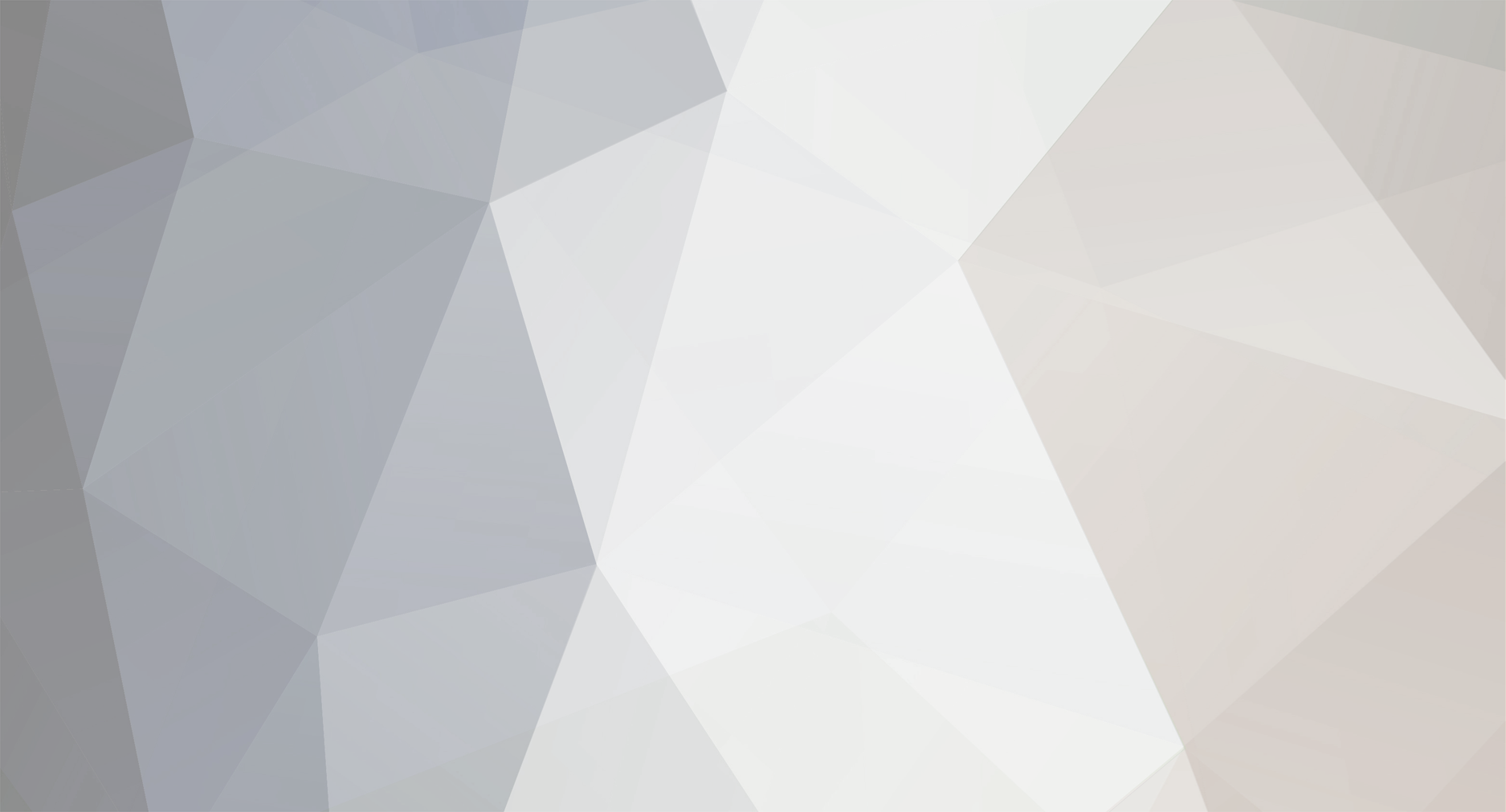
David Heaf
Member-
Posts
24 -
Joined
-
Last visited
Content Type
Profiles
Forums
Classifieds
Tip Site Directory
Blogs
Articles
News
Arborist Reviews
Arbtalk Knot Guide
Gallery
Store
Calendar
Freelancers directory
Everything posted by David Heaf
-
Domusa Bioclass NG ( https://www.youtube.com/watch?v=Uo7GCK1nv0k ) Installed 2015 Updated 2019 with HM43 burner, main circuit board & display Power output 43 kw Currently heating an 8-bedroom house It comprises two units: Hopper 5ft high, 2 ft 6 in wide, 2 ft 6 in deep Burner 4 ft 6 in high, 2 ft 2 in wide, 3 ft deep The recipient would have to remove it at their own expense. As there are isolating valves on the pipe connections, removal should be easy. Location LL52 postal district of NW Wales.
