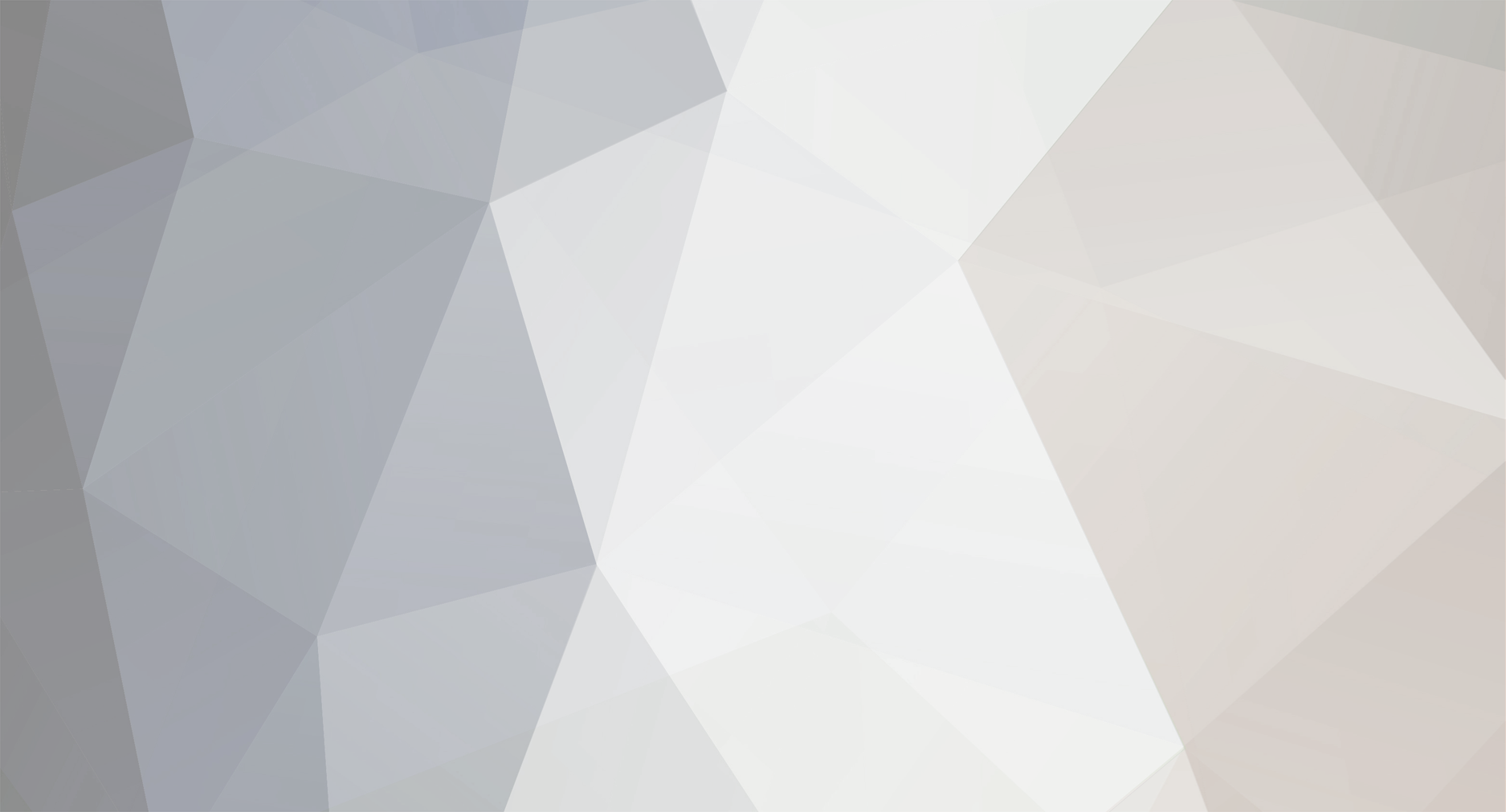
cjdg
Member-
Posts
51 -
Joined
-
Last visited
Content Type
Profiles
Forums
Classifieds
Tip Site Directory
Blogs
Articles
News
Arborist Reviews
Arbtalk Knot Guide
Gallery
Store
Freelancers directory
Everything posted by cjdg
-
Sorry to latch onto the back of this thread but I have the exact opposite problem. The lower roller bolts keep coming loose about every 5 to 10 hours of use. They work out a bit and slow then stop the roller from working. I have tried all sorts of Locktight / tite and in particular No 243. I am considering in my desperation using Araldite! Any ideas from this forum as to what to use? Chris George
-
Anyone out there within fighting range of OXFORD who knows of any competent person or firm that could set me up with, ideally, a second hand winch with all the hydraulics installed as it is clear to me that I (to put it politely) need guidance and at my time of life I would rather pay to get it done right. Chris
-
Thanks for the replies. I should have explained that I need the Avant with the "useful" attachments attached and to have the capacity of using the winch to get me out of trouble when I get stuck hence my comments of putting it on the back as recommended by Paul Helps. The sort of logs I will be hauling out and which may well get stuck in mud might well have the Avant moving instead of the log! If it is on the back, I can at least use the log forwarder grips to hang onto a tree when I pull the log out. I might need something that I can cart about the wood using my forwarder, grab or pallet forks and have it independently mounted to a fixed tree or stump. Never done this before hence the seeking of advice...
