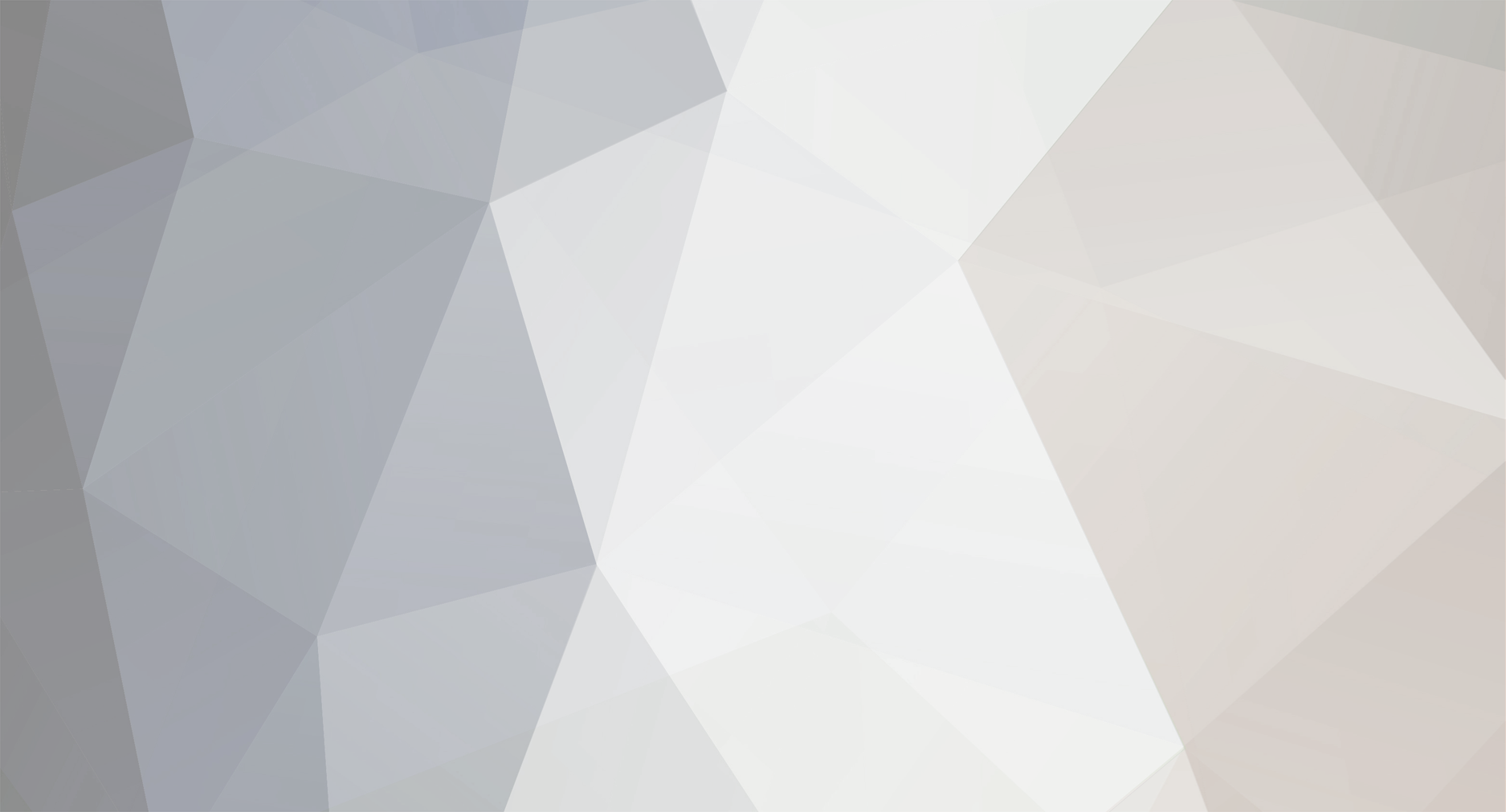
ihatesaws
Member-
Posts
52 -
Joined
-
Last visited
Content Type
Profiles
Forums
Classifieds
Tip Site Directory
Blogs
Articles
News
Arborist Reviews
Arbtalk Knot Guide
Gallery
Store
Freelancers directory
Everything posted by ihatesaws
-
I got the saw idling okay again but after doing a few hours of cutting I think the oiling problem is still there. The bar is getting very hot, makes a sound, looks dry and oil consumption is low. When I take the chain off I always find some mushy crud in the bar groove which I remove. Without the bar there is a good flow of oil out the hole on the saw. Could bar/chain wear be the problem. I can push the cutters from side to side on the bar. They could well be worn. The chain wouldn't pull the oil along the bar so a mass of oil and sawdust builds up in the groove which blocks further oil coming out of the saw???