-
It is indeed! It's as powerful as the one I bought in the early 1980s, which is the one with the failed pull start. Thanks for the repair tip. I meant 'pleasant'. I misread the author name. So thanks again!
-
Thanks Dan & Chris! I followed Dan's instructions and all went smoothly (the circlip was safely in another room when the spring 'exploded'). But the spring itself turned out OK. The pulley side against the spring is sound. In short there's no obvious reason why one turn of the spring was displaced enough to impede the pulley. Anyway, I'll renew the spring when I reassemble. On the rare occasions that I return to this forum, I always find it very helpful including being able to buy a spare Sachs Dolmar 123 from a member. (It's still running well Steve!)
-
Today the pull start on my 40+ year old Sachs Dolmar 123 failed. The rope stayed out after starting but retracted due to vibration when the saw was cutting at speed. This means the spring is working. After removing the unit and testing pull/retraction I can see that the rim of the inner side of the pulley (the outermost when on the saw) is rubbing on the spring in the region of the blue arrow shown in the photo. When pulled, the rope stays out only when pulled to its full extent, but can be retracted by turning the pulley manually. A coil of the spring appears to be dislocated. I've so far hesitated to dismantle further because the spring can 'explode'. Has anyone here got any diagnostic suggestions. I've ordered a replacement spring (# 123 163 010) in case the spring is the cause.
-
Yes indeed, but thanks for checking it. Getting a new needle roller bearing for it was not easy. The Makita replacement part has a plastic cage, whereas the original Sachs Dolmar's was steel. In the end I found one with a steel cage at a bearing specialist in Germany.
-
That would be useful information to have, but please do not dismantle your saw specially to measure it! The original drum, which a 16372X Oregon rim sprocket drum replaces, is 74.23 mm outside diameter, 69.24mm inside diameter, centre hole 17.93mm, depth of drum near outer edge 20.37mm, overall depth of unit including spur sprocket 30.29mm.
-
My enquiries in 2017 to 10 possible suppliers of this part all resulted in them saying it was no longer available or obsolete. Just now, typing in '16372X Oregon' on Ebay yielded two new ones in the USA, one of then costing less than £30 with postage. It may be worth enquiring to Makita/Dolmar dealers in Germany. Thay may even have the original spur clutch drum marked as 113 223 091 on my Sachs Dolmar 123 parts diagram. Not sure what the Makita part number is for his.
-
Thanks to all for very helpful suggestions! Yes, it was a case of the Oregon chain being harder than the new Oregon 7/32" file I am using. I suspected work hardening was the problem. The last ~90 min session yesterday on a 24" ash trunk may have caused it. It was not the sharpest of chains before that session, although I'd given each tooth two or three strokes of the file beforehand. As it is a 52-teeth chain and they are still 5.5-6mm long I was reluctant to follow the 'throw it' advice. So, mindful of the work hardening possibility, I ground the hard teeth with a Lidl 'Florabest' chain sharpener. (I'm a bit skeptical as to whether that device gets the angles right, even when set up correctly. For example, my saw (Sachs Dolmar 123) manual says the leading edge if the tooth should be at 85 degrees to the bar.) To avoid the risk of overheating the teeth, I ground each one slowly, taking off only a small amount of metal. The result is that the file bites again, and I was able to finish filing the teeth to the recommended 30 degrees angle with a 10 degrees tilt of the file relative to the horizontal.