-
Advice needed on winches to remove very large logs (up to 1 metre diam 4.5 m long "just" able to be picked up with the large Avant Grab without - too often! - tipping up) ideally using the Avant. The thinking is to put the winch on the back where the weights usually are perhaps by extending the mountings so as to get some weights and the winch on at the same time and using skids or similar to haul the logs over boggy and other ground where the Avant cannot reach. It may be that the consensus of opinion is to have the which on a separate wheeled frame to attach to stumps. What is the best machine and what power source? Battery does not sound feasible for all day work but might be ok for the odd job here and there. Having it on the Avant is a bonus as I have spent hours getting it out of bogs and soft ground with ropes bit at a time using the extending arm - very boring Chris
-
USA based "Chainsaw" type brush cutter disc - anyone seen one in the UK
cjdg replied to cjdg's topic in General chat
20 to 30 mm but not very wooden and strong so the Oregon tip sounds like it might be the ticket. Thanks. -
Dear All, Heavy Duty Brushcutter SALTYCORN.COM Shape Up Your Yard! Is your lawn looking a little out of shape? Is your garden overgrown? Do your hedges need a haircut? The Heavy Duty Brushcutter is like having a lawn crew to... Came across this USA tool on a FB video that looks to be too good to be true, rather dangerously cutting down small trees and making mincemeat out of small brushwood. I need something for thick bamboo. The Stihl circular saw blade is useless. Anyone come across anything similar in the UK? Any recommendations as to what would be best on my HD Stihl? Am contemplating welding on a (sharp but damaged) chain (the undamaged part!) to an existing plate as a DIY. Thoughts?
-
Sorry about the photos' quality Now for the questions. Gareth has suggested HP Lithium grease for the sliding sides of the feeder roller assembly but what should I use for the bearing? It is a plain simple metal shell with a PTFE end stop. I have copper grease and will be buying HP lithium. It seems to me that it is a slowly rotating floppy (loose) bearing so a gap filling thick grease that does not melt away would be favourite. One of the splines is well worn and I am pretty sure it is the lowest one. Can one swap top to bottom on the basis that the bottom gets more wear (indeed is that true?) or Do you just wait till it goes and THEN replace it? or Replace it now? Just remembered - ran the machine for 15 mins as recommended by Dean and BOY was it smooth - not a hint of all the vibration pre repair so concluded that the flywheel was out of balance when I bought it which does not surprise me but I have done about 200 hours of productive work on it so no complaints cheers all Chris
-
An update and further questions. Firstly, a BIG thank you to all helpers especially Gareth whose Green Plant service is exceptional. Here are some photos of work to date which may be of interest. Got the anvil blade distance pretty well spot on at 2.5 mm and 3 mm respectively. Used two shims which was the same as before. First problem was to invert the anvil which was welded on. Ground that off carefully but one of the screws (countersunk Allen key) ended up with a round socket so had to use a blow torch and club hammer. The first was to loosen up the contact area and the second was to rotate the anvil off the tail end of weld which was not fully ground down to avoid grinding the metal. Judicious use of a centre punch at an angle got the Allen bolt moving sufficient to get a grip. Once out it was easy to clean it up and swap over and decided as it was all messed up with weld to tack it back on where the plate had been worn down. Then fun and games with a large club hammer and a mate with a blow torch to move the outer casing back into shape. Followed Dean's instructions with a slight modification in that I put on both blades and rotated the free floating flywheel to about 10 different positions to see if it "fell" to a natural low point but try as I might it stopped at any point in the 360 so considered it was OK. Will post photos with this record and pose question in a new post
-
Thanks for that advice. Rotor shaft is OK was a tight fit.
