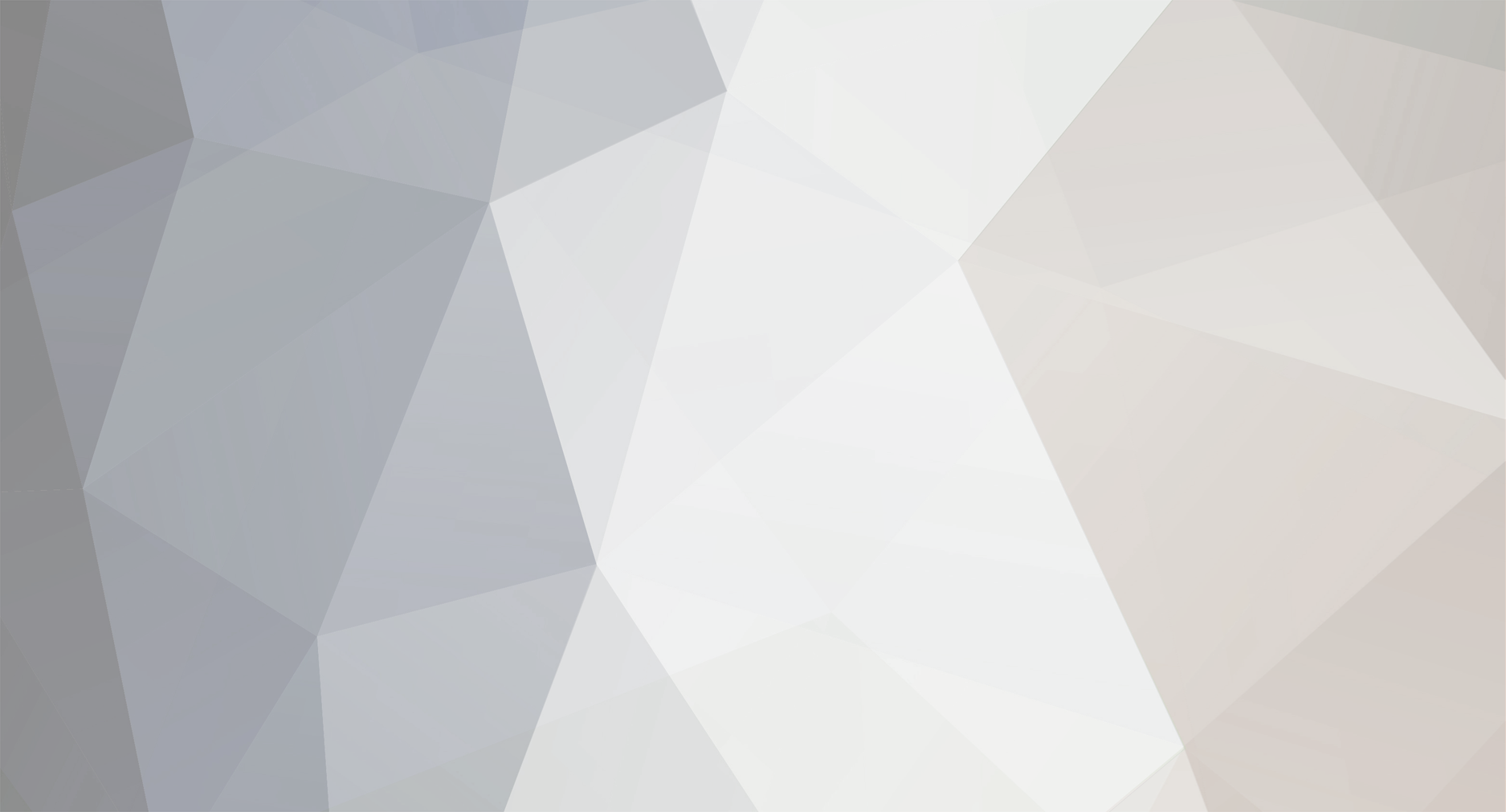
FlyFishn
Member-
Posts
22 -
Joined
-
Last visited
Recent Profile Visitors
The recent visitors block is disabled and is not being shown to other users.