-
I got a new sprocket from china with a new bearing. I had the whole saw apart again due to an air leak where the top and bottom go together and I saw that there is a screw on the oil pump to increase the flow of oil.You can actually turn it through a hole from underneath the saw without taking anything apart. The oiling might be the best thing working now on the saw as after putting it back together I'm having trouble getting it to idle consistently without adjusting the screws. The revs at idle just keep dropping till it dies. I pressure and vacuum tested it twice after putting it back together and it passes so I guess it must be the screws. I'll look at it again. I have a question about the ignition coil. I had to reset the gap when I put the flywheel back on and one of the two screws keeps rotating and doesnt get fully tight. Is it screwing into metal underneath the coil? I used loctite 243 once before but when I loosened it again it didnt feel like it had been locked tight. Btw do you use loctite on the four cylinder screws?
-
I am a farmer!!!!!! Thanks to all. I might try thinning the oil a bit.
-
I won't be using the saw enough to replace the sprocket regularly so I'm not going to get a conversion kit. The one on it is probably the original one. What are the consequences of continuing to use a worn sprocket? If I replace with an aftermarket one will it just wear more quickly than oem or could it damage other parts of saw? As regards oiling I did write that I cleaned out the bar groove and the inlet hole on the bar so that can't be it. Is it the case with every saw that the oil tank empties at the same rate as the fuel tank? Is there a vent in the oil tank to prevent a vacuum and if so where?
-
Hi do I need a new sprocket? Is an aftermarket one for £5 from China okay or do I need an oem one for £20? Had arbor biooil or some such stuff in the saw and it clogged it up. After doing a bit of cutting the chain wouldn't move anymore. I cleaned all of the gunk out and even put in a new worm gear although I think the old one wasn't too bad. When I run the saw and take off the bar the new oil trickles out and down the saw but when the bar is on the flow seems to be slow. I don't see a great amount of oil in the groove on the bar and when I go through a tank of petrol then maybe only 1/4 or 1/3 of the oil tank has been used. I thought they should both empty at the same rate. Since I cleaned the whole thing out the chain doesn't seize anymore but it does look a bit dry and feel hot. Is this model of saw a poor oiler? I don't see what could be stopping the oil flowing in the bar as i cleaned out the groove and the small inlet hole thoroughly. Does the oil pump wear out and not pump as strongly with time? Thanks
-
It is worse than ever. Very erratic idle and doesn't stay going for long. Just to make matters worse the starter recoil stopped working a few weeks ago. It wouldn't pull back in the rope. I was using the starter from the 024S on both saws and now that is pulling in the rope extremely slowly. Thanks for your help, spud. I give up. I hate saws.
-
It is worse than ever. Very erratic idle and doesn't stay going for long. Just to make matters worse the starter recoil stopped working a few weeks ago. It wouldn't pull back in the rope. I was using the starter from the 024S on both saws and now that is pulling in the rope extremely slowly. Thanks for your help, spud. I give up. I hate saws.
-
I got the pick set a couple of weeks ago. Manufactured from chrome vanadium steel for strength, so said the product description. Each one of them bent straight away. A neighbour gave me a piece of really hard steel today from a hay turner. It has a 90 deg bend at the end. I stuck it into the seal, put my two feet on the saw and pulled the shaft up with a vise grips as hard as I could but the seal wouldn't budge. I put another vise grips on opposite and got another guy to pull up on that one and after a few goes it finally popped out. I put the new seals in. Hopefully they are at the correct depth. The clutch side didn't go in quite right. The socket pushed on the outer metal ring only so there was no pressure on the inner rubber lip which in part didn't go down smoothly where the crankshaft widens. I hit it with a smaller socket and that helped it be more uniform but it isn't perfect. Prodding it with a screwdriver didn't seem to help. I don't want to hammer it any more incase the seal goes too deep. I did a vac test while rotating the crankshaft and it seems not to leak. Tomorrow I will finish putting the saw back together and give it a test. If it is still the same way I'll go crazy. I vac tested the 024S a couple of weeks ago again and I couldn't see any leaks but maybe the seals only leak when the saw is running and haven't deteriorated yet to the point where I can pick the leak up with the test. If the 024 is now fixed I will probably replace the seals on the super.