-
Latest question please. The anvil on the main plate is a) welded on by the same sort of animal to which Dean referred. b) is well worn. I appear to have to choices: 1) build it up with a weld in situ then file or grind it to a roughly square section shape 2) grind off the weld, undo the nuts and buy a new anvil and put it on I favour No 2) and if that is the consensus would it be sensible to animalistically tack it on with a weld as well? I can only presume that this was done (as it was for the anvils on the flywheel) due to experience of them coming off in the past So Questions Do I go for 1) or 2) If I go for 2) do I weld it What experience do others have of any such NEED for welding with the anvils coming off or bolts coming undone? Photos of works to date (for those interested) not in any particular order. 7943 7944 7942 are of the anvil
-
I knew it had to be something mindlessly simple
-
Latest development is that I have managed to clean off the machine and get it inside. Thanks are owed to Gareth who has supplied the parts for tomorrow (couriers permitting!). Dean said "After taking off the drive pulley, I undid the four bolts securing the front bearing housing and withdrew the flywheel." Well, I have just spent an hour and a half with a mate trying to do those six words "After taking off the drive pulley" !!!!! There are supposed to be three grub screws holding in a conical taper lock bush and, as one was cross threaded, it was empty so that left two to undo opposite each other luckily. Once undone, logic dictates that you tap the pulley wheel off the taper onto the shaft in the direction of the flywheel away from the engine THEN pull the bush and key out towards the engine. The bush is well and truly "stuck" in. I have tried a blow lamp both sides of the bush, heating the bush and wheel rather than the shaft. I have put on gallons of penetrating oil spray let it go in and then tried to shift it. I have tried shifting just the key with a long blunt screwdriver to loosen it off. I have tried levering it off with the bush as a last resort. Must be doing something that should be mindlessly simple wrongly! Any ideas chaps?
-
Thanks Mick and other Chaps! Gareth, Thanks for the offer but before I read this, I rolled up my sleeves this afternoon and got as far as getting to the rotor wheel, so everything is off including the plate and roller assembly and am now going to take off the rotor wheel but not sure just how it is extracted. I assume that a little penetrating oil, an assistant to hold and put pressure outwards on both sides and then tap it to loosen it and pull it off? See photo below. I see that the fans are sold in pairs and wondered if (as is said above it is a common fault) my original thought of only replacing one was misplaced and that it would be best to junk the sound one on there and put in two new ones? I am puzzled as to what the strain is on this fan as it is only driving air and not as if it is taking much load as for example the anvil and blades. Is it worth replacing all the bearings at the same time as they do not appear to be bad? Seems to me a small investment given the time taken to take it all to bits just to replace them. Thoughts?
-
Big bang! so switched off PDQ. Sounded like a bearing (casing?) had gone with lots of heavy knocking but on looking at the Maintenance manual could not see this part shown in photo below. It has evidence of metal fatigue over 1/3 of the cracked casing (Image 78970. I suspect it is associated with a bearing housing. I need (I think) the following but subject to better advice: 1) a workshop manual if one such thing exits outside favoured manufaturers' listed agents 2) the spare part in question 3) advice as to what other parts I should sensibly replace since I have to take it to bits anyway (full set of bearings for the roller") Question The machine is in Oxford OX1. Does anyone know of any recommended service agent that can provide an estimate (it would not be easy to provide a quote till it is in bits) or guideline price and rates to take this off my hands. It is outside but at a push (literally) could just about be put inside. Chris G
-
Does not appear to be VERY resistant but then it never did. It is certainly not "easy".