FlyFishn's Achievements
Apprentice (3/14)
-
Rare
-
-
-
-
Rare
Recent Badges
-
I looked up the 4310 and it looks like it is a European market saw only. I'm in the US so that won't work. We have an Echo, I want to say it is about 50cc with an 18" bar. I will have to check and see what the model number is. It is relatively new - bought 2 years ago and only used a couple times. I don't particularly care for the saw. It does not have a fuel primer button. We did use it last weekend and I had to open the air filter to prime with gas straight in the carb to get it to go. Overall, I am not real sure what to make of Echo saws. Historically I would have never considered them. Someone else in the family bought the one we have and had heard good things about them. I had someone else say good things earlier this week about them. So I am more inclined to give them a chance. I suppose if people here on the forums are recommending them there is a reason. No matter what brand, I do know there is a difference between consumer grade and professional grade - and the price points show that. Looking at the US market Echo line-up - the CS-361 is 35.8cc and 8.4lbs. That sounds about right for what I was thinking on sizing. They spec it with a 14" and 16" bar. CS-361P Rear-Handle Chainsaw | ECHO WWW.ECHO-USA.COM Professionally productive. Learn more about the CS-361P and other chainsaws today at ECHO.
-
In another thread I was asking about larger saws, so I'll keep that subject there. I am also looking at smaller/lighter saws. I was originally thinking something at most 40cc, maybe in the mid 30's. However, looking at the Husq and Stihl options they dont appear to have a professional grade saw that small with a rear handle. I've run a top handle Stihl before, and although I really do like it for cutting down smaller limbs, I don't think its the right type of saw for how I am intending to use it. I still think a rear handle traditional saw is going to work better. Dad has a small stihl I've used and worked on before. I don't recall the model, but it is a homeowner grade saw for sure. That is what I don't want. The bar length I am wanting is 14" with possibly a 16" as an option. The goal is to have a lighter, more maneuverable saw. Down the road a top handle is on the list, but I'm not sure I want to go that route this round. What thoughts do you have?
-
Can you explain what you mean about the bigger Husqvarnas in your experience? I having not run a bigger saw, personally, than my 455 rancher I don't have much to go off of. The 455 rancher I got back around 2012, lightly used, so the last over 10 years that's been what I've grown to know. That isn't to say the newer saws are that similar to what I have, but my experience with Husqvarna has been very good. So I am tempted to stay with them. Stihl is another possibility. I haven't done much digging on saw brands recently, but many years ago Jonsered was up there on recommended saws. I see they went out of production in 2022 and were, at least for the last period of time of their existence, a subsidiary of Husqvarna. I don't recall that being the case back 10-15 years ago, but I can't remember much other than the brand name. There are some knock-off brands on the market, also, that seem to have surprisingly good reviews/performance. One is blue that is a knock-off of Stihl. I am not sure I could get myself to go that way, but then again - for as often as I would need a heavy saw that might still get the job done.
-
All, I'm doing some digging on saws and have a question on cutting bigger trees - including oak and ash. In the midwest here needing more than a 36" bar is a rare thing. Our crew took out a 64" trunk diameter tree last week that was a real odd-ball. I am not sure what variety, I didn't cut on it. The other trees we worked on seemed pretty soft to me. My saw is a Husq 455 with a 24" bar and skip chain. On cutting down some of the trunks I had to cut from both sides. I am guessing some of them were in the 30" range. For as much as I do that, the saw I have does the job, but it is under powered. What I would like to do is get a heavier saw that will have the power to get through wood a 36" bar can cut with decent power. On the rare occasion I'd like to get a bigger bar on there if the need arises, but in that situation I would probably have a bigger saw - stihl 661 most likely - to handle it. Its just with one saw and several trees being worked on at the same time trying to use one saw for everything slows things down when it happens. Is a saw like the Husq 592 xp up to the task? The recommended max bar is 36". So that meets the main criteria I'm looking for. Other than slowing down with dragging a longer chain through more wood and quicker clutch wear maybe - is there anything else to really be concerned with? I'm thinking if I double up with a smaller lighter saw with a 14" or so bar then the one bigger heavier saw I can cover all my bases. I'm not a fan of swinging the 455 all day on limbs when I don't need it, but then it falls short on most of the bigger stuff.
-
Excellent post. Thanks. Though doable, this makes the task a lot more complicated on the numbers. That might also explain the low cutting on the last 2 chains, but again - I didn't put any science in to the guide depths before. I can tell you the one I didn't use measured .044" and one of the ones I did use (after using) measured .043" - that was the one of the two I ran that time that cut best, but not great. That would seem to align with the progressive cutting you mention. However, without a way to measure it (is there a triangular formula of some kind that takes in to account the width of the distance between the cutter and guide?) it is a "cut to test then regrind" process - and somewhat defeats the purpose of shop sharpening.
