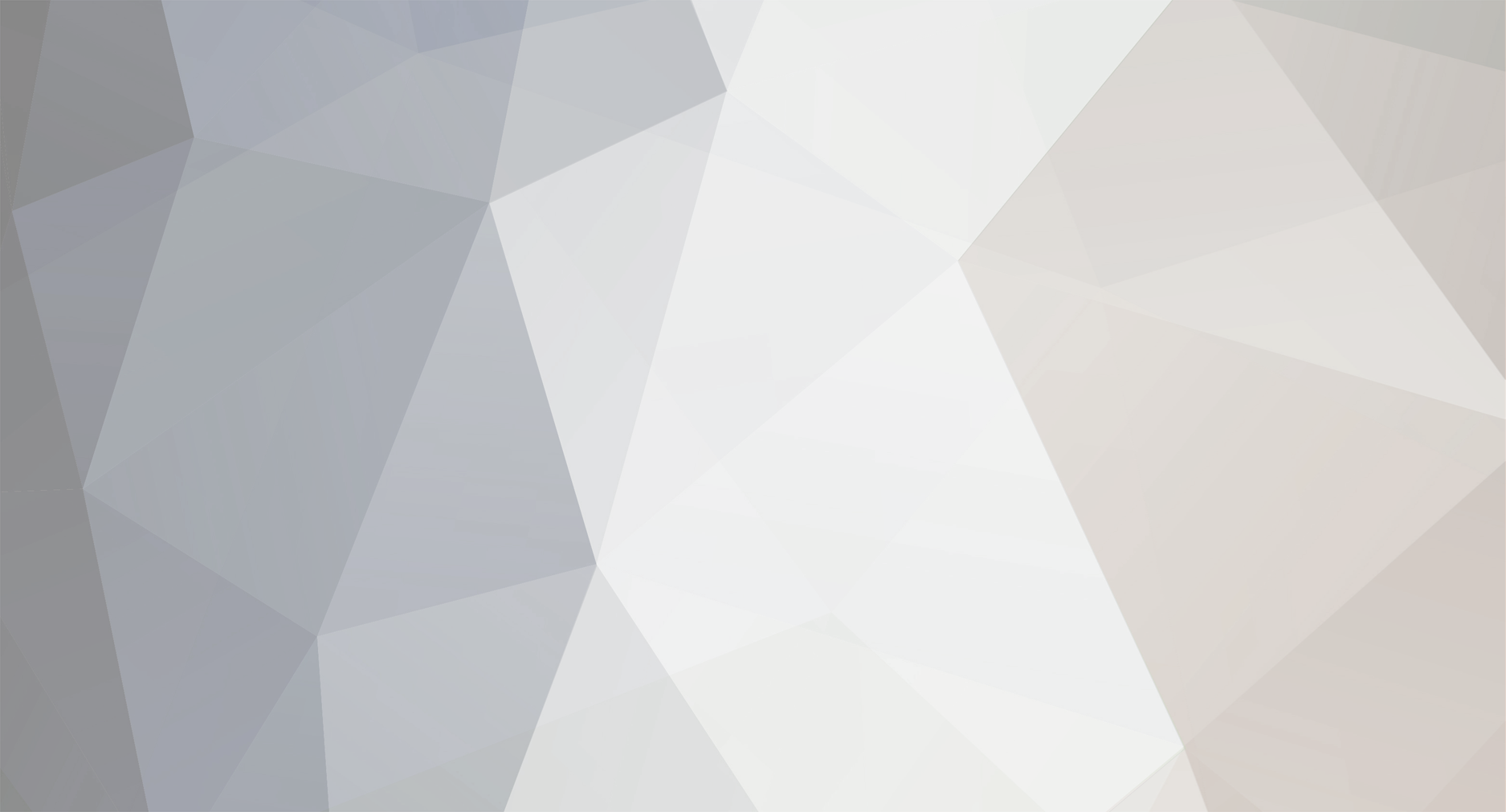
Skyhigh_Arb
-
Posts
45 -
Joined
-
Last visited
Skyhigh_Arb posted Find a freelancer map marker in Machinery Owner/Operators
Skyhigh_Arb replied to Jonny Burch's topic in Firewood forum
Skyhigh_Arb replied to Skyhigh_Arb's topic in General chat
Arbtalk.co.uk is a hub for the arboriculture industry in the UK.
If you're just starting out and you need business, equipment, tech or training support you're in the right place. If you've done it, made it, got a van load of oily t-shirts and have decided to give something back by sharing your knowledge or wisdom, then you're welcome too.
If you would like to contribute to making this industry more effective and safe then welcome.
Just like a living tree, it'll always be a work in progress.
Please have a look around, sign up, share and contribute the best you have.
See you inside.
The Arbtalk Team
We have placed cookies on your device to help make this website better. You can adjust your cookie settings, otherwise we'll assume you're okay to continue.