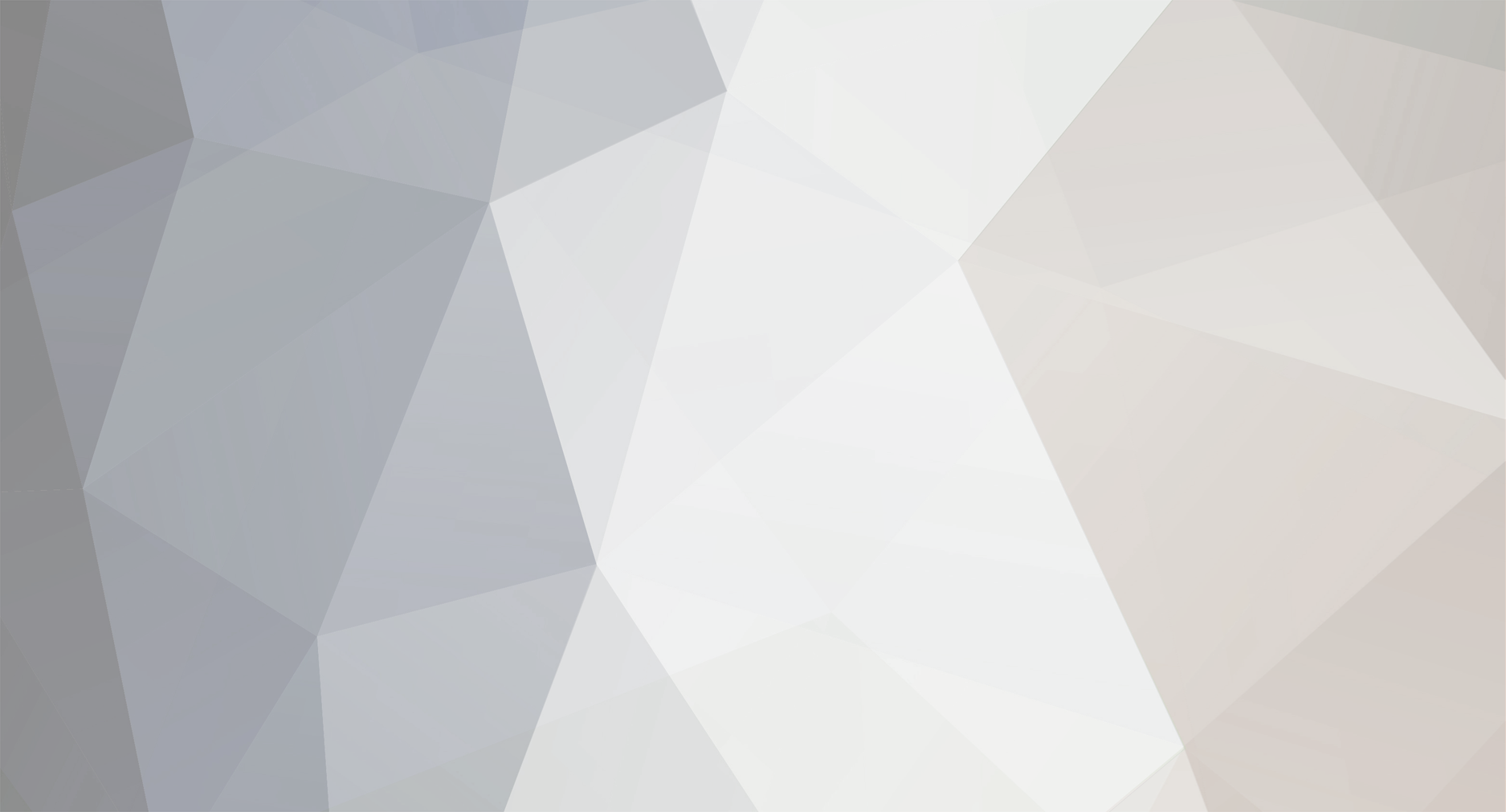
purple badger
Member-
Posts
20 -
Joined
-
Last visited
Recent Profile Visitors
The recent visitors block is disabled and is not being shown to other users.