-
If this is the right place to ask: my chain sharpening question is how to deal with sharpening when a brand new 7/32" file set in an Oregon file holder and used at the correct angles on the correct sized chain/teeth will not bite into the metal of the teeth. The file skids over the metal and gets blunted (reflects light from the tips of its 'blades'). Sharpening chainsaw teeth with a file has worked these past 39 years, so what's gone wrong? Could the teeth become so work hardened that the fille won't penetrate them?
-
Oregon depth gauge not as marked 0.025" (0.63mm)
David Heaf replied to David Heaf's topic in Chainsaws
So there's a case for grinding a commercially available depth gauge tool to the correct 0.63 mm depth. I've been using the Dolmar one that is rated 0.63mm but is 0.40 mm actual, for 37 years and had no cause to complain. The saw is 70cc so would no doubt cope with the proper depth of cut. -
I have two depth gauges marked 0.025" (0.63mm), one an Oregon (part no 21830) and the other a Dolmar (complete with bar slot cleaner hook). Neither are noticeably worn. I noticed that more of the chain's depth gauge (raker) projects with the Oregon one. So it set me measuring them with digital calipers and a straight edge. The Oregon one was 0.45 mm and the Dolmar 0.40 mm. So neither of them were the stated 0.63 mm and thus result in a shallower depth of cut. Has anyone else looked into this issue? Does a loss of at least 0.18 mm in cutting depth make much difference? Does anyone check their depth gauges to verify whether they are as stated?
-
I use my Sachs Dolmar 123 routinely and have been very pleased with it these past 37 years. The second one I bought three years ago as a backup from 'spudulike' on this forum runs well too. The only snag with the 123s is the 8.5 kg with bar. I've just bought a Sachs Dolmar 100 weighing ~4.5 kg for lighter work.
-
I read somewhere that it means there is no needle roller bearing supplied with it. Do you know where at the moment in the UK I can get this part (Oregon clutch drum 16372X for rim sprockets to fit a Sachs Dolmar 123)? The last compatible part I got came from a Makita dealer as part number 957223123, but they say it is no longer available.
-
I considered using veg oil but was concerned that it may form deposits in the oil tank, pump or oilways when the saw is left unused for several months at a time. Do you have any issues like that? Also, I read that the biodegradeable oils such as the the one Bosch sells for their AKE range of electric saws, and which seems not to come cheaper than £9 a litre, have stabilisers and anti fling additives.
-
Best log splitter for around the £400-£500 mark?
David Heaf replied to Devs's topic in Firewood forum
Though the person in question has a tractor ideal for the job, he's hopeless at changing over equipment. A mower is attached most of the time. So it would have to be a stand alone splitter. There is a single phase power supply to hand, but petrol/diesel would also be acceptable. -
Best log splitter for around the £400-£500 mark?
David Heaf replied to Devs's topic in Firewood forum
Can anyone suggest a splitter that will split oak, ash, sycamore logs up to 3 feet diameter and 8-12" thick, and yet allow the log to be placed in the splitter without breaking a person's back? The person I'm enquiring for is about 80 years old and is finding that he cannot split with his maul and wedges as easily as he used to. This would be for private use, and I imagine that about £1500 would be the upper price limit. -
chainsaw clutch drum needle roller lubrication?
David Heaf replied to David Heaf's topic in Chainsaws
Ah, but they probably already know that finding spares for an antique Sachs Dolmar is getting harder and harder. As Makita supplies only plastic cage needle roller bearings, I eventually sourced a metal cage one that fits (NTN Needle Roller Bearings (Japan)) from the stockist in Germany mentioned in my earlier post. -
chainsaw clutch drum needle roller lubrication?
David Heaf replied to David Heaf's topic in Chainsaws
I'm the grateful recipient of this clean machine. Many thanks! -
chainsaw clutch drum needle roller lubrication?
