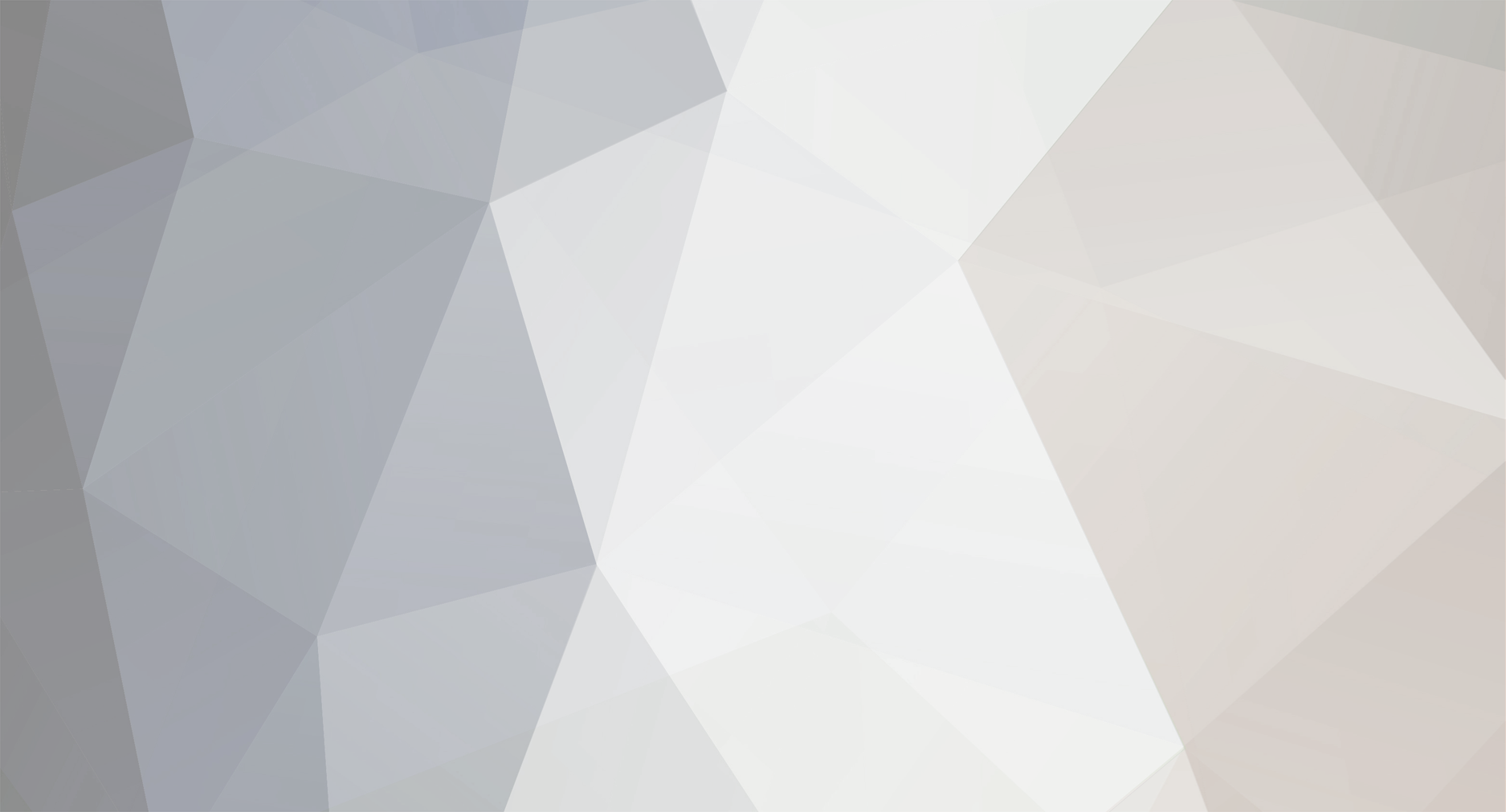
DaveyCrockett
Member-
Posts
33 -
Joined
-
Last visited
Content Type
Profiles
Forums
Classifieds
Tip Site Directory
Blogs
Articles
News
Arborist Reviews
Arbtalk Knot Guide
Gallery
Store
Freelancers directory
Everything posted by DaveyCrockett
-
Husqvarna 435 cylinder/ piston fault or something else?
