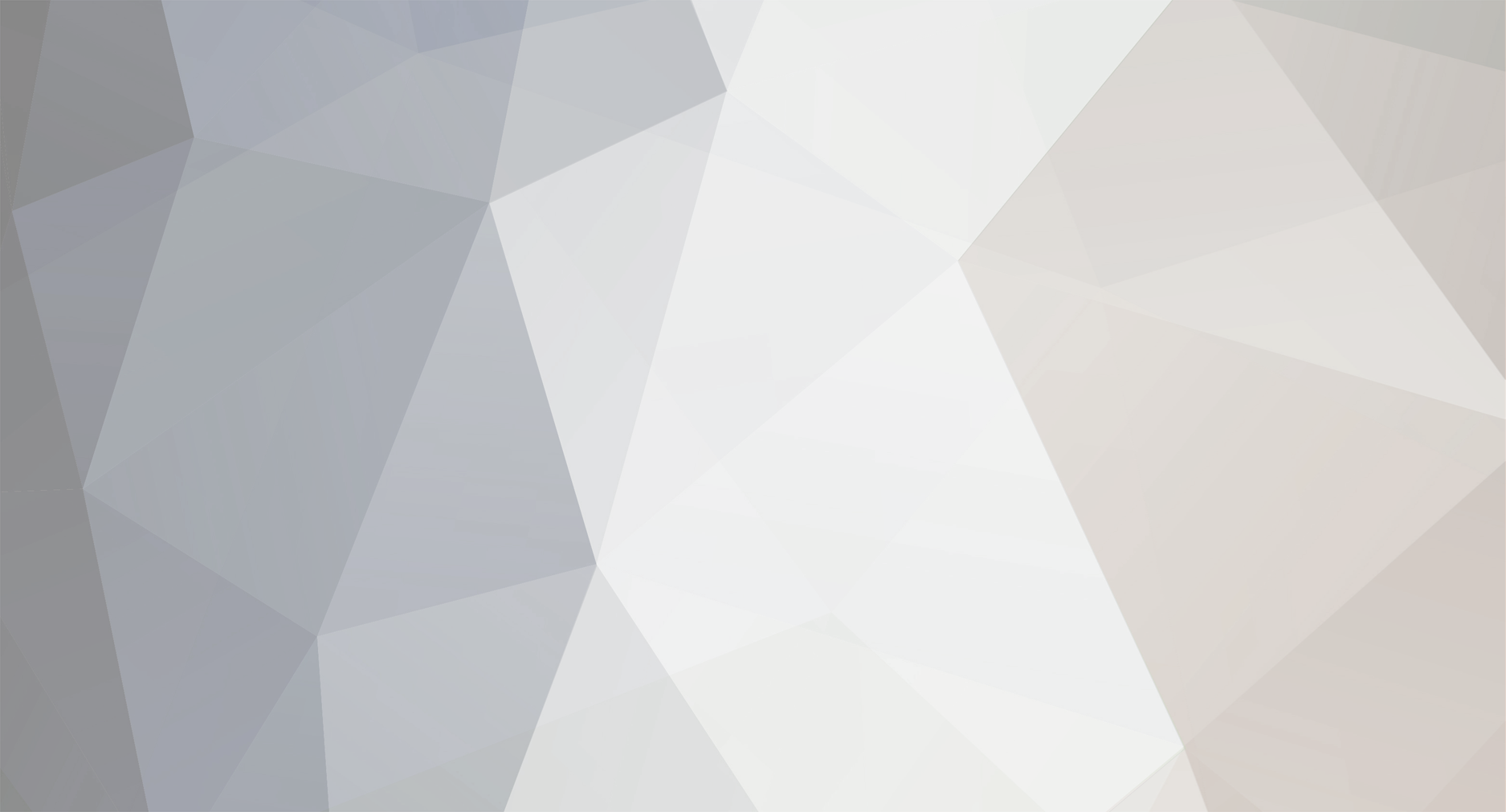
cjdg
-
Posts
51 -
Joined
-
Last visited
Content Type
Profiles
Forums
Classifieds
Tip Site Directory
Blogs
Articles
News
Arborist Reviews
Arbtalk Knot Guide
Gallery
Store
Freelancers directory
Posts posted by cjdg
-
-
Just had the chains referred to in a previous post repaired by a garden machinery specialist. the obvious to bent links have been fixed but the chap could not find the other defective ones despite my fixing tape on the links that were sticking in the bar round the sprocket Paid for them to be professionally sharpened Went back to put in the bar (now cleaned as advised on this forum) and Lo and Behold! still sticking. Aaaargh Took advice from a pro tree surgeon locally and he said when that happens to him he simply puts the chain in the saw and runs it hard to get it to fix itself !