-
Thanks for the thoughts. The measurements I gave of .044, .050, and .055 are the depth of the guides from the plane of the cutters - those weren't chain "gauges". All the chains I run on this saw are .058". I am not sure what the other saws are, dads is a small stihl that runs .325" and we just got a Dewalt battery saw - I haven't looked at it close enough to see what it is but either .325" or 1/4". I don't think any of those chains are even close to interchangeable - the Dewalt and the Sthil are different bar lengths so it would be pretty obvious.
-
Sharpening chains is a waste of time? Another hobby of mine is knife sharpening. I suppose I won't bore you with the waste of time in the process all the way to honing with balsa wood a diamond spray. Joking aside, sharpening is imperative to properly operating cutters of any kind - knives, mower blades, saw blades, axes, chisels, you name it. I'm a believer an operator of something should know how to operate it. In the example of a chain saw - the thought of running the chain to oblivion, tossing it in the can, and repeating with a new one really grinds me. I know full well there are people out there that do that, but think of the material inefficiency - if you can get around 10 grinds out of a chain and toss one in the can when it gets dull that's wasting 90% of the life of the chain.
-
The chain I ran before that cut the best of the two was .043" on the guide. So I am guessing the "standard" that these chains should be is .050". So I ran one at .050", another at .055", then a third that I didn't use (still sharp ready to go) measured .044" so I left it. That gives me what I am assuming to be the "standard" +/- .005" to have 3 different levels of aggression on the cutters to see what works. How I did it is with a straight edge and a feeler gauge. I set out to make a "tool" but when I had everything set up I figured the straight edge + feeler gauge was easy and "good enough". Next time I cut I will note how each cuts and then when I resharpen I'll go to what ever measurement that points to on this set. Every type of chain is different. I did label each of the 3 so I know which is which when I grab them out of my box. The saw got the .055" so that will be first up. Trying to hold the straight edge to clamp the feeler gauge with one hand and take a picture with the other was a challenge. The name of the game is to get the straight edge across the points of two cutters, then check the guide under the left-most cutter. Grind to spec and lock the stop, then run all the guides to the same spec. Repeat for different chains (same type or different type - every chain wears differently and sharpens differently) Tools used.
-
I've run the set up since 2013-ish. It's not the long bar. For several years I had the place I worked at the time sharpen my chains. Down the road I got my own machine to sharpen. The saw has cut fine with the same skip chains on the same bar. I'll come up with a method to dial in the guides and go with it. Unfortunately, I don't have any wood right here to test cut on so I'll figure up a starting point on the depth based on what I can find, make a guide to that, and go with it, then when I get to cutting next I can tweak from there. Its easy to go down on the guide to make it more aggressive, not so much going back the other way without wasting cutter life. Of the 2 chains I ran recently the previous one cut better. I suppose I can get it in the vice and put a feeler gauge on one of the guides to see what it measures at as a starting point, then maybe go another .005-.010". That might be the best route to start with. I don't know if an extra .005-.010" would be that noticeable, but if going an additional .025" is too much then at .005-.010" more I am not left with a chain I can't use in the field.
-
Hijacking my own thread here... Re: 2 strokes making a "come back" - Im not sure how much many of you have paid attention to the Marine industry. However, just as every other industry, manufacturers of Marine engines have been clamped by emissions regulations. That made 2 strokes of the past go by the way of the dodo bird. Nissan, Mercury, Tohatsu, and the list goes on - they all did away with their 2 strokes in favor of 4 strokes. Back in the early 2000's we got a 60hp Merc with our pontoon boat - it was already a 4 stroke at that point. Until Evinrude (what Johnson merged in to - it was Johson/Evinrude for a while, then went all Evinrude - under BRP Marine) was sold out (they merged with Merc somehow) around the Spring of '20 they were the only "mainstream" outboard manufacturer still producing a 2 stroke. The way they were able to comply with emissions was their computer control with fuel and oil injection. Spring of '19 we upgraded another boat from an 80hp Merc 2 stroke from the mid-80's to a 75hp Evinrude ETec - one of the computer-controlled EPA-compliant engines. Aside from the fact it is hard for me to work on (need a computer and proprietary software to do much) - I do like it. The fuel efficiency is amazing compared to another smaller boat/motor that uses a Johnson 25hp 2 stroke ('93 model engine) - and its 3x the HP and the boat goes 3x the speed. Running straight gas in the ETec is good also - that means I can share tanks with the 2 bigger boats and generators. If I have to mix for the smaller engines (we have about 4-5 - 25hp down to... I think the small one is 4hp) then I can, but stocking up on several