-
That was my idea as well -works for a motorbike but was not sure of a small cylinder saw. In fact the fuel bubble is firm and appears to be pumping fuel
-
OK, It was Christmas Eve and I just could not resist a bit of grafting to finish off a job of chipping and wanted to cut a bit of brash to fit in the chipper and my reliable old 550 XP 2 years old and probably with about 300 hours on it would not start. Its been good as gold for two years. It had not been used for about a month, had about 1/3 of the tank full was in the cold so not dried out and it "appears" that the pump is working (but no bubbles). Pulled my nuts off for up to twenty pulls - no joy. Took off the plug and it was bone dry - not a drop of fuel. Tried again with lots of pumping - no joy. I read on this forum that if it gets too hot the fuel vapourises an there is an air lock. This seems unlikely as it has worked fine for two years. OK suppose that is right, how do I get fuel to the carb? I was thinking of perhaps putting some in the cylinder and "hoping" that it might drag some liquid in but suspect that is a crazy hope. How can I tell if the pump bubble is working? There must be a way of disconnecting fuel line to carb and checking. Yours aye Chris
-
I ended up running a mile from the Isle of Man "offer" which had all the appearance of a scam and bought the 2006 one which was actual a 1998 one. It has been running well for the last two days so will spend a week clearing my brash and then play with servicing it. Thanks to all kind offers of help and advice. I am really impressed with this machine - old though it is as my previous one (a 4" Caravaggio) which I will now sell to a gardener or DIY person (it is completely useless for forestry) for leaves and branches to make compost!
-
Given the low price I got it for, I am happy to spend money on the basics as even with that money I am still quids in. As a biker who has built numerous bikes from parts (eg a Manx feather bed frame with a Villiers Starmaker 250 two stroke unique combo back in the sixties I know my basic engineering and the Kubota is fine, the wheel bearings are fine and the chassis is OK so am reasonably comfortable and, above all, the think works well - it just needs some TLC and tarting up. I am ever the optimist!
-
I bought it 3 days ago and it is pretty damn ropey as the guy that sold it to me was not very clued up - said it was a 2005 model but on checking it was May 1998! he had just looked at the 5 before the 98! and either lied or was stupid. It requires a lot of work. Talking about bearings, is this a reference to the chipper itself that drags in the timber ? I presume not the bearings of the Kubota! If so it does not seem to me too onerous to have to replace them from time to time along with changing the cutting blades every 25 hours as recommended. Anyway I am now stuck with it and the plan is to refurbish it - not sure if I need a new Anvil (how does one measure that? presumably with feeler gauges or the like?) - will need a new loom, starter switch, repair the holes in the sides, diesel cap, fan missing a blade, complete service and overhaul the hydraulics - looks like 2 to 3 days' work and several hundred quid. Flywheel seems ok but will check fins - good tip - thanks Chris
-
Dear All, Am responsible for bringing to heel about 80 acres of stored woodland of which I own about 20%. Complete newby and aim to get it managed within 5 years. Have some knowledge of timber in the lab and in buildings (www.atics.co.uk) but limited out in the woodland. Have an Avant 760i and most of the attachments needed but need a chipper that is a) suitable for the short term volume of work (I guess several hundred hours), easy to maintain, runs on diesel, has hydraulic input, can be towed or pushed to awkward locations, directional output for trailer as chips are due to be sold or used to make compost and wont break the bank. I have come to the conclusion that it is either a Timberwolf 150 HB towed to location via the Avant or a tractor OR one like this https://www.ebay.co.uk/itm/TH8-HYDRUALIC-DOUBLE-FEED-CHIPPER-FORESTRY-WOOD-PROCESSING/173020236598?hash=item2848cf4b36:g:tHUAAOSwySVaErtg from MDL https://www.mdlpowerup.com/product/th8-pto-driven-twin-roller-chipper/ The latter will of course need the tractor with the chipper and so collection of chippings would have to be by another machine. What chipper would the combined wisdom of the forum advice? More specifically, I have two TW 150s in mind - one is 2006 and going for under £3k but looks really tatty despite its low hours 600 odd The other is 2013 and has done 900 hours and looks pretty good despite its apparent suspect "provenance" from a "vendor" that does not live on the UK mainland and refuses to accept payment other than by Pay Pal (has turned down a BACS). Would you go for the older or younger one? After how many hours do these machines require serious maintenance eg major engine rebuild or chipper bearings etc ? ie say the equivalent for the average car was 100,000 miles when one should think of getting rid of it Yours Chris