-
I got the pick set a couple of weeks ago. Manufactured from chrome vanadium steel for strength, so said the product description. Each one of them bent straight away. A neighbour gave me a piece of really hard steel today from a hay turner. It has a 90 deg bend at the end. I stuck it into the seal, put my two feet on the saw and pulled the shaft up with a vise grips as hard as I could but the seal wouldn't budge. I put another vise grips on opposite and got another guy to pull up on that one and after a few goes it finally popped out. I put the new seals in. Hopefully they are at the correct depth. The clutch side didn't go in quite right. The socket pushed on the outer metal ring only so there was no pressure on the inner rubber lip which in part didn't go down smoothly where the crankshaft widens. I hit it with a smaller socket and that helped it be more uniform but it isn't perfect. Prodding it with a screwdriver didn't seem to help. I don't want to hammer it any more incase the seal goes too deep. I did a vac test while rotating the crankshaft and it seems not to leak. Tomorrow I will finish putting the saw back together and give it a test. If it is still the same way I'll go crazy. I vac tested the 024S a couple of weeks ago again and I couldn't see any leaks but maybe the seals only leak when the saw is running and haven't deteriorated yet to the point where I can pick the leak up with the test. If the 024 is now fixed I will probably replace the seals on the super.
-
I wasn't able to get the seal out. Maybe you would like to taunt me with yet another photo of the pullers? I was already beginning to scrape the edge of the crater in which the seal sits with what I was using to try and lever it out. I was only going to cause more damage so I gave up. I am waiting for a hook and pick set like this one before trying again: http://www.mxsouth.com/bikemaster/bikemaster-other-tools-tool-packs-wraps-4-peice-mini-hook-and-pick-set_1.jpg I read about one guy hitting a kind of bushing down around the exterior of the seal crushing it inwards so it could be pulled out. I would be afraid of driving the seal further inwards and of scratching the crankcase but I suppose it is not as important to not damage the case as the crankshaft as the new seal will be static against the case and any scratches between them will be sealed with the hylomar applied to the outer diameter of the seal before insertion. I suppose I shouldn't hammer a screwdriver down between the case and the seal though
-
I was able to get the clutch side seal out easily enough with something i made to resemble a paint can opener but the the flywheel side has me stumped. It is too small to fit the tool in I used on the other side and any smaller version I make is too weak as the metal is so thin itjust bends when I pull. I've been trying with an awl I made out of a screwdriver. At this stage the rubber near the crankshaft is in bits with all the puncture holes. I am able to get the awl in under the metal part of the seal in a few places but even if I pul upwards with all my might the seal won't budge. The metal part is stuck to the crankcase. I've sprayed wd40 in to try and loosen it up but no effect so far. I'm reluctant to try and squeeze something down between crankcase and seal as I would be scratching the case. Is there some kind of stuff that would be good for disolving whatever sealant is between the case and the seal? I've been reading elsewhere on the internet that this particular seal was the one that convinced them to buy pullers.
-
I put oil first on the flywheel side and instead of the vacuum going from 0.5 to 0.4 bar it went to around 0.45. I then turned it over and put the oil on the clutch side and brought the pump back to 0.5 bar. After 15 seconds of turning it didn't drop. Then I kept on turning and after a bit I could hear the oil being sucked in and the gauge needle dropped dramatically. When I bought the new carburetor I remember reading their recommendation to replace the crank seals as well in order to be able to adjust the saw correctly. I bought them at the time but the old seals seemed to pass the pressure/vac test and it seemed an awful ordeal to replace them. I don't have expensive pullers. Does this mean I am going to be drilling holes and sticking in screws so I can pull them out or am I going to put the crankcase in the oven so it expands allowing the seals to be easily removed? At least we seem to be getting somewhere at last (apart from the asylum).