purple badger's Achievements
Apprentice (3/14)
-
-
Rare
-
-
Rare
-
Recent Badges
-
I've put the 3D printer files up on Cults here so anyone can download them: https://cults3d.com/en/3d-model/tool/jonsered-625-630-670-chainsaw-safety-interlock-throttle-lock Print settings if you're using your own printer are up there too, but also below: Printer type: FDM Time to print: approx 40mins Units: Metric/mm Material: PET-G (ideally) Layer height: 0.2mm Print Thin Walls: must be set to 'On' in slicer settings Infill: 50% Supports: must be set to 'Off' as the part already includes the required supports that can be snapped off after printing Print orientation: As shown in images in this thread Bed Adhesion: Skirt (do not set to Brim or the built in supports will not work properly!) If you don't have a 3D printer then there are print services that you can use on the web to print it for you. I've never used them, but here's a link to a review of the main ones: The Best 3D Printing Services in the UK | All3DP ALL3DP.COM Looking for a 3D printing service in the UK? There are plenty of services offering a variety of solutions. Read on for the biggest players! If you fancy buying your own 3d printed then this was printed on an original Anycubic i3 Mega that is about 4 years old - they currently sell second hand on eBay for around £100-150 and 1kg of filament to print with (which will last you a looong time) is around £15-20 on amazon. The CAD software is free and called Fusion360 and the slicer for preparing your prints is also free and called Cura. Thanks again to all that have helped this come together - hopefully it'll help someone in future fix their saw!
-
Nowt wrong with marking blue and a good scribe!
-
Honestly if I can do it (and I remember the time before the internet, PCs, mobile phones etc) then anyone can - way I see it, every day's a school day and we've got more experience to take advantage of new tech. Also it's not a massive learning curve, the printers are cheap and the CAD software is free (fusion360), it's a no brainer if you're that way inclined.
-
So I fabbed up some hardware today - stuck with the old spring as it worked, just tempered it to keep it springy (got it glowing cherry red under a blowtorch and then dunked it in water) And then fitted everything together - almost impossible to tell it's not the original! Quick test and it works as it should! VID_20240127_122107.mp4 So thanks to everyone and @adw in particular, who really went above and beyond helping with this project - without you mate this would never have been possible. That's now one jonsered 630 made whole again! I'll get the 3d printed file up on thingiverse or whatever when I get home and I'll post a link to it here so others can print the part if they need to - huge thank you guys, we've brought an obsolete part back from the grave and hopefully kept a few 625s, 630s and 670s going longer (maybe a few other models too - who knows!).
-
Guys here thought I was mad going for something that old, but then I've been running the 041 since new. Also like I said to them I loved those 630s when I got to use them and the new saws don't have any decent heft to them - it sort of feels wrong and flimsy! Besides all I need it for now is some logging and a bit of clearance now and again... It's not like I'm a pro using it day in and out. Still... It is probably madness and I should have forked out on something newer! Yeah those are my favourite gloves - got a new pair before Xmas but it's like having balloons on your hands, you can't feel anything! So still using the old ones. (If anyone has any recommendations for decent hard wearing work gloves you can feel stuff though then don't be shy, please let me know!)
-
So I had a few minutes today to fab up a rough spring and test the prototype part I think the spring fits like this I then used a nail as the main pin and (spoiler alert if you don't want to watch the vid) it seems to work like it should. VID_20240125_191930.mp4 So I splashed out on a whole 17p and printed the proper part in black PET-G which I'll fit tomorrow.
-
Yeah it changes the way you think about things for sure - once suppliers get their heads around the tech it will be the way it's done, I mean that 3d printer was only £179 a few years ago. It paid for itself in a couple of weeks and it was a Xmas present - what more could you want! Chain brake definitely - one of the lads broke one and had him up and running the next day (although replaced now with a 'proper' part when it came in stock). Fuel tank ... there's flammable fuel safety issues there so I wouldn't do it, but no reason a manufacturer couldn't. Frankly after a few years I'm sold on the whole 3d printing idea and I'm now looking at a metal printer (£1k+) to do custom engine parts as it should pay for itself fairy quickly. Love it - white PLA is the cheapest for prototypes, but comes in any colour you want mate, even 'unicorn rainbow' 😂
-
Yeah I said that when I was given this one for xmas.... 1 month later after having fixed a thermostat bracket I'd snapped on my hot water tank at home using it (was quoted £120 for the whole replacement thermostat + bracket part and 3 months wait by local supplier as it was during Covid...) and I suddenly understood that it was going to become essential. I then moved it into the shop and haven't looked back. It's one of those tools that you don't know you've always needed until you have one - it sort of requires a mind shift and then you look at the world differently if you know what I mean!