There is a certain logic in this as the link has no VISIBLE bend or dink
It may be that there is a machine that can measure this but for sure the operator will have to have good glasses!
Any comments on what to do?
-
I must have been a muppet on dealing with a particularly large 5 stemmed sycamore and bent the bar which, unsurprisingly, now wanders on the cut. When I first measured the deformation it was about 2.5 mm and by judicious use of boot and a flat surface I have reduced this to "almost" straight BUT I am somewhat concerned as to how to get it fully straight and not overdo it and bend it the other way! To exceed Young's modulus by just the right amount I am thinking of using two plates of steel at each end about 2mm thick and pressing down on the centre with about 100 mm wide load eg a 4 x 2" timber and a lump hammer and see if that works. If not go up in 1 mm increments until it does
Is there a professional way to do this in a better precision engineered way? Who would provide such a service? I am near Oxford
See also the other post on sticky links
9C45F9A6-1BDB-409B-A945-8C894FFA4339.heic 5A596F21-F4AA-47D9-B968-16720F3DB433.heic 6948D16D-3A36-4D3D-94FB-2416454408BB.heic
-
Thanks all. I will stick with my eye and a flat file
Chris
-
My mentor told me how to get the burrs off the sides of the chain bar with a flat file. He also showed how o level out the two sides at 90 degrees. I see on the many videos of maintaining a worn chainsaw bar that a tool is recommended. See the image below.
Question 1
Is this what professionals use? I have never seen the three guys I know use one.
Question 2
If so what is recommended model or make? Stihl, Husqi etc whack them out at over £30 but the one below is under £10
Seems a no brainer to go cheaper IF (and I suspect it is not) recommended by the professionals
Chris
-
-
The saga continues.... Got the new switch and fitted it BUT although the key operates the ignition LIGHTS
turning it to the right to get the starter motor to turn does not work The supposed diagram supplied by the supplier of the switch has different colours to the colours on the actual switch The earth and the power are black and orange that is pretty clear The other three colours on the machine itsefl are respectively
Red / Grey (sort of grey)
Purple which the diagram says goes to the ignition cut out switch and a component I cannot fathom on the diagram
Orange/green/blue
The diagram has Blue / red and
Red
The actual wiring is on the photo and I have downloaded the diagram as a pdf.
not sure if it will work!
1 - K C A (91-02).pdf1 - K C A 1 - K C A (91-02).pdf(91-02).pdfam
So my question(s)
Assuming the orange and black are right What are the other colours?
What colour is equivalent to the missing colours
or was the replacement switch the wrong one?
It was sent on the recommendation of a Countax expert
Chris
-
The chain came off within the saw because I had not put it on properly and as it fell apart it hit the saw. It pains me to admit this but as George Washinton said.....
-
1
-
-
I have managed to mildly mis align three of these and take out a complete half axle on four Oregons that still have lots of life
Anyone able to recommend a local chainsaw doctor (or indeed forester) in the Oxford area I am told that local Garden centres provide this service but I am somewhat wary of such chaps having twice been mislead by the so called engineers I find at such places
I am in OX1
Yours
Chris George
-
Dear Member L
I am intrigued by you making up chains... I am a late coming amateur old git Took up chainsawing when I bought some woodland well north of age of 65 but a reasonably competent motorbike engineer. I have managed to mangle four chains. Three of them have no easily visible defect but when you put them on the bar they stick round the sprocket and it appears that one of the links is slightly bent The fourth one has an obvious half in half out central axle where one end has popped half out of the link. On a push bike (I do a lot of that) you get a chain link tool that pushes out the axle on the link and shorten the chain or put in a link. Question. Is there a service available for repairs of such defects in chains or a tool for DIY or is this simply too dangerous ?