-
If by any chance there are others out there crazy enough to want to take apart (or more importantly put back together) the stihl 024/026 there is an eight part series here on how to do it: TheInfoworks's channel - YouTube It is only a shame I found it today. It would have been really useful for me starting out. I suppose an even more useful video though would be how to do the ms290
-
Great stuff, Spud. You keep giving me hope. We'll win in the end! >>all I will be doing is what I have described here in this thread! Yeah but you'd be doing it right. I'll give that vac test a go again. I just remembered that when I replaced the cylinder and gasket I had no hylomar at the time (nor did I know I needed it) so there is none between the gasket and the metal. I will lift the cylinder up as high as I can without the rings springing out and spread some on.
-
I took the HD-19B carburetor off the ms290 (one of your favourite saws) and sealed up both ends and stuck it in a bucket of water. It leakes like a sieve out of the throttle and choke shafts so I believe you now that it is not an issue. I guess constant air leaks are not a problem. You just tune the carburetor to compensate for them. >>do either of your 024 Stihls work fine with any of the carbs you have? I suppose it depends on how you define fine. They do afterall cut pretty well and idle to a certain extent at times. If by fine you mean consistent behaviour at idle then I would have to say no. I took the clutch and the oil pump off and poured water on the seal while the 024 was running. No sign of any bubbles. I sprayed carburetor cleaner down on where the cylinder meets the crankcase but couldn't see any change in rpm. I was thinking that maybe there were airleaks only when the saw was running and got hot but I couldn't test anymore areas with it running. I took off the flywheel for the first time (hurray!) and pressure tested the saw. I pulled and pushed on the crankshaft on both sides of the saw but no drop in pressure. I rotated the crankshaft constantly but no drop in pressure and no bubbles. It definitely isn't loose. I then did the vacuum test. If you wait a few minutes you can see a tiny drop but it is only when you rotate the crankshaft constantly that the vacuum goes from 0.5bar to 0.4bar in 10 or 15 seconds. If I could rotate it quicker it might go even quicker. You can then rotate all day but the gauge shows no further change. I read in the manual that only if the vacuum increases to 0.3bar within 20 seconds are the oil seals bad. I started the 024S with one of the WT-22B carburetors. The idle did seem a bit more stable than when I tested it with the WT-194A but I wouldn't put money on it. At one stage I got it idling between 2400 and 2800 rpm for a few minutes. If I tilted the right hand side of the saw up in the air the rpms would rise to the upper value and if I let it back flat on the ground it would sink to lower values. I did a small bit of cutting and when I let it idle it would be around 3000-3200 rpm. I could adjust that down but the saw wouldn't start then with the new settings. I guess the saw is pretty usable as it is. It is just not likely to idle for any great length of time especially if you're moving it but I suppose I can either leave it flat on the ground or if I'm moving press the throttle now and again if I hear it beginning to die. I think I damaged the other WT-22B so testing it might be just adding more confusion (if that were possible). I never get any cloud of black smoke after idling for a while and then going full throttle. It is kind of bluish or transparent. The fuel line and filter on the 024 is new and long. If by breather you mean the tank vent then that ought to cause problems at WOT as well and the problem should appear with time as fuel is used rather than a constantly inconsistent idle. I can test without the vent though. I am afterall desperate at this stage. What's your postal address, Spud?
-
I bent the metering lever in the WT-194A carburetor up to be level with the lip, set the H and L adjustment screws to 3/4 turn out and the idle screw to 2 turns out which is halfway on the tip of screw. After 10 or 11 pulls the saw started with the choke. It then wouldn't start normally as I think 3/4 is too lean and when the choke was open there was then too much air to start. I turned the L screw to 1 turn out and the saw started. I could rotate between 3/4 and 5/4 turns out before it either got too lean or too rich and died. I could get it sound kind of poppy at around 9/8 turns out and then adjust the idle screw to get the rpm 2500-2800 but any settings I would use wouldn't really have any lasting effect.The rpm would vary more widely and upwards especially by having the saw on one side or after returning from WOT.It would inevitably die but I could restart it immediately. I put the 024S back together with a new impulse hose. I see what you meant earlier about the hose sticking out from the back of the tank housing.It has a different design to the one I put in before.It is hard to push it in fully. I took the WT-194A off the 024 and put it on the 024S. It started straight away. It is louder. You can tell from the sound of it that it is a more powerful saw, although that probably has more to do with the cylinder being original than the longer stroke. I turned the L screw out slightly to 5/4 to idle okay but it started to behave erratically as well.If the rpms started to drop I would turn the screw in. It would then slowly go up and at times continue over 3000, so I would turn the screw back and it would go down again.So I could influence the direction the revs would go in by turning the L screw back and forth slightly but there wasn't any real fixed link for any prolonged durateion of time between a certain L position and a certain rpm. Turning the saw on its side was one sure way of getting the rpm to climb. Then I gave up because I was sick of it.
