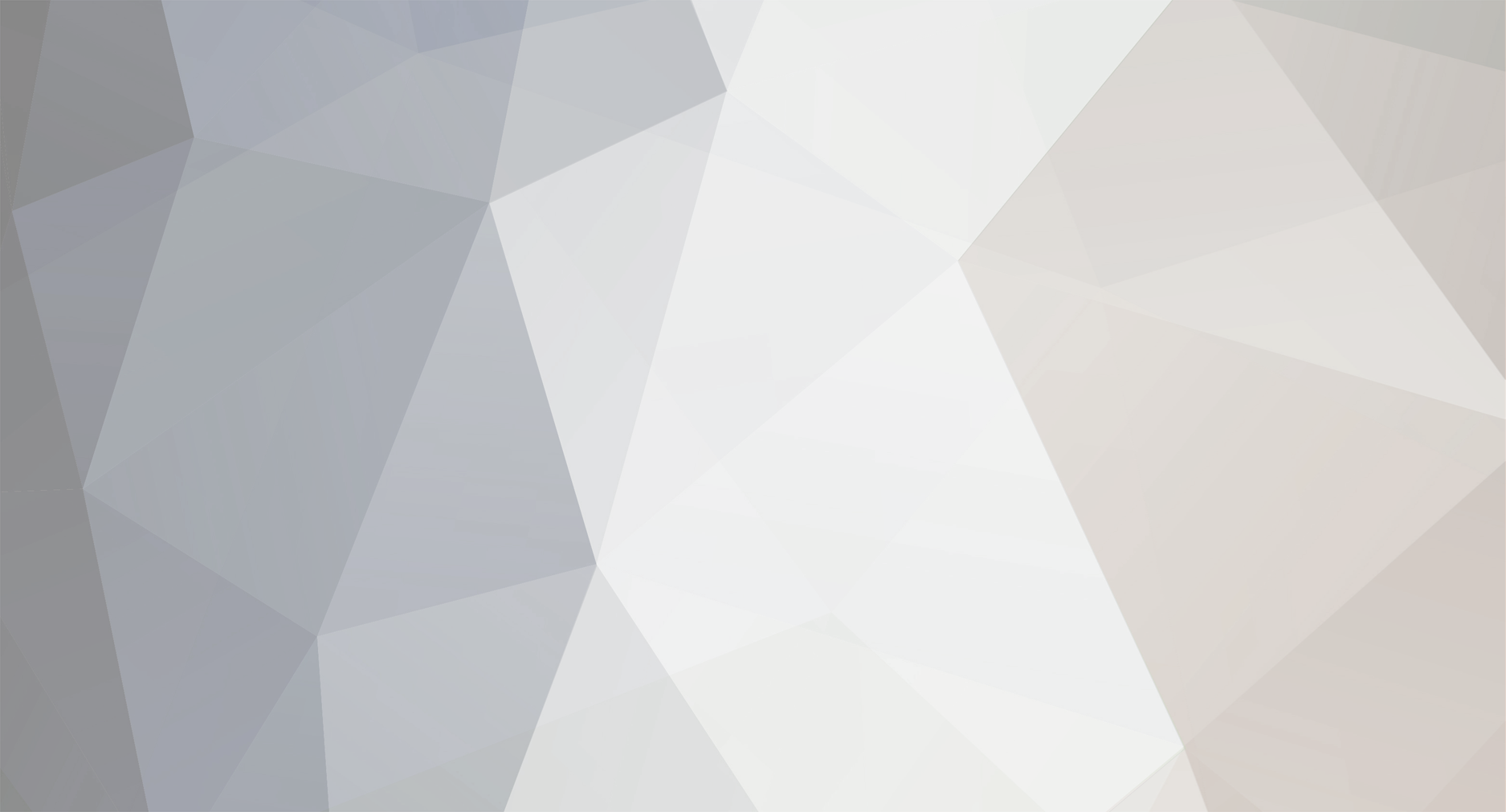
cjdg
Member-
Posts
51 -
Joined
-
Last visited
Recent Profile Visitors
The recent visitors block is disabled and is not being shown to other users.
cjdg's Achievements
Enthusiast (6/14)
-
Rare
-
-
-
-
Recent Badges
-
What is the longest bar that 550 XP "sensibly" can use? I have 16” and 18” bars for my 3No XP550s already and wondered if I could get away with a longer one
-
Just had the chains referred to in a previous post repaired by a garden machinery specialist. the obvious to bent links have been fixed but the chap could not find the other defective ones despite my fixing tape on the links that were sticking in the bar round the sprocket Paid for them to be professionally sharpened Went back to put in the bar (now cleaned as advised on this forum) and Lo and Behold! still sticking. Aaaargh Took advice from a pro tree surgeon locally and he said when that happens to him he simply puts the chain in the saw and runs it hard to get it to fix itself ! There is a certain logic in this as the link has no VISIBLE bend or dink It may be that there is a machine that can measure this but for sure the operator will have to have good glasses! Any comments on what to do?
-
I must have been a muppet on dealing with a particularly large 5 stemmed sycamore and bent the bar which, unsurprisingly, now wanders on the cut. When I first measured the deformation it was about 2.5 mm and by judicious use of boot and a flat surface I have reduced this to "almost" straight BUT I am somewhat concerned as to how to get it fully straight and not overdo it and bend it the other way! To exceed Young's modulus by just the right amount I am thinking of using two plates of steel at each end about 2mm thick and pressing down on the centre with about 100 mm wide load eg a 4 x 2" timber and a lump hammer and see if that works. If not go up in 1 mm increments until it does Is there a professional way to do this in a better precision engineered way? Who would provide such a service? I am near Oxford See also the other post on sticky links 9C45F9A6-1BDB-409B-A945-8C894FFA4339.heic 5A596F21-F4AA-47D9-B968-16720F3DB433.heic 6948D16D-3A36-4D3D-94FB-2416454408BB.heic
-
Thanks all. I will stick with my eye and a flat file Chris
-
My mentor told me how to get the burrs off the sides of the chain bar with a flat file. He also showed how o level out the two sides at 90 degrees. I see on the many videos of maintaining a worn chainsaw bar that a tool is recommended. See the image below. Question 1 Is this what professionals use? I have never seen the three guys I know use one. Question 2 If so what is recommended model or make? Stihl, Husqi etc whack them out at over £30 but the one below is under £10 Seems a no brainer to go cheaper IF (and I suspect it is not) recommended by the professionals Chris
-
No ignition lights or starter connection on Countrax C400 H key change
cjdg replied to cjdg's topic in Maintenance help
The saga continues.... Got the new switch and fitted it BUT although the key operates the ignition LIGHTS turning it to the right to get the starter motor to turn does not work The supposed diagram supplied by the supplier of the switch has different colours to the colours on the actual switch The earth and the power are black and orange that is pretty clear The other three colours on the machine itsefl are respectively Red / Grey (sort of grey) Purple which the diagram says goes to the ignition cut out switch and a component I cannot fathom on the diagram Orange/green/blue The diagram has Blue / red and Red The actual wiring is on the photo and I have downloaded the diagram as a pdf. not sure if it will work! 1 - K C A (91-02).pdf1 - K C A 1 - K C A (91-02).pdf(91-02).pdfam So my question(s) Assuming the orange and black are right What are the other colours? What colour is equivalent to the missing colours or was the replacement switch the wrong one? It was sent on the recommendation of a Countax expert Chris -
I have managed to mildly mis align three of these and take out a complete half axle on four Oregons that still have lots of life Anyone able to recommend a local chainsaw doctor (or indeed forester) in the Oxford area I am told that local Garden centres provide this service but I am somewhat wary of such chaps having twice been mislead by the so called engineers I find at such places I am in OX1 Yours Chris George
-
Dear Member L I am intrigued by you making up chains... I am a late coming amateur old git Took up chainsawing when I bought some woodland well north of age of 65 but a reasonably competent motorbike engineer. I have managed to mangle four chains. Three of them have no easily visible defect but when you put them on the bar they stick round the sprocket and it appears that one of the links is slightly bent The fourth one has an obvious half in half out central axle where one end has popped half out of the link. On a push bike (I do a lot of that) you get a chain link tool that pushes out the axle on the link and shorten the chain or put in a link. Question. Is there a service available for repairs of such defects in chains or a tool for DIY or is this simply too dangerous ? Chris George
-
No ignition lights or starter connection on Countrax C400 H key change
cjdg replied to cjdg's topic in Maintenance help
Thanks for all this. I have ordered a new one from a different supplier Its £45 with the postage but it has taken me a day and a night of worry and lots of head scratching. Never for a moment suspected the ignition console but on looking at the back they are different. -
No ignition lights or starter connection on Countrax C400 H key change
cjdg replied to cjdg's topic in Maintenance help
ANSWER found The key replacement console - although looking identical - actually was a different wiring set up and so was dead as a do do It was found by (again) double checking with the old key console after charging up the battery. Now to find out which wire goes to which part of the new switch. Any countax experts out there with a clue as to how I find the right colours for the new switch? Thanks to those who put in answers -
No ignition lights or starter connection on Countrax C400 H key change
cjdg replied to cjdg's topic in Maintenance help
I will try the battery terminals Never thought of that Its obvious but they "look" good and are a robust clip on mechanism. However I will do that right now! -
No ignition lights or starter connection on Countrax C400 H key change
cjdg replied to cjdg's topic in Maintenance help
Yes to the sensor seat. I tested that by shorting out the connections See photo with blue wire -
Tried to change the key starter lock mechanism today and shorted very briefly (small spark) as I fed the new lock into its hole. Went to start it and - nothing! dead as a Dodo. Assumed it was a fuse but on checking, it was not. Double checked the three fuses with a mulitmeter. All sound. Triple checked by putting in new ones. All dead. Checked the earth from the battery. OK. Checked the seat cut out switch (which should not affect the ignition lights - only the running of the engine. No ignition lights. Just to be sure put a wire across the two connectors. Still dead. Went to lunch to think. Still dead. It was working with the old switch (with a screw driver as lock was effed) and put that back in Still dead. Battery has 12.65 volts and is fine and fully charged. Checked with the manual and diagram for wiring to see if there is a hidden fuse somewhere else in the system. Cannot see that. Took the top off the fuse console to get direct access to the female fuse connectors and cleaned them up a bit and put in new fuses - still dead. Thoughts.... is there a hidden fuse? Unlikely... There must be something very simple that I am missing... Now pretty desperate as my tiny brain is hurting and its sunny and the lawn is telling me I want to be cut! Chris George CA966F2A-78AF-425A-85B9-9D03E6A10428.heic 7175BC2D-E57E-4063-AD9C-459B761F71E2.heic