Chris George
-
-
ANSWER found
The key replacement console - although looking identical - actually was a different wiring set up and so was dead as a do do It was found by (again) double checking with the old key console after charging up the battery. Now to find out which wire goes to which part of the new switch. Any countax experts out there with a clue as to how I find the right colours for the new switch? Thanks to those who put in answers
-
1
-
-
I will try the battery terminals Never thought of that
Its obvious but they "look" good and are a robust clip on mechanism. However I will do that right now!
-
Yes to the sensor seat. I tested that by shorting out the connections See photo with blue wire
-
Tried to change the key starter lock mechanism today and shorted very briefly (small spark) as I fed the new lock into its hole. Went to start it and - nothing! dead as a Dodo. Assumed it was a fuse but on checking, it was not. Double checked the three fuses with a mulitmeter. All sound. Triple checked by putting in new ones. All dead. Checked the earth from the battery. OK. Checked the seat cut out switch (which should not affect the ignition lights - only the running of the engine. No ignition lights. Just to be sure put a wire across the two connectors. Still dead. Went to lunch to think. Still dead. It was working with the old switch (with a screw driver as lock was effed) and put that back in Still dead. Battery has 12.65 volts and is fine and fully charged. Checked with the manual and diagram for wiring to see if there is a hidden fuse somewhere else in the system. Cannot see that. Took the top off the fuse console to get direct access to the female fuse connectors and cleaned them up a bit and put in new fuses - still dead.
Thoughts.... is there a hidden fuse? Unlikely...
There must be something very simple that I am missing...
Now pretty desperate as my tiny brain is hurting and its sunny and the lawn is telling me I want to be cut!
Chris George
CA966F2A-78AF-425A-85B9-9D03E6A10428.heic 7175BC2D-E57E-4063-AD9C-459B761F71E2.heic
-
Dear Anyone
I have spent quite a lot of time on refurbishing this machine over the last 8 years and inter alia have replaced the fans (big cast ali ones), tapped and die some of the fixings the block. I "think" it might benefit from a new block but that is just a guess. I am looking for someone within fighting range of Oxford who has a small business with low overheads (and hence not too expensive) who can go through this machine and do the following which is a bit of a guess
I suspect it may need
a) a replacement block and rollers (I have drilled and re tapped the studs a couple of times) but you MIGHT be able to drill and re-tap with a slightly larger diameter stud
b) total service of engine and all other parts
c) check and, maybe, a new wiring harness or repair where needed with good insulation and connections
d) repair and re-weld the safety bar (it does not comply with current legal requirements but "sod that" - it works)
e) sharpen the cutting blades
f) tidy up the shoot lever angle adjustment mechanism
g) check wheel bearing etc etc and replace if needed
f) clean out fuel tank and fuel lines and refill with clean diesel
g) new diesel glow plugs if needed
What I have done in the past
Purchased a service pack of spare parts and carried out a service including the following:
1) Jet washed all oiled chippings, grease and other contaminants from engine and chassis
2) warm up and remove existing engine oil, safely contained and disposed at local refuse centre
3) drained down fuel, loosen and clean out water contaminant from fuel tank by loosening off chassis and jacking up tank fully to drain
4) new oil
5) change filters for fuel and oil
6) remove and replace electrical wiring clips to ignition switch
7) attempted to drill out one of two defective bolts broken off in place holding on wiring front plate. This failed and still needs to be done for both
😎 removed and cleaned out using tap and die the thread of the arm cramp securing the dolly wheel
9) repaired the clamp for the rear stand using 8mm bolt supplied by others
10) Install two new chipper blades
11) Test run engine
12) Adjust three drive belts’ tension
13) Lubricate grease nipples of chassis tow bar
14) Supply new fuel cap and lock
Work carried out on 3rd and 4th October 2016 with part time assistance.