-
No, whole thing was probably a couple of hours of work and if I'd had the actual original part in my hands it would probably have been nearer an hour. If you're starting out the CAD might take half a day or more, but you learn it really quickly and rapidly speed up...and of course once you have the model it's literally seconds to click print and get another part printed. However, like anything it's what you put in that you get out - you do have to learn the CAD, but any half practical person can do it easily, especially if you have lathe/milling experience as it's just cutting and extruding. For this one I just traced round the photo on the computer to get a 2d outline drawing, scaled it so it was the right dimensions (literally one click), extruded it by thickness of the part so it became a 3D block (again one click), then cut the various holes and channels in it (e.g. draw a 2D circle and then extrude it as a 'cut' to get a hole in the part etc.). That's the basic process. Basically as long as you are practically minded it's simple. Slicing is literally just adjusting a few settings for the material you're using and then clicking 'slice', once that's done printing is pressing another button. OK there's a little more to the whole process that you have to think about (supports for overhangs etc.) but that's it. Simple - I honestly don't understand why more workshops don't have FDM printers, as if I can do it anyone can.
-
OK so I couldn't resist spending an hour over lunch finishing the prototype and printing it. @adw huge thanks as I did have a couple of dimensions off between 1-2mm, but they're now all adjusted. Anyway, I added breakaway supports to the model that are necessary to print the slot as it overhangs and otherwise my printer would be printing in thin air. Then next job was to slice it ready for printing (took 35mins and cost 13p). The prototype is printed in white PLA to keep things simple and quick, you'll see it's also hollow to keep things cheap (20% infill). Once fit has been checked, the final model will be printed in black PET-G at 100% infill (solid not hollow) so it's tougher and looks like the original (although you could have it in any colour or finish you wanted including wood or metallic 😁). 35 mins later and it's done - the breakaway supports are snapped off - with the final model you should probably really clean it up better with a knife and sandpaper but this will do for a prototype! Then the final prototype is measured up to check against the original model in the photos @adw kindly supplied. Pretty much spot on from what I can see (and yup, I found my favourite callipers!) Job done - I always find it mad that this is now possible with cheap modern tech - when I think what things were like when I started and now you can draw something on a a thing called 'a computer' and print it out into the real world on another thing in your workshop in half an hour - total madness, but puts a real grin on your face when you see something emerging slowly on the print bed! Anyway, I'll try a test fit at the weekend if I get time - it'll probably need a little more fettling with some dimensions but it's definitely getting there!
-
@adw Absolutely perfect, thanks! Right will check tomorrow if I got those dimensions correct. I'll also try to model up a spring jig, might have wait until the weekend as it's all kicked off today.... Looked like the rest of my week is going to be more busy than is comfortable. Guess it just happens sometimes... but hope it's going better with you!
-
You and me both mate. Out of interest how easy is it to get the interlock and spring in/out of the handle? I've yet to actually look at how to get in there and I don't have a service manual for this saw.
-
Didn't realise you were pulling it out of the saw each time! That's above and beyond.... Honestly mate - if it's a load of effort don't worry and I can figure it out, you've done enough already.
-
So the prototype model is ready - not quite printable yet as I need to add some breakaway supports to a few areas, but almost there. @adw Thanks for all your help - not sure if I got the slot highlighted with a red circle in the pic right - did it look like this? I've also made a guess at the depth of the slot in the main handle, pretty sure that can't be too critical as I imagine it's just for the spring. We're well on the way to bringing an obsolete part back - thanks for all the contributions.
-
That's the badger - yup won't forget, I'm just hoping that it's fairly obvious how it fits together as I'm missing both arm and spring. Should be reasonably easy to create a spring from a bit of piano wire though. That's one dusty filter and carb - always amazes me that people don't clean them out more regularly themselves. I had a mates on the bench a few weeks back and it was clear he'd never touched it! Those were the days, mine are probably of the same vintage passed to me by an old engineer - they never run out of battery (because they don't have one) and you can't accidently click the digital re-calibrate button and screw everything up. There is literally no reason I can think of for modern digital calipers! 3d printers are the dogs. I never thought I'd say that, thought It'd be little used when I got one for the workshop, but it's one of my most useful bits of kit, it's even been used to replace broken water tank, car, bike and washing machine parts at home. An FDM printer is a brilliant bit of kit for £200ish if you spend the time to learn CAD. The plastic for printing is only £15 per kg so it's cheap, most printed parts end up costing way less than £1. More importantly, when you break some small important plastic something you don't think 'oh cr*p!' - you just go 'aw well, I'll print another' - that's worth it's weight! The part will be as strong as the material that's used to print it. In this case, it'll be plenty strong enough in PET-G plastic, but you could use ABS or Nylon if you wanted 'stronger'. PLA would be stronger still (hard), but brittle with it, so not a good choice for anything other than a prototype. The enemy is heat as the parts would deform, but PET-Gs only going to start deforming at 75*C so you're going to have bigger problems if the handle is getting that hot 😂