DaveyCrockett replied to DaveyCrockett's topic in Chainsaws
New genuine ignition module fitted and it's running pretty good. Max RPM a bit slow and it has a little hesitation on acceleration, but a tune up tomorrow should see it right. Thanks to everyone who contributed to the thread, especially ADW who's diagnosis was spot on. DaveyCrockett- 38 replies
-
- 3
-
-
- husqvarna 435
- non runner
- (and 3 more)
-
Husqvarna 435 cylinder/ piston fault or something else?
DaveyCrockett replied to DaveyCrockett's topic in Chainsaws
I didn't measure gap before removal, but it looked sensible. I set it at 0.3 mm putting it back. A new module is on order. I will report back the outcome. You have had some pretty weird issues over the years. It seems like all the testing methods for ignition modules are not 100 %. What do people regard as the most reliable tester and is there a better way?- 38 replies
-
- husqvarna 435
- non runner
- (and 3 more)
-
Husqvarna 435 cylinder/ piston fault or something else?
DaveyCrockett replied to DaveyCrockett's topic in Chainsaws
I'm leaning in the same direction. Although the piston and cylinder are far from a thing of beauty, and in a formula 1 car engine, internals like this would hit the bin, this is a consumer grade chainsaw and I don't believe what I have seen would stop the saw running completely. The ignition module however ... I can imagine things inside which I can't see, that could easily cause the problem.- 38 replies
-
- husqvarna 435
- non runner
- (and 3 more)
-
Husqvarna 435 cylinder/ piston fault or something else?
DaveyCrockett replied to DaveyCrockett's topic in Chainsaws
Yes they are visible through the exhaust port with the cylinder assembled. Here is the inlet side of the piston. The scratch above the ring groove I did removing the ring😳. Top of exhaust port looks perfect.- 38 replies
-
- husqvarna 435
- non runner
- (and 3 more)
-
Husqvarna 435 cylinder/ piston fault or something else?
DaveyCrockett replied to DaveyCrockett's topic in Chainsaws
There was a little debris in the strainer, nothing horrendous. Did you mean - both flywheels and coils CAN be faulty?- 38 replies
-
- husqvarna 435
- non runner
- (and 3 more)
-
Husqvarna 435 cylinder/ piston fault or something else?
DaveyCrockett replied to DaveyCrockett's topic in Chainsaws
My trouble is that every part I look at, I think, well that should probably work. But ignition and engine together (forget the carb) - nothing ever looked less like a working saw 😩- 38 replies
-
- husqvarna 435
- non runner
- (and 3 more)
-
Husqvarna 435 cylinder/ piston fault or something else?
DaveyCrockett replied to DaveyCrockett's topic in Chainsaws
Carb was pressure tested before and after disassembly. Needle valve holding 15 psi and reseating and holding pressure when pressing purge bulb. I just have the original flywheel and ignition module. I believe they are correct matched parts. See earlier post for part numbers. Behaviour always the same, on cleaner or carb. Fires but runs down in 1/2 second, no power at all. Crankcase passes vacuum and pressure test too.- 38 replies
-
- husqvarna 435
- non runner
- (and 3 more)
-
Husqvarna 435 cylinder/ piston fault or something else?
DaveyCrockett replied to DaveyCrockett's topic in Chainsaws
The ring location pin seems solid. I've tried to move it with tweezers and a strong magnet. When I strip the saw everything is very wet. I think it is unburnt fuel from missed ignitions rather than running rich, but could be a carb issue. The exhaust when it fires seems on the smoky side, but the saw is so far off running properly I'm reluctant to judge it like a running saw and blame richness. The fuel mix is fairly recent - a few weeks old. It does fire on carb cleaner for 1/2 second but seems to make no power. It doesn't scream away for a couple of seconds like some things do, that gives you confidence compression and ignition is right. I believe it had fuel in the metering chamber, but brain was not thinking leanness at that point, because of wet engine internals.- 38 replies
-
- husqvarna 435
- non runner
- (and 3 more)
-
Husqvarna 435 cylinder/ piston fault or something else?