tanks at the lake I can cover the majority of things with straight gas. That and common fuel fittings makes swapping tanks pretty easy. From a maintenance perspective - I would like to see more 2 strokes. At some point, which has been pushed pretty far down the road now, I want to upgrade boats with a ~20ft aluminum fishing boat (full weather enclosure) with a 150-175hp outboard. Since Evinrude went under things apparently went all 4 stroke. I haven't kept up with the merge with Merc, so I am not sure where that line up will lead. Hopefully things improve with product offerings, though. Weight-wise a comparable HP 4 stroke outboard is significantly heavier than a 2 stroke. Add to that the maintenance and I'm not a fan of them. As to other industries gaining momentum with 2 strokes - I would be very curious how things go. If Evinrude could do it there is a way. Though, personally, I am not a fan of the technological mountain involved with the computerized systems as that is the complexity of society and innovation going the way of making the "do it yourself'er" obsolete. How is a home mechanic going to replace a fuel injector, for example, when it is a Canbus device that has a computer address and the only way to program the computer address and calibrate is with proprietary software that a major corporation keeps tight under the pay wall of "you must come to us for service"? Efficiency and clean-burning are good things, but wheres the balance? Back 30-40 years ago the operators manual of a car showed you how to time the distributor. Now they have warning labels plastered all over them about not drinking the battery fluid etc. Wheres shop class in high school - where you run table saws, radial arm saws, band saws, learn how to weld and run an oxy/acetylene torch? Did we really evolve as a society this far? We have a plaque hanging in one of our buildings at the lake that states "Livin' can't be simple anymore. They's too many gadgets".
-
Thats the best part of machine sharpening - everything on the chain is the same when you're done. My concern isn't uneven'ness of the cutters - the cutters aren't chewing enough wood = less aggressive cutting. It works fine, but I felt the last 2 chains were too slow-cutting. On my dads saw (not here, .325" pitch) I ran the guides down then test cut and ran the guides down some more then test cut until I got it where it was right. On a one-off that is one thing, but going through 3-4 chains in a row I'd rather throw a gauge of some kind across a guide to dial the one in, then run the whole chain, then set up on the next chain (dialing in a new stop position). I will see what I can come up with. I'm thinking a plate with a weld bead as the depth peg would work for as small of a difference in height we're talking - .025"-.050" or so. Plus I can tweak the measurement to fit different chains/applications (full chains less aggressive than skips for example).
-
Like this? Oregon 0.025 in. Drop-Center Depth Gauge Tool and Flat File for Saw Chain | Oregon Products WWW.OREGONPRODUCTS.COM This tool makes it easy for you to set the depth gauge on your chainsaw chain. Includes a .025 inch drop-center depth... That is a guide for filing - it stops a file at the proper setting. It doesn't give you an indication of how far to set a grinding wheel on a machine.
-
I'm noticing my chains don't cut uniformly. The last 2 were sharp, but they didn't seem to have quite the bite. My assumption is the guides aren't at the right depth. My usual method is to dial in the cutters uniformly across the chain, then take a bit off the guides. How I knock the guides down is with a wide flat ground wheel on the machine - I can use the depth stop the same as the cutters - so every guide comes out the same. At the moment I don't have a good way to measure the guides with respect to the cutters - and I presume that is my problem. I'd prefer to do everything on the machine since I can index the chain and set up the stops. Question - is there a method that any of you have to dial in the guide depth? I have a micrometer (.0001" precision) and digital calipers (.0005" precision) - but I can't get them in place to grind and measure set up on the machine. If I could - I could set a plate across the 2 adjacent cutters with an opening over the middle then drop down from the plate as a reference to the guide, subtract the plate and have my measurement. Maybe a screw gauge is on order? IE - make a plate that will straddle 3 cutters with a screw peg to set at the proper guide depth like a micrometer, set to proper depth, then grind to eliminate the rocking of the plate on the peg? That actually sounds like a neat method as long as the peg could be locked in place. Or make a couple gauges with fixed peg dimensions so there's no knocking out of adjustment or adjusting for new settings, just swap gauges for proper depth per what ever the chain needs.
-
Interesting. Thanks for the link. I looked at that close to see how it was set up. The rivets on the nose are not flush rivets. It is a milling bar so the tip is not part of the cutting portion - it is clamped in the mill. So for that application it would not matter if the rivets aren't flush. For burying the bar in wood the rivets would have to be flush with the face of the bar (which should be narrower than the kerf so it is easier to pass through the kerf). I guess one thought would be to modify the nose section/rivets and work them flush.