PARTS
Chipper Service and Fuel Cap - £61.80
Chipper Blades - £89.40
1) Investigation of fault with infeed rollers intermittently stopping
- Found loose relay causing the fault
- Secured relay in place with zip tie
Work carried out on 10th October 2018
I have done the following similar work to this was all done in March 2019 Complete new fan and assembly and bearings
https://arbtalk.co.uk/forums/topic/9965-timberwolf-fins-and-flywheel-bearings/
Did a replacement of those silly cast Ali fans
=======
23rd and 24th March 2021 – 7 Hours
Remove Feed Roller and remove blades and sharpen, replace onto new roller and fit assembly.
Remove and fit new starter motor.
Remove battery and charge.
Collect new solenoid valve.
Remove Feed in/out solenoid and valve and replace with new one.
Tested all good.
PARTS £150
I may be that someone out there is interested and if so let me know otherwise I will go to Mr Scot (with whom I spoke today and was most helpful in suggesting a possible part exchange)
Over to you guys!
Chris George
-
I have two of these machines one mark 1 one mark 2 (I think!), lets call them A and B. My "regular" one A has been good as gold until a month ago. It was always a bit of a b^&&£r to start but then it went dead. Checked the plug sparking by taking out plug of A and turning over. No spark. Put the plug out of B which worked and checked that in A. No spark . Took the plug out of B which worked in B and swapped over the plug to A No Spark. Checked therefore both plugs in B and there is nothing wrong with the plugs. So it must be the generation of the spark Now I am an old old git close to 80 and I was brought up on motorbikes with. contact breakers and magnetos etc etc so I do not have a clue as to what generates the spark but suspect it is some form of electronic chip/package that you screw in and out. Where do I start looking for a solution?
-
See photo 1 of the "bend" in shaft of JW(Went over a traffic bump that was in my own drive way that is a bit to abrupt and it dropped out and bent on the next bump!) I know idiot thing to do.See photo 2 of split pin having HAD to be drilled out as it would not knock outIt is now 7 mm in diameter and I am not sure if that is more than the original but suspect it isI am unsure as to how to take the wheel handle off the top of the shaft as it is not rotating "clear of the wheel" (ie still linked) even after the removal of the split pinI conclude that, therefore, there is a flat to the threaded rod as well as a split pin as in screen grab (No 4 below) from an on-line Aussie videoPhoto 3 non circular receptor handle of another make of jockey wheelPhoto 4 non circular threaded rod of another make of jockey wheelQUESTIONS1) Given that the wheel cannot come off at the bottom due to there being no means of disassembly, am I right in thinking that the only way to get this off is to draw the threaded rod upwards out of the base of the wheel?2) Is there a similar flat in the threaded rod on the Ifor Williams JW as shown in Ptoto 4 above?3) If not, is it a matter of forcing the handle upwards now that the split pin has been removed? I suspect not as I have been fairly hard with a club hammer trying to knock it off from both sides.4) Even if I do. manage to get it off it still will not be removable from the trailer unless I cut off and re weld the lower receptor for the anti spin spring connector which "seems" a rather drastic and, I hope, unnecessary procedure5) Am I right in thinking that IF IT WAS NOT BENT one could simply unwind the whole top section out with handle on the top?6) If so, what is the purpose of the split pin ?7) If so, and the ONLY way to disassemble this is by unscrewing the bent threaded rod by force would it not be best to try to bend at least some of the bend out of both threaded rod inside and the outer casing ?8) It would need considerable force carefully applied with a jig and suitable strong crampsWhat do any of you experts advise?