-
I sealed up the two WT-22B carburetors and stuck them in the bucket of water. They showed exactly the same behaviour as the 194A. If I constantly pump I can the pressure up to around 5psi and there is a big stream of bubbles out of both ends of the throttle valve shaft. I was rather hoping to find some way to stop the air leak rather than managing it. I mean you wrote earlier about expecting leakage in the pressure test of the whole saw from 10psi down to zero over 20-30 seconds and not well under. This must classify the air leak I have as major. Maybe there is a reason the stihl manual only does the pressure and vacuum testing without the carb. Maybe they don't care about leaks in the carb. The reason my name is ihatesaws is that adjusting the carburetor screws is the thing I hate the most and has me pulling my hair out. This is probably because with an air leak the saw does not behave in a predictable manner. You can find a carb setting that seems to work and you cut. Next time you try to start the saw it may not start or it might be racing at idle with the same setting. The metering arm seems to be level with the carb body. I see the raised lip you're talking about. The arm seems to be maybe 1mm below it. I can bend it up slightly. You want to make things richer in general so. >>Start the saw up and turn the L screw out until the saw revs drop Won't they start to drop immediately as the mixture is getting richer? Do you mean turn out until the saw revs drop down to like 2000 rpm and it sounds like it is about to die? >>turn back in until they peak and start to drop, undo until the saw drops in >>idle speed again and the engine note sounds sort of poppy Okay but why don't I just set the L screw straight away so that the saw revs at 2500rpm on the tachometer? >>then set the H screw so the saw revs out and try it again. What does revs out mean? I'll be adjusting the H screw to see how the idle is affected or you want me to adjust H at WOT to get near the max recommended rpm of 13000 and then adjust L again to poppy at idle? What would you recommend me to start off with for the idle screw? Two turns out?
-
The company seems to be reputable. I got the cylinder kit off them as well. On the main body of the carb it says WT-194A so I assume it is a walbro carb. The only other carbs I have are the two 22B's. I already saw one of them leaking loads of air out of the throttle shaft and I wasn't able to pressurize the crankcase any easier with it than with the 194A.I'm sure that if I put on the two steel plates and dip it in the bucket it will be a similar story. The other one I think I damaged by firing compressed air into the holes on the metering side of the carb. I don't have an ultrasonic cleaner. Am I right in thinking they are expensive? Anyway I suppose I could put that one back together if it still has all the pieces so I could test how its throttle valve shaft behaves. When I first got the WT-194A I tried it on the 024S as well and although the idle rpm increased a bit as well it didn't seem to be as bad but it was a while back and I don't remember too well. Maybe these saws in general just don't have a very stable idle. You must have alot more experience of them than me though. I doubt I can get a replacement from Sägenspezi for the carb given the amount of steel I've ground off the back and front of the carb at the collar screw holes due to my overtightening. All that messing around with the M5 nuts and the carb boot - a big waste of time I've no confidence anymore that a new 194A would be any better anyway
-
The cover on the fuel pump side of the carburetor does say Walbro. I put in the hylomar behind and infront of the throttle butterfly. I sealed the carburetor with the two steel plates. I could pump up to 10psi and it took about 15 seconds for it to drop to zero with a few bubbles still coming out of the throttle shaft. I then put back in the inlet needle and put the carburetor on the saw, sealing behind it. I pumped up the saw through the impulse hose to 7.5 psi with only two pump actions and it took more than a minute to gradually drop to zero. I could only draw a small vacuum however. I presume this is due to the pump sucking the hylomar away from the shaft allowing air to enter.
-
It is a new carb that came in a box from Sägenspezi in Germany: Vergaser Walbro passend für Stihl 024 024AV AV MS240, 56,50 € - SÄGENspezi It says the carb is from walbro and made to a high quality standard. What if I somehow seal the throttle shaft temporarily with some kind of sealant, put the carb back on the saw with the plate behind it and do the pressure test again? Would that hylomar gasket sealant I have be worth a try? I could try and squirt it around the shaft inside at the throttle butterfly.
-
That is not the exact pump I have. It's broadly similar but at the front you can rotate between In and Out to go between vacuum and pressure. It seems even harder to draw a vacuum than to pump in air so I suppose that supports the case for the carb boot interface not being at fault. I took the wt-194a off the saw, made a second rubber and plate and removed the inlet needle from the carburetor. I used two collar screws to clamp the plates to the carburetor sealing the venturi. I attached the pump to the fuel input line and stuck the carb in a bucket of water.By constantly pumping I was able to get the pressure up to maybe 5psi. This dropped quickly to zero when I stopped pumping. There was a constant stream of bubbles out of both sides of the throttle valve shaft and nowhere else. This doesn't look very good for the throttle shaft but maybe they are all like this. For comparison would you be able to test in a similar fashion any carb you have there from a saw that idles well? Maybe it's just the carbs made for 024/026 that are bad idlers.
-
The impulse hose is in the correct position as shown in your diagram. The carb is fully inserted and making contact with the boot. We've moved on from getting no reading at all. Since I've started using the steel plate, the choke side of the carb is better sealed and I can get the gauge up to 7psi by constantly pumping. It quickly drops back to zero though if I stop pumping. I'm using a pump like this one for the pressure and vacuum tests: http://www.werkstattportal24.de/fotos/r-parts/40.40.34-1.jpg Now that I can get some pressure into the saw it is alot easier to see bubbles of air coming out. I guess that when I pressurize the carb separately I will see how quickly the gauge needle drops. If it is very quickly like when it is on the saw with bubbles only at the throttle valve shaft this would indicate that the main leak is within the carburetor. If on the other hand it is a slow drop to zero I will have to look again at the seal between carb and boot as being a factor as well. I'm in Ireland so you don't have to worry about me landing on your doorstep with a box of saw parts anytime soon. I don't think you can do anymore. Some things you just have to have in front of you to examine in order to figure out what is going on. I'll keep you posted. Thank you very much for your help so far.
-
Well, Spud, I see they don't pay you the big bucks for nothing. The throttle valve shaft does seem to be the culprit (or at least one of them). I tried the pressure test without the metal insert ring but that didn't make any difference. I then put pressure with my thumb on the piece of rubber at the back of the carburetor and I was able to get the gauge needle to move a bit. The metal washer wasn't any good at keeping the rubber pressed against the carb.It is weak enough that you can bend it in with your hands. I made a solid steel plate to replace it. I can now get up to maybe 6 or 7 psi if I pump constantly. If I stop pumping it drops down to zero, certainly within 10 seconds. I poured in the water around the carb and there were bubbles coming from the throttle linkage. On the opposite side of the shaft there were bubbles as well although it is possible that they were coming from the carb-boot seal instead. There is less space on the left side of the carb to see anything. That was with wt-194a. I then put on wt-22b. This had bubbles coming out of both sides of the shaft as well with quite alot on the left side. Would the following work to test the carb for air tightness off the saw? I would make a second rubber and steel plate and seal it at both ends using two long 5mm bolts. I would remove the inlet needle from the metering side of the carb which would allow air from the pump to pass from the fuel pump side into the metering side and from there through the L and H holes into the venturi. I would then stick the carb in a bucket of water and pump to see exactly where the bubbles are coming from. How can a new carb have this problem? Maybe they figure the air leak isn't large enough to be of significance and all carbs are like this? There is a certain constant amount of air coming in through the choke butterfly anyway so a small air leak isn't a problem as long as it's constant? But I seemed to get an rpm increase by lifting the saw or turning it on one side so the air leak isn't constant. >>I would expect leakage from 10psi down to zero over 20-30 seconds and not well under. You mean you'd expect this on a normal saw that works fine? I'm pretty sure the 22b is a compatible carb as both the 024 and the 024S came with one of them. I read somewhere else on the internet too about some guy with a 024 and a 22b on it. I see in the parts manual for the saw that the walbro carbs shown are 110 and 426. In the manual for the 026 there are 427, 590, 195, 155, 403B and 493A shown. What is this compensator thing? A carb with one of them wouldn't fit older saws? Where did you see a carb for £15? I see at the moment you can get a 426, a 403 or a 493 on ebay from the US for $30 including postage. But what's the point if they are all leaky anyway?