David Heaf replied to David Heaf's topic in Chainsaws
The odd thing is that for 30 years I was unaware that the needle roller bearing of my Sachs Dolmar 123 needed greasing at all. I never had it fail until a couple of years ago. Since then I've got through several plastic cage replacements that Makita now stock and one authentic part with a metal cage that a chainsaw specialist in Germany just happened to have in stock. There is clearly something fundamental wrong. Today, using a lower chain tension than I've been using for the past few years, I cut for a few hours a sycamore that was wider than my 23" bar. The bearing did not seize but has clearly shed most of the grease I gave it. Also towards the end of the session the chain was inclined to run on tickover, a somewhat hazardous condition. Thanks. I'll implement this. Until I've diagnosed the problem, I'm inclined to clean and regrease the bearing after each work session. -
chainsaw clutch drum needle roller lubrication?
David Heaf replied to David Heaf's topic in Chainsaws
Thanks for this input. The clutch drum was indeed worn, so I fitted a new one that I obtained from the USA, only this time with a rim sprocket. I cleaned the shoes and gave them a light rub with emery paper. I also managed to source a metal cage needle roller bearing (K15X18X14 from Kugellager Handloser, Germany, who have an ebay.de shop) for the clutch drum. However, the bearing is still seizing after a few hours of use, despite taking great care in avoiding stalling the chain. The clutch shoes for a Sachs Dolmar 123 seem harder to source. Does anyone here know what the clearance between clutch and drum should be on a chainsaw when new? Another factor may be chain tension. I could have been over-tightening it. The over tightening could be causing clutch slip before full revs are reached. One feature of the design of the clutch freewheel that seems less than ideal to me is that any lubricant introduced into the needle roller bearing must be flung out at each end during running. On the inner end it must end up on the clutch drum, thus increasing the risk of slippage of the clutch. In any case, needle roller bearings that have seized are always completely devoid of lubricant. -
chainsaw clutch drum needle roller lubrication?
David Heaf replied to David Heaf's topic in Chainsaws
Wow, thanks everyone for your help! I'd not considered the drum being glazed. Presumably it's OK to roughen it with emery paper? The clutch is metal-on-metal, i.e. the shoes are just metal. I checked for drum wear. It does have a slight ridge on the crankcase side. Measuring the inside of the drum beyond the ridge, i.e. where it contacts the shoes, it is 70.5 mm diameter. The shoe unit is 68.6 mm diameter. I have no measurements from when new. So the clearance all round is 0.85 mm when stationary. Would this indicate significant wear? The manual says: 'When replacing the clutch drum renew the high melting point grease in the needle bearing...' Can anyone recommend a suitable grease? The spur sprocket now has more than the 8 thou (0.2 mm) wear recommended in the manual, so I'm looking for a replacement first of all in the UK. As the saw is obsolete, an exact replacement is unlikely, so I am trying to find a clutch drum, rim sprocket and spacing washer assembly. A more recent Dolmar parts diagram shows this assembly as items 36, 37 and 38 (image appended below). There is a photo and Dolmar part numbers at Dolmar or substitute chainsaw clutch parts sought. Can anyone point me to where I can get this? On another thread, someone suggested to Arbtalk member wayne 4098 that an Oregon Powermate 16372x rim sprocket drum fits. I've spent several hours trying to locate such a part in the UK, so far without success. Some leads would be much appreciated. . . . and if anyone is thinking of scrapping a Sachs Dolmar 123 I'd be interested in talking to you. -
My Sachs Dolmar 123 clutch is slipping occasionally while sawing old oak about as wide as the 24 inch bar. The assembly is shown in the diagram attached. History: the needle roller siezed last year after 31 years use. It had a metal cage/keeper. I put in a new one from Makita. It had a plastic cage/keeper. I generously lubricated it with sprocket nose grease. It failed this year apparently due to overheating. I noticed that the chain was more prone to stall under full power, i.e. motor still running. On dismantling, I noticed that the bearing was completely dry, but there were traces of decomposed grease on the clutch shoes and drum. There is apparently no component that stops grease being flung from the needle roller bearing into the clutch drum. My question is: should the needle bearing be lubricated and if so, with what and by how much?
-
If you have not found the instructions yet, I have the original instruction manual for my Sachs Dolmar 123 which I bought in 1980. I could scan in the 19 pages and email them to you if you wish. Have you had any luck getting parts? If so, please could you let me know the sources. I'm looking for a clutch drum with an 8-tooth sprocket.