-
Latest on this project. Flywheel off by removing the collet which cunningly had only two grub allen screws with the third non threaded hole being used to push out the collet. I remember now why I put two white lines on the used ones - Doh! Opened up casing to find it well out of shape and cracked. The option to take out the engine to get at the frame was considered for all of a micro second before being discarded. Will cut out bent parts and weld replacement in situ with a complete new "inner" liner of say 5mm steel also welded in on the bottom 30 degree segment and along up to the top of the chute.
A replacement roller box is well north of £1000 so it looks like some clever reaming and oversize threaded rod to get welded back in but there is not much room in the inside with the roller so cannot use a bolt as originally planned. That means a special two diameter threaded rod one to weld in and one to hold the pump.
Any other ideas welcome
Chris
-
I put a new fan on a complete rebuild of this machine about four years ago. It has again disintegrated!
Question(s) 1. Is the cause of this likely to be user-related by putting stones or metal instead of timber? Seems unlikely as it is not on the cutting path. If not, what has caused this after such a short time? I would not expect this to be a service replaceable part but to last the lifetime of the machine. Any comments ?
Question 2. At the same time, I noticed that the threaded studs on the bottom hydraulic motor have pulled out of the cuboidal housing of steel despite being welded in last time. Is it time to buy a new plate steel housing or (and I am inclined to favour the latter) should I drill out the steel hole, weld in a new bolt rather than threaded rod with the bolt head set inside the steel and if necessary ground down slightly should it be needed for clearance (yet to be determined)
Question 3. How do I pull out the bearing on the main frame steel plate shown in the photo with the bearing puller which only fits on two of the three sides? What am I missing here?
Question 4. If it is the case that this is normally a life time part for the machine and it is not possible to damage it by abuse, what are my chances of the supplier replacing it FOC or at cost price?
Chris
-
A relative newbie asking so be polite and patient
Sequoia IMG_8248 | Safe Tideway Rowing
ROWING.ATICS.CO.UKSee this Sequoia
The bottom section has been cut in one length about 4.5 m long and it is big and heavy.
There are two sections about 2 m long and the rest are chunks about 600 to 900 taken down in slices. I reckon they are only good for firewood unless sequoia is good for turning as some of the heartwood has a fantastic hue.
So the question is "Would it be worth bringing in a proper mobile mill and doing some cutting into thin sections or bringing in an Alaskan and DIY ? What is hewn / planked Sequoia worth?
Is it ok for furniture?
Anyone know its structural properties of it? From what I read on the internet it is much valued for both furniture and structures and is pretty difficult to get hold of.
Thoughts?
Chris G
-
It appears that around my patch Wootton (the one near Oxford) / Cumnor etc an Avant and lots of other local guys have had stuff nicked - chain saws and the like. I have lost a nice Husqui pole saw and top notch Back pack leaf blower nicked in my totally isolated area at Youlbury - never had a problem before as it is right at the end of a long private road at a dead end. Just wondering if any other areas have had a blight of such thefts? Have any of you been offered cheap tools? If so please take a photo of the licence plates of those offering unless you know they are kosher. I am now going to have to spend over 10 grand on top of the range face recognition camera set up with vehicle registration recognition software from VL office to get to grips with this low life. I normally keep my shotgun stock away from the barrel hidden elsewhere in the house on firearms officer advice - perhaps it is time to reunite them!?
-
1
-
1
-
-
Looking for a quick response to hire man and machine to take about 100 trees cut to varying lengths of max 6 m but mostly between 2 and 4.2 m Max diameter about 1.25 for the largest (very few of those) but average round about 900 mm from location to local store less than a mile away and all on private land. Day rate not a quote but have got free supply of red diesel and will provide food tea etc. Can accommodate overnight if needed. 07478 601456 or [email protected]
-
1
-
-
Pryor & Rickett Silviculture
-
Sorry to hijack a forum post but I am in need of finding Adam Todd. Anyone know if is is well and functioning as he is not answering his phone.
longest bar and type of chain for Husqui 550 XP
in Chainsaws
Posted
What is the longest bar that 550 XP "sensibly" can use? I have 16” and 18” bars for my 3No XP550s already and wondered if I could get away with a longer one