DaveyCrockett replied to DaveyCrockett's topic in Chainsaws
Well I can measure a couple of resistances as well as the spark test. HT to ground = 1.6 kOhm, cut out contact to ground = 60 kOhm. Doesn't prove much but HT lead good in this case.- 38 replies
-
- husqvarna 435
- non runner
- (and 3 more)
-
Husqvarna 435 cylinder/ piston fault or something else?
DaveyCrockett replied to DaveyCrockett's topic in Chainsaws
It was in right. I first saw both sets of scratches through the exhaust port, and I did check the arrow on the crown was pointing front.- 38 replies
-
- 1
-
-
- husqvarna 435
- non runner
- (and 3 more)
-
Husqvarna 435 cylinder/ piston fault or something else?
DaveyCrockett replied to DaveyCrockett's topic in Chainsaws
The only tests I can really do for the module is to jump the normal gap 0.5 mm which gives a fat blue spark and it jumps a modified plug with a 2mm gap but I know the stresses on the module are higher when it makes the spark jumps under compression. It sounds like I should take a punt on a new module. I can always send it back if it doesn't work. I have taken the taken the saw apart again to check ring wear and to provide some pictures. I've had it apart so many times now it didn't take long! The ring gap is 0.3 mm with the ring in the bore, so negligible wear. I think the scratches on the front of the piston are nothing to worry about. The blow past, wouldn't usually worry me if the saw was running. The scratches on the back of the cylinder are I think caused by burrs on the ends of the piston ring. It's not nice but I don't think it would stop the saw running.- 38 replies
-
- husqvarna 435
- non runner
- (and 3 more)
-
Husqvarna 435 cylinder/ piston fault or something else?
DaveyCrockett replied to DaveyCrockett's topic in Chainsaws
This is a Husq 435 II I have used the parts lists from L+S engineers website for numbers. The flywheel has the number 580 27 98 cast in the back, The parts list for series II quotes 580 27 98 01. The ignition module fitted is marked 579 63 88-02. The parts list for series II quotes 579 63 88-03. Is this okay? I think the last two digits are just a revision number. I have checked lists for 435 and 435E. They use a different parts for flywheel and ignition module. I think I have the right parts fitted.- 38 replies
-
- husqvarna 435
- non runner
- (and 3 more)
-
Husqvarna 435 cylinder/ piston fault or something else?
DaveyCrockett replied to DaveyCrockett's topic in Chainsaws
I was guided by the book by Paul Dempsey which quotes 90 psi as a working limit, but I think you could be right. There is no figure quoted by husqvarna.- 38 replies
-
- husqvarna 435
- non runner
- (and 3 more)
-
Husqvarna 435 cylinder/ piston fault or something else?
DaveyCrockett replied to DaveyCrockett's topic in Chainsaws
I have considered ignition module, but most I have seen failed are either totally caput or fail when hot. The wrong module hadn't crossed my mind.- 38 replies
-
- husqvarna 435
- non runner
- (and 3 more)
-
Husqvarna 435 cylinder/ piston fault or something else?
DaveyCrockett replied to DaveyCrockett's topic in Chainsaws
It still had the alu heat shield to seal it so any leak would be very minor. Most of the tuning effect from the muffler would still be there. This saw hasn't got a flat spot in the power band - It won't run at all.- 38 replies
-
- husqvarna 435
- non runner
- (and 3 more)
-
Husqvarna 435 cylinder/ piston fault or something else?