-
Thanks spud. I'm afraid I can't give up and put the saw on ebay. I have spent too much time and money already. A positive outcome is required. The carburetor wt-194A is new and cost more like £45 than £15. I have seen cheaper ones on ebay from china but they looked a bit different and had a "compensator" connection????? Is this what you're talking about? The old carburetor is wt-22b. It looks almost identical to the wt-194A. I was doing the "pop off" test you describe a while back with the 22B and it was leaking.I stuck it in a bucket of water and there were air bubbles slowly coming out of the impulse connector. This was with a new carb kit so I thought maybe the carb body was deformed and that was the reason for my idle problem.I therefore decided to eleminate the carb as the source of the problem by buying a brand new one. I since discovered however that the gaskets are only air tight when they are wet. Just now I sprayed carb cleaner in the fuel pump side of the carb, screwed it back up and pumped it up to 7 psi.It seems to hold. I did the same with the new 194A and no leak. I stuck the 22B on the saw, put back on the rubber patch but again no increase in pressure. In with the soapy water and pumping gives lots of bubbles allover the place down at the carb boot. Anyway it is not like I can pump up the crankcase to 10psi and see if it takes 30 seconds to leak out through maybe the throttle valve shaft. I can't even pressurize it to 1psi. Two bad shafts seem extremely unlikely. It just doesn't make any sense. I think I will put the 024 super back together and do the pressure test on that with the carb in place. One thing that might be stopping the carb from sitting properly (during the test anyway) on the carb boot is the impulse connector.I have the pressure pump connected to the impulse hose so the impulse connector on the carb is digging into the side of the hose instead which obviously is not ideal. I suppose I could not have the hose come through the tank housing and out the side instead to the pump. I would love to get a new ms240 out of a shop and do the same test on it but I guess I would probably just end up wrecking a brand new saw I will soldier on.
-
Sorry I've not reported back sooner. It is so demoralizing not making any progress that I only manage to muster up the motivation to look at the saw at protracted intervals. I managed to cut the nut off with a hacksaw.The collar screws seem undamaged. Two new nuts screw on and off easily anyway. It seems that the overtightening caused small pieces of the metal washer and the rubber boot around the collar screws to wear away. I guess this is also what happend to the previous parts that I replaced with this new set. The rubber boot does protrude slightly higher than the outer metal washer. The inner insert ring however has a lip on it which keeps it on the surface of the boot that meets the carburetor. So it would be first this ring, then the boot and finally the washer that make contact with the carburetor. I can't see anything that would be forming a barrier when I put on the carburetor. I made the paper washer and put grease on the boot and the carb, put everything together and took it apart. The grease seemed to have formed a circle on both sides of the paper without any gaps. One thing I have noticed is that the hole in the plastic tank housing is more ovular than circular with the axis perpendicular to a line between the two collar screws being slightly longer than the distance between the screws.The rubber boot and the metal ring tend to deviate from their initial circular shape and take on this ovular shape. There could therefore be a mismatch between this and the perfect circle at the back of the carburetor. I do squeeze the ring back into a circlular shape with a visegrips and I think it deforms more when I overtighten. I've started tightening like you suggested and the boot seems to be remaining more circular. As I had replaced the boot on the cylinder I did the pressure and vaccuum tests as I had before with the piece of rubber between boot and carburetor to make sure I hadn't introduced any new air leaks. It seemed fine on both tests. I then put the rubber after the carburetor and used the old metal washer from around the carb boot to seal the rubber evenly on the carburetor with the two nuts. I couldn't get the gauge to register any increase in pressure or draw any vacuum. I poured in the soapy water the best I could and there seemed to be bubbles coming from the junction between the boot and the carburetor above and later below the throttle linkage and also on the opposite side but it was difficult to see exactly where. (Am I right in thinking that the pressurized air I'm pumping in (through the impulse hose on the cylinder btw) may make it through the three low fuel holes into the metering side of the carburetor but shouldn't make it past the inlet needle into the fuel pump side of the carburetor? Just concerned that the air could leak out the fuel line of the carb.The high fuel hole has a check valve, doesn't it? I fear I may have damaged a different carburetor blasting compressed air into that hole.) So no progress, back to being demoralized I guess .