DaveyCrockett replied to DaveyCrockett's topic in Chainsaws
Hi Khriss, Actually the exhaust gasket was missing, but I didn't think that would effect how the saw ran.- 38 replies
-
- 1
-
-
- husqvarna 435
- non runner
- (and 3 more)
-
I have been trying to diagnose a fault on a Husqvarna 435. The saw was initially running poorly and hot. It was taken for a serviced by a local company after which the saw wouldn't start. It was taken back. The company swapped the carb which didn't fix it then they said it might need a new piston and quoted a high price.. The owner brought the saw to me. The saw will fire but won't run for more than 1/2 second, even with direct priming with carb cleaner. The plug has been changed and it produces a healthy spark which jumps a gap. Compression was measured at 120 psi. The piston ring is free and piston skirt un-scored. There are some mystery scratch marks on the back of the cylinder opposite the exhaust post and on the front of the piston below the ring but they seem quite superficial and not enough to cause a problem. On removing cylinder, there were no foreign objects, nothing stuck in the transfer port, manifold and cylinder seemed in reasonable condition. There were dark marks on the piston skirts so I think there is some blow by past the ring. Just in case, I stripped the carb to look for obvious faults but all looked clean and in good condition. I have also tried every tuning point of H and L including the standard tune in am effort to get this saw to run at any RPM. Has anyone any suggestion where I should go from here? My feeling is that it needs a new piston or piston and cylinder but I am not at all sure. Thanks for any help
- 38 replies
-
- husqvarna 435
- non runner
- (and 3 more)
-
This problem is fixed now so I thought I would tell you the outcome. I decided to buy a coil (ignition module) as this was the cheaper option, but thought I would check out the coil resistance first. I found that the HT lead was open but the resistance from the HT screw to ground to the was 7.6 kohm. I replaced the HT lead expecting it to run, but no. I bought a pattern coil, and it was a pretty bad fit. I had to shorten the HT screw and plastic surround where the lead comes out, but eventually got it in. The spark jumped 3 mm (orange looking spark) but saw runs OK. It looks like the flywheel magnets are good after all. Thanks for you help, Dave
-
That's already done Stubby, but I haven't checked the grounding on the module so I'll clean everything up, reset gap and try again.
-
I'm working on an old Stihl 034 AV electronic quickstop. I have had it fire on direct priming with carb cleaner but not at all reliably. Sparks well over 0.5 mm gapped plug out the cylinder but can't jump a 3 mm gap. In my experience ignition modules fail totally or when they get hot so I'm thinking weak magnets in the flywheel. What do people think is my best move? Is is worthwhile taking a punt on a second-hand flywheel? A new one is about £95. Should I buy a pattern module just to get it eliminated? Does anyone know how to test the magnet strength or get them re-magnetised? Thanks for any advice.
-
I fixed this saw about 15 months ago. It was leaking from the clutch side seal. It had broken the little metal plate that sits over the bearing at the bottom of the barrel. Where the bearing/seal sat the metal of the barrel looked a little shiny unlike the other side which showed the cast finish. The plastic of the shell was maybe a little scuffed but not bad. I fitted new bearings/seals and new little plate. Pressure and Vac tested OK. Job done. Now it's back leaking from around the clutch side seal. I used Loctite grey silicone SI 5660. I didn't put any around the outside of the bearing/seals as there was no sealant there before. Is the way to go to try to reseal with a coating around leaking bearing seal or as it looks like the plastic shell and barrel might now be oversize on the clutch side, is this saw history? As a general enquiry, the sealant I use doesn't seem to bond very tightly. I'm guessing I should be de-greasing the surface and maybe abrading it slightly. What is the best practice to make sure the stick stays stuck? Any advice welcome, Thanks, Crockett
-
Pattern piston kit install - advice needed
DaveyCrockett replied to DaveyCrockett's topic in Chainsaws
Openspaceman, If I'd known I would have just got a piston, but I read that Stihl don't sell them alone, so thought I had to buy a kit, and price drove me East. My OEM cylinder doesn't seem too bad. Tried giving it a scrape with some brass, but that wasn't too effective, so tried Plusgas and 600 grade wet and dry which was a bit better. What is the right way to clean it up? I'm just trying random stuff here!- 19 replies
-
- aftermarket
- cylinder assembly
-
(and 2 more)
Tagged with:
-
Pattern piston kit install - advice needed
DaveyCrockett replied to DaveyCrockett's topic in Chainsaws
I'm not sure I have all the tools to smooth off ports. I don't think they spent much time finishing off the casting in China. It's especially horrid around the impulse port. I've had a little go with needle files. I have got a die grinder in the cupboard but have never really used it. I'm guessing I would need to buy some burrs. I've got a few mounted points but not sure that's the thing to use. I've never done any work on engine internals, just fitted parts together, so please forgive my high level of ignorance. The pot is on now, but I'm waiting for more parts from my very slow local Stihl dealer, so might be prepared to have a go.- 19 replies
-
- aftermarket
- cylinder assembly
-
(and 2 more)
Tagged with:
-
Pattern piston kit install - advice needed
DaveyCrockett replied to DaveyCrockett's topic in Chainsaws
Thanks for the help Spud and all who replied.- 19 replies
-
- aftermarket
- cylinder assembly
-
(and 2 more